You can get your white paper here:
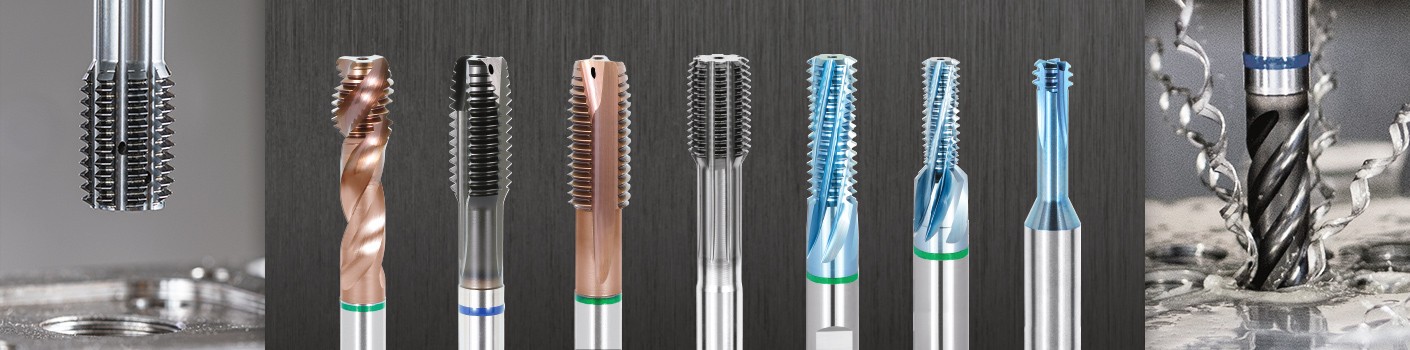
Process Reliability for Thread Generation: You need to know this for the generation of internal threads
Learn all about the various internal thread generation processes
In production technology, the generation of internal threads ranks amongst the most demanding of all machining tasks.
Thread generation often takes place at the end of a production process, and is thus critical for the quality of the workpiece. Defective threads generally mean high additional costs. Process reliability is absolutely the top priority, but short cycle times and cost-effective production processes must also be achieved.
Folgende Gewinde-Herstellungsverfahren finden Sie hier auf einen Blick:
1. The Manufacturing Process: Thread tapping
2. Herstellungsverfahren: Gewindeformen
3. Herstellungsverfahren: Gewindefräsen
4. Herstellungsverfahren: Bohrzirkulargewindefräsen
Basic terms for threads
General designations and instructions
Nominal diameter:
Refers to the diameter of a thread geometry. The quoted nominal diameter of an M16 thread is the value 16 mm.
Core diameter:
This is the smallest diameter of the thread geometry and can be determined by the rule of thumb:
- Core hole for thread tapping and milling: Hole ⌀ = nominal ⌀ – pitch P, example size M16, hole ⌀ = 16.0 mm – 2.0 mm = 14.0 mm
- Core hole for thread forming: Hole ⌀ = nominal ⌀ – factor f × pitch P example size M16, tolerance 6H: f = 0.45, tolerance 6G: f = 0.42 hole ⌀ = 16.0 mm – 0.45 × 2 mm = 15.1 mm
The actual size will of course vary from this, depending on the production and tolerance conditions.Pitch:
For a thread this refers to the axial distance travelled for each completed turn (M16: pitch P = 2). This is then expressed as the distance between 2 successive crests of the thread. For imperial threads the thread pitch is expressed as turns per inch (tpi)..
Effective diameter:
This describes a theoretically and geometrically ideal circular cylinder (effective cylinder). Its diameter lies midway between the core diameter and nominal diameter. This divides the thread profile so that the width of the valleys (voids) equals that of the peaks (teeth). Amongst other things it is necessary for determining the pitch angle of a thread.
Flank angle:
Metric threads have a flank angle of 60° and a pointed crest to the teeth. This large angle generates increased friction and with it high self-locking against a screw fastening coming loose. In comparison to this, other threads such as trapezoidal threads have a small flank angle with low friction.
Thread tolerances for taps, fluteless taps and thread mills
Taps/fluteless taps:
The tolerance width of a tap or fluteless tap is much tighter than the permissible tolerance band of a finished thread. The tolerance is designed so that a correct thread is produced from the beginning. The tool wears in service and eventually reaches the point where the correct thread profile can no longer be produced:The thread is now smaller than the lower tolerance of the “Go” gauge. The tolerance for the thread tap or fluteless tap could then be positioned at the upper part of the internal thread area. Here however there is the risk of producing an oversized thread, which is above the upper limit of the “No Go” gauge. Thread taps or fluteless taps with “X” tolerance which are used on materials that have no problem with oversize are positioned higher in the tolerance band. The result is longer tool life as a result of higher wear tolerance.
Thread mills:
The tolerance of the thread mill has no effect on the tolerance situation of the thread to be produced. The required tolerance is governed by the machine tool and is generated by a circular movement of the tool. Tool wear can be compensated by programming.The Manufacturing Process: Thread tapping
The general-purpose process for internal threads
Thread tapping is the most widely known process for generating internal threads.
High productivity, relatively low costs and universal operational capabilities (on conventional machine tools, transfer systems, machining centres) are the main considerations. Taps are available in HSS / HSS-E / HSS-E-PM / solid carbide to satisfy the particular requirements of the user.
Special considerations when tapping threads
When tapping threads there is a form fit between tool and workpiece. The thread size, thread pitch and tolerance are precisely defined by the tap itself. However this causes specific machining problems not found with drilling or milling:- Axial and radial movements in combination
- The spindle play must be controlled in order to avoid pitch errors
- Feed rate and cutting speed are directly linked
The rotational speed of the machine spindle must be synchronised with the speed of the feed axisThreads in through holes and in blind holes
When selecting a tap, the longest possible lead chamfer form should be selected. A longer lead chamfer places less stress on the tool, thus reducing the load on the cutting edges. This aspect is increasingly significant as the tensile strength of the material increases.
Taps for through holes
With these (straight-fluted) taps with a spiral point, the chips are evacuated downwards in the feed direction and fall out downwards when the tool is withdrawn. Therefore these tools are unsuitable for use in blind holes. When the direction of rotation is inverted (reversed), the compressed chip is not sheared off and becomes jammed.
If these taps are used in blind holes, damage to the thread or breakage of the tool is inevitable. Straight-fluted taps without a spiral point are used for machining brittle materials. Due to the tendency of brittle materials to form discontinuous chips, tools of this design can be used both for tapping through holes and also for tapping blind holes.
Form A 6 - 8 turns lead chamfer, for short through holes.
Form B 4 - 5 turns with spiral point, general purpose for through holes
Form D 4 - 5 turns lead chamfer, for through holes or blind holes
Taps for blind holes
In general the generation of a thread in a blind hole places greater demands on the tool. The chips must be evacuated upwards through the chip flutes. When reversing and shearing off the chips at the root the tap is subjected to high torsional forces.
Form D 4 - 5 turns lead chamfer, for blind holes with long thread runout.
Form C 2 - 3 turns lead chamfer, for universal range of use.
Form E 1.5 - 2 turns lead chamfer, short thread runout for the greatest possible depths of thread.
Advantages and disadvantages of tapping
Advantages:
- Wide field of application in almost all materials
- No special requirements for the machine tool
- If necessary, threads can be re-cut using the same tool
- Manual use is always an option
- They usually offer a cost-effective solution for thread generation
Disadvantages:
- Chip evacuation often causes problems
- Lack of process reliability due to the formation of swarf wrapped around the tool
- Tool breakage generally leads to scrap
Avoidance of defects when using taps
You should be aware of this:
Problem when tapping
Solving the problem
Chipping at the start of the thread- Reduce the cutting speed.
- Check the core hole diameter.
- Check the radial run-out of the spindle and the workpiece clamping.
- Use a tap with a longer lead chamfer.
Excessive tool wear- Increase the oil proportion in the emulsion, use cutting oil.
- Use a longer lead chamfer.
- Switch to a suitable tool coating.
Inadequate chip evaluation- Use a tool with suitable geometry.
Poor surface quality- Exchange of worn tools.
- Select suitable operating parameters for the material to be machined.
- Tool unsuitable for the material.
- Increase the oil proportion in the emulsion, use cutting oil.
Built-up edges- Select a suitable tool coating.
- Increase the cutting speed.
- Improve the cooling.
Tool breakage- Check the pre-drill diameter.
- Check the axial offset between the tool and the pre-drilled core hole.
- Run-out too short when tapping a blind hole.
- Use a tapping chuck with length compensation.
Thread too large- Defective core hole.
- Reduce the feed rate and cutting speed.
- Check the axial offset between the tool and the pre-drilled core hole.
Thread too small- Defective core hole.
- Tap tolerance incorrect.
- Wear mark reached – use a new tool.
Classification into performance categories
Taps are divided into groups by the Hoffmann Group for simple and correct selection of the product.
Our GARANT highlight products for tapping
The Manufacturing Process: Thread forming
The thread forming process generates the threads by cold deformation; chip formation and chip evacuation are no longer required. Thanks to this advantage, the fluteless tap can be used with good process reliability for generating threads in blind holes and through holes, even with critical L×D ratios and thread depths greater than 4×D.
Load phases in the thread forming process
In the thread forming process, the torque load on the tool is up to 30% greater than for the thread tapping process. Since a fluteless tap does not require chip grooves for evacuation of chips, the core diameter of the tool can be designed for greater stability. This means that a fluteless tap can achieve good process reliability even when used for the most demanding processes.The following factors have the greatest influence on the torque development:
- Workpiece material
- Pre-drill diameter
- Thread pitch
- Lubrication
- Coating and geometry
In order to keep the torque forces as low as possible, the optimum tapping diameter and a high-quality lubricating medium should be chosen
Advantages and disadvantages of thread forming
Advantages:
- No chip formation, chip evacuation is not required
- High process reliability
- High thread strength because it is created by cold deformation
- Sturdy tool design, thus low risk of fracture
- Very good surface quality
- The same tool can be used for generating threads in blind holes and through holes
- Extremely long working life
Disadvantages:
- High precision demanded of the pilot hole
- Tool breakage usually leads to scrap
- Not approved in some industries
- Application area limited by elongation at break, tensile strength and thread pitch
- Large sizes of thread require high torque
Error avoidance when using fluteless taps
You should be aware of this
Problem when thread forming
Solving the problem
Thread not fully formed- Reduce the pilot hole diameter. Refer to the appropriate table for the suitable pilot hole diameter.
Thread overworked- Increase the pilot hole diameter. Refer to the appropriate table for the suitable pilot hole diameter.
Thread surface rough, thread flanks torn- Use high-quality lubricant and ensure a sufficient supply of lubricant.
- Use a tool with oil grooves.
- Use coated tools.
Tool breakage- Increase the pilot hole diameter.
- Reduce the cutting speed.
- Change the lubricant and ensure a sufficient supply of lubricant.
- Use coated tools.
- Material is unsuitable for forming. Choose another process.
Core diameter too small- Increase the pilot hole diameter. Refer to the appropriate table for the suitable pilot hole diameter.
Our GARANT Highlight Products for thread forming
The Manufacturing Process: Thread milling
Thread production with short cycle times:
3D CNC control is a pre-requirement for the performance of thread milling. After adjustment to the working depth the tool describes a spiral and radial movement into the workpiece so as to reduce the loading. By rotation of the thread mill and simultaneous movement of the three main axes of the machining centre, the thread is now produced in a 360° movement.
Thread mills offer many potential applications:
- Thread mills can be widely used for general-purpose thread cutting in a very wide range of materials
- High cutting speeds and feed rates make a substantial contribution to saving time in production
- They also avoid the risk of axial overcutting of the thread
- Short milling chips contribute to good process reliability
Advantages and disadvantages of thread milling
Advantages:
- Very versatile and flexible in use
- The same tool can be used for generating threads in blind holes and through holes
- The same tool can be used for generating right-hand and left-hand threads
- Different tolerance levels achievable with a single tool
- Good process reliability thanks to short chips, no swarf wrapped around the tool
- Tool breakage does not result in component scrap
- Low torque, even for large thread dimensions
Disadvantages:
- High cost of tools
- Complex programming and
- demands on the machine tool
- Machining time is often uneconomical for mass production
Machining strategies for thread milling
Optimisation for use of thread mills
Normally with a thread mill the complete thread is generated in a single 360° movement. For special requirements it may be preferable to employ a divided cut. A change to the direction of rotation may also help optimise the results.
Workpiece programming:- For thread milling, machine tools mostly operate to cycles programmed within the controller
- When programming the cutting parameters, check whether the input relates to the contour feed rate v, or the feed rate at the centre of the cutting path V m
- Tip: Perform a trial run on the workpiece and monitor the cycle time
Cutting force distribution (recommended) for critical milling operations:- For thread depths >2×D and large thread pitches (P>1.5 mm), work with a radial cut distribution of 2/3 – 1/3
- For thin-walled materials and unstable machining conditions
- For problems with conical thread forming due to the tool being forced back
- Radial cut distribution significantly reduces the torsional forces and bending moments
Radial distribution of the cut
The thread is first cut about 2/3 of the depth and then is cut to the finished profile in a second pass.
Axial distribution of the cut
Here part of the thread is produced first and then the full depth of the thread is machined.
Choice of the optimum tool movement:
Climb milling
The radial force F acts in the direction of the centre. The chip thickness is small at the point of cutter exit
Opposed milling
The radial force acts in the direction of the workpiece. The chip thickness is greater at the point of cutter exit
Advantages:
- Reduced vibration (chatter marks)
- Improved tool life
- Low cutting pressure, suitable for thin-walled components
Disadvantages:
- On high tensile materials
- Avoidance of conical threads
- Under unstable machining conditions
End cutting thread mill
In the end cutting thread milling process, certain deviations in the machining strategy must be observed, which differ from standard thread milling.Cutting force distribution
With an end cutting thread mill the thread is completed to the full thread depth in a single machining cycle. No cutting force distribution is necessary, since the radial forces that occur remain constant even at different thread depths.Tool set-up
Using the specified programming radius (RPRG value), which is laser etched on the shank, the user can generate threads true to the thread gauge, right from the first thread.The strategy
The end cutting thread mill is designed for left-handed cutting. Thus the machining is carried out as climb milling for right-hand threads, and as opposed milling for left-hand threads. Cooling with compressed air permits very high production quantities per tool in hardened materials up to 63 HRC. The thread protection countersink can be created either before the actual thread milling process or after it.Thread milling process
The end face geometry creates the core diameter of the thread. The end face is designed so that when the middle of the thread tolerance band is achieved, the core hole ⌀ lies within the core hole tolerance. Thus the gauge size of the core hole and also of the thread is achieved. The first cutting edge of the end cutting thread mill serves as the taper lead-in for the thread profile. In the thread milling process, it performs the main machining work of generating the finished thread profile. The second cutting edge performs the finishing work. The machining work of the third cutting edge is very little, it serves to clean the thread rather than performing a pass without cutting.Avoiding problems when using thread mills
Problems with thread milling generally have only minor causes, and these can be rectified without great trouble:
Problem
Solving the problem
Vibration/chattering- Change the operating parameters (cutting speed and feed rate).
- Change over to axial or radial distribution of the cut.
- Check the radial run-out and make sure the clamping is adequate.
- Use tools with smaller overhang.
Tool breakage at start up- Check the feed rate.
- Check the programmed milling radius.
- Check for interference and collision contours on the workpiece or jig.
- Check the tool for wear
High wear on the flank faces- Switch over to climb milling.
- Use tools with suitable coating.
- Reduce the cutting speed.
- Select a higher feed rate per tooth.
- Check the supply of coolant.
Poor surface quality- Exchange of worn tools.
- Select suitable operating parameters for the material to be machined.
- The tool is unsuitable for the material.
Our GARANT Highlight Products for thread milling
The Manufacturing Process: End cutting thread milling
A 3D CNC control system is also precondition for the use of an end cutting thread mill, just as it is for a thread mill. Unlike thread milling, the end cutting thread mill plunges into the material with a helical movement without drilling a core hole. Drilling, thread milling and chamfering can be performed in just a single operation.
End cutting thread milling as problem solver for a very wide range of requirements:
An end cutting thread mill ensures process reliability, especially for final machining tasks on complex components. It is ideally suited to generating a thread on surfaces that are skew or are not flat.Thread entry and exit surfaces that are skew will not cause the end cutting thread mill to run off line. It is also suitable for unstable clamping conditions. This tool offers excellent process reliability even for difficult to machine materials up to 63 HRC.
Direct purchaseAdd an article directly to the cart: Please state article number or article code here.Products found:
-
Article no. {{ combinedCodeWithHighlight }}Article code:EAN / GTIN:Manufacturer number:
No products were found for your search term
Please check your entry or adjust the article number / article code
This article cannot be ordered.Services cannot be ordered without the right article. Please add the service to the desired article.Further configurations on the product detail page are necessary for this article.Please check this specification or adjust the article number / article code.Please select a specific variant.An error found the way into our system.This article is not available anymore.Multiple items can be added via our Order form.Sign in to your Account