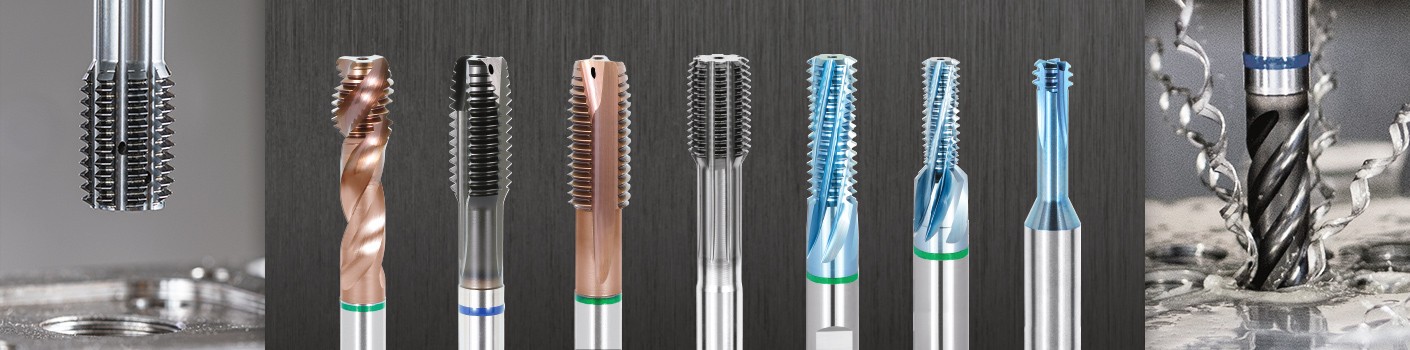
Un taraudage en toute sécurité - Réalisation de filetages intérieurs
Découvrez toutes les informations utiles sur les différents procédés de fabrication de filetages intérieurs
En technique de fabrication, la réalisation de filetages intérieurs compte parmi les tâches d’usinage les plus exigeantes.
Le filetage intervient souvent à la fin d’un processus de fabrication et est donc décisif pour la qualité de la pièce. Des filets défectueux impliquent généralement d’importants coûts supplémentaires. La sécurité de processus a dès lors une priorité absolue, mais il convient également de veiller à des cadences courtes et des cycles de production économiques.
Vous trouverez ci-dessous un aperçu des procédés de filetage :
1. Procédé : taraudage
2. Procédé : taraudage par déformation
3. Procédé : fraisage de filets
4. Procédé : fraisage-alésage par interpolation
Introduction : notions de base sur le filetage
Désignations générales et remarques :
Diamètre nominal :
Désigne le diamètre d’une géométrie de filetage. Pour le filetage M16, le chiffre correspond à un diamètre nominal de 16 mm.
Diamètre d’âme :
Diamètre minimum de la géométrie de filetage, qui peut être calculé selon la formule de base suivante :
- Perçage d’avant-trou lors du taraudage et du fraisage de filets : ⌀ alésage = ⌀ nominal – pas P, exemple de dimension M16, ⌀ alésage = 16,0 mm – 2,0 mm = 14,0 mm
- Perçage d’avant-trou lors du taraudage par déformation : ⌀ alésage = ⌀ nominal – facteur f × pas P. Exemple de dimension M16, tolérance 6H : f = 0,45, tolérance 6G : f = 0,42, ⌀ alésage = 16,0 mm – 0,45 × 2 mm = 15,1 mm
Il en résulte des différences naturelles par rapport à la cote réelle en termes de fabrication et de tolérance.Pas :
Pour les filetages, désigne la distance axiale parcourue lors d’un tour (M16 : pas P = 2). Ce terme exprime ainsi la distance entre 2 pointes de filet successives. Pour les filetages en pouces, le pas de filetage est indiqué par le nombre de filets sur une distance d’un pouce (threats per inch/pas par pouce).
Diamètre sur flancs :
Décrit un cylindre circulaire (cylindre de flanc) théorique et géométriquement idéal. Son diamètre se situe au centre entre le diamètred’âme et le diamètre nominal. Le profil de filet est coupé de manière à ce que les largeurs des creux de profil (espaces vides) et des pointes (dents) soient identiques. Il est notamment nécessaire pour déterminer l’angle d’hélice d’un filetage.
Angle de flanc :
Les filetages métriques ont un angle de flanc de 60° et une forme pointue des dents. Ce grand angle exerce un frottement plus élevé et donc un autoblocage plus important contre le desserrage d’un vissage. En comparaison, par ex. les filetages trapézoïdaux ont un petit angle de flanc avec un frottement faible.
Tolérances de filetage pour les tarauds standard et à refouler ainsi que les fraises à fileter
Taraud standard/à refouler :
La largeur de tolérance d’un taraud standard ou d’un taraud à refouler est nettement plus étroite que la plage de tolérance admissible d’un filetage terminé. La tolérance est conçue de manière à pouvoir réaliser un filetage correct dès le début. Pendant l’utilisation, l’outil s’use et atteint le point auquel il n’est plus possible de réaliser un filetage correct :Le filetage devient plus petit que la tolérance inférieure du calibre ENTRE. Il serait alors possible d’appliquer la tolérance de taraud standard/à refouler à la zone de filetage intérieur supérieure. Mais il existe toutefois un risque de réaliser un filetage trop grand, qui serait supérieur à la valeur limite du calibre N’ENTRE PAS. Les tarauds standard ou à refouler avec une tolérance "X", qui sont utilisés dans les matériaux dépourvus de problèmes de surcote, sont positionnés plus haut dans la plage de tolérances. La durée de vie s’en trouve ainsi prolongée en raison d’une tolérance d’usure supérieure.
Fraise à fileter :
La tolérance de la fraise à fileter n’a aucune influence sur la position de tolérance du filetage à réaliser. La tolérance nécessaire est commandée par la machine et produite par un mouvement circulaire de l’outil. La programmation permet de compenser une usure de l’outil.1. Procédé : taraudage
Le procédé universel pour les filetages intérieurs.
Le taraudage est le procédé le plus connu pour la réalisation de filetages intérieurs.
Productivité élevée, coûts comparativement bas et possibilités d’utilisation universelles (sur machines-outils classiques, installations de transfert, centres d’usinage) sont des atouts majeurs. Les tarauds en HSS/HSS-E/HSS-E-PM/carbure monobloc répondent à toutes les exigences de l’utilisateur.
Particularités du taraudage
Pendant le taraudage, une liaison mécanique est établie entre l’outil et la pièce. La taille de filetage, le pas de filetage et la tolérance sont définis avec précision à l’aide du taraud. Par rapport au perçage ou au fraisage, cela donne toutefois lieu à des problèmes spécifiques lors de l’usinage :- Combinaison de mouvements axiaux et radiaux
- Contrôle du jeu de broche nécessaire pour éviter les erreurs de pas
- L’avance et la vitesse de coupe sont directement liées
La vitesse de rotation de la broche de la machine doit être synchronisée avec la vitesse de l’axe d’avance.Filetage de trous borgnes et débouchants
Lors du choix du taraud, il convient de sélectionner une entrée la plus longue possible. Une entrée longue sollicite moins l’outil et la charge sur les arêtes de coupe est réduite. Cet aspect gagne en importance en cas de résistance croissante du matériau.
Tarauds pour trous débouchants
Pour ces tarauds (à goujures droites) avec entrée GUN, le copeau est évacué vers le bas dans le sens de l’avance et se détache lors de la sortie de l’outil. C‘est pourquoi ces outils ne conviennent pas pour l‘usinage de trous borgnes. En cas d’inversion du sens de rotation, le copeau refoulé n’est pas cisaillé et est coincé.
L‘utilisation de ces tarauds pour l‘usinage de trous borgnes entraînerait inévitablement un endommagement du filetage ou un bris de l‘outil. Lors de l’usinage de matériaux cassants, des tarauds à goujures droites sans entrée GUN sont utilisés. En raison de la tendance des matériaux cassants à former des copeaux en poussières, il est possible d’utiliser les outils de ce type à la fois pour l’usinage de trous débouchants et de trous borgnes.
Type A Entrée sur 6-8 filets, pour trous débouchants courts.
Type B 4-5 filets avec entrée GUN, utilisation universelle pour les trous débouchants
Type D Entrée sur 4-5 filets, pour trous débouchants ou borgnes
Tarauds pour trous borgnes
En général, la réalisation d’un filetage borgne est plus exigeante pour l’outil. Les copeaux doivent être amenés vers le haut via la goujure. Lors de l’inversion et du cisaillement de la racine du copeau, des forces de torsion importantes s’exercent sur le taraud.
Type D Entrée sur 4-5 filets, pour trous borgnes avec fin du filetage longue.
Type C Entrée sur 2-3 filets, pour utilisation universelle.
Type E Entrée sur 1,5-2 filets, fin du filetage courte pour des taraudages en limite de fond de trou.
Avantages et inconvénients du taraudage
Avantages :
- Domaine d’utilisation large dans la quasi-totalité des matériaux
- Pas d’exigences particulières pour la machine
- Le cas échéant, les filetages peuvent être réusinés avec le même outil
- Utilisation manuelle possible
- Solution généralement économique pour le taraudage
Inconvénients :
- L’évacuation des copeaux pose souvent problème
- Incertitude de processus en raison de la formation de rubans de copeaux
- Le bris d’outil entraîne généralement des rebuts
Prévention des erreurs lors de l’utilisation de tarauds
Vous trouverez ci-dessous des solutions pour résoudre les éventuelles difficultés rencontrées :
Problème du taraudage
Résolution du problème
Bris au niveau du pas du filetage- Réduire la vitesse de coupe.
- Vérifier le diamètre d’avant-trou.
- Vérifier la concentricité de la broche et le serrage de la pièce.
- Utiliser un taraud avec une entrée plus longue.
Usure trop importante de l’outil- Augmenter la proportion d’huile dans l’émulsion, utiliser de l’huile de coupe.
- Utiliser une entrée plus longue.
- Opter pour un revêtement d’outil approprié.
Evacuation insuffisante des copeaux- Utiliser un outil avec une géométrie adaptée.
Mauvaise qualité d’état de surface- Remplacer les outils usés.
- Sélectionner les paramètres d’utilisation adaptés au matériau à usiner.
- L’outil ne convient pas au matériau.
- Augmenter la proportion d’huile dans l’émulsion, utiliser de l’huile de coupe.
Arêtes rapportées- Choisir un revêtement d’outil approprié.
- Augmenter la vitesse de coupe.
- Améliorer l’arrosage.
Bris de l’outil- Vérifier le diamètre de pré-perçage.
- Vérifier le déport d’axe entre l’outil et le pré-perçage.
- Sortie trop courte lors de l’usinage de trous borgnes.
- Utiliser un mandrin de taraudage à compensation de longueur.
Filetage trop grand- Avant-trou défectueux.
- Réduction de la vitesse d’avance et de coupe.
- Vérifier le déport d’axe entre l’outil et le pré-perçage.
Filetage trop petit- Avant-trou défectueux.
- Tolérance de taraud incorrecte.
- Marque d’usure atteinte – Utiliser un nouvel outil.
Classification en catégories de performances
Pour une sélection aisée et correcte des produits, nos tarauds sont répartis en groupes :
Nos produits phares GARANT pour le taraudage :
2. Procédé : taraudage par déformation
Lors du taraudage par déformation, les filets sont produits par formage à froid ; la formation et l’évacuation des copeaux sont supprimés. Grâce à cet avantage, le taraud à refouler peut être utilisé en toute sécurité pour le filetage de trous borgnes et débouchants, même en cas de rapports L×D critiques d’une profondeur de filetage supérieure à 4×D.
Phases de charge lors du taraudage par déformation
Lors du taraudage par déformation, la charge du couple sur l’outil est jusqu’à 30 % plus élevée par rapport au taraudage. Etant donné qu’un taraud à refouler ne nécessite pas de goujures pour l’évacuation des copeaux, le diamètre d’âme peut être conçu pour être plus stable sur l’outil. Un taraud à refouler peut ainsi être utilisé en toute sécurité, même avec les exigences les plus strictes.Les facteurs suivants ont une influence majeure sur le développement du couple :
- Matériau de la pièce
- Diamètre de pré-perçage
- Pas de filetage
- Lubrification
- Revêtement et géométrie
Pour minimiser les forces de couple, il est nécessaire de choisir le diamètre d’avant-trou optimal et un lubrifiant de haute qualité
Avantages et inconvénients du taraudage par déformation
Avantages :
- Aucune formation de copeaux, évacuation des copeaux supprimée
- Sécurité de processus élevée
- Résistance élevée au filetage grâce à la déformation à froid
- Conception robuste de l’outil, ce qui réduit le risque de rupture
- Excellente qualité d’état de surface
- Un seul outil pour les trous borgnes et débouchants
- Durées de vie très élevées possibles
Inconvénients :
- Exigence élevée au niveau du pré-perçage
- Le bris d’outil entraîne généralement des rebuts
- Pas autorisé dans de nombreux secteurs
- Domaine d’utilisation limité par la ductilité, la résistance à la traction et le pas du filetage
- Couple élevé et dimensions de filetage élevées
Prévention des erreurs lors de l’utilisation de tarauds à refouler
Vous trouverez ci-dessous des solutions pour résoudre les éventuels problèmes rencontrés :
Problème du taraudage par déformation
Résolution du problème
Filetage non entièrement formé- Réduire le diamètre de pré-perçage. Prendre note du diamètre de pré-perçage approprié dans le tableau correspondant.
Filetage surdimensionné- Augmenter le diamètre de pré-perçage. Prendre note du diamètre de pré-perçage approprié dans le tableau correspondant.
Surface filetée sale, flancs de filet arrachés- Utiliser des lubrifiants de haute qualité et assurer un apport de lubrifiant suffisant.
- Utiliser un outil avec des rainures d’huile.
- Utiliser des outils revêtus.
Bris de l’outil- Augmenter le diamètre de pré-perçage.
- Réduire la vitesse de coupe.
- Modifier la lubrification et assurer un apport de lubrifiant suffisant.
- Utiliser des outils revêtus.
- Le matériau ne convient pas pour le formage par déformation. Choisir un autre procédé.
Diamètre d’âme trop étroit- Augmenter le diamètre de pré-perçage. Prendre note du diamètre de pré-perçage approprié dans le tableau correspondant.
Nos produits phares GARANT pour le taraudage par déformation :
3. Procédé : fraisage de filets
Taraudage avec des temps machines courts :
L’utilisation d’une fraise à fileter nécessite une commande CNC 3D.
Après l’approche à la profondeur de travail, l’outil pénètre radialement dans la pièce dans un mouvement hélicoïdal afin de réduire la charge. La rotation de la fraise à fileter et le mouvement simultané des trois axes principaux du centre d’usinage permettent alors de réaliser le filetage en un mouvement de 360°.Les fraises à fileter offrent de nombreuses possibilités d’utilisation :
- Les fraises à fileter peuvent être largement utilisées de manière universelle dans les matériaux les plus divers.
- Des vitesses de coupe et des avances élevées contribuent considérablement à un gain de temps dans la production.
- Il n’existe pas non plus de risque de repassage axial du filetage.
- Les copeaux de fraisage courts sont en outre avantageux pour la sécurité de processus.
Avantages et inconvénients du fraisage de filets
Avantages :
- Utilisation universelle et très flexible
- Un seul outil pour les trous borgnes et débouchants
- Un seul outil pour les filetages à droite et à gauche
- Possibilité de différentes positions de tolérance avec un seul outil
- Sécurité de processus grâce aux copeaux courts, pas de rubans de copeaux
- Le bris d’outil n’entraîne pas de rebuts de pièces
- Couple réduit, même avec de grandes dimensions de filetage
Inconvénients :
- Coûts d’outillage élevés
- Programmation complexe et
- exigences élevées vis-à-vis de la machine
- Délai d’usinage souvent peu rentable lors de la production de masse
Stratégies d’usinage lors du fraisage de filets
Optimisation en cas d’utilisation de fraises à fileter
Une fraise à fileter permet généralement de réaliser le filetage complet en un mouvement de 360°. Pour des exigences particulières, une répartition de l’effort de coupe peut s’avérer judicieuse. Une modification du sens de fonctionnement peut également optimiser les résultats.
Programmation de la pièce :- Lors du fraisage de filets, les machines-outils utilisent généralement leurs propres cycles de commande
- Lors de la programmation des paramètres de coupe, veiller à ce que l’avance de contournage v ou l’avance continue centrale V m soit prédéfinie
- Conseil : démarrer l’essai au-dessus de la pièce et respecter le temps de cycle
Répartition de l’effort de coupe (recommandations) pour les opérations de fraisage critiques :- Pour les profondeurs de filetage > 2×D et les grands pas de filetage (P > 1,5 mm), travailler avec une répartition de coupe radiale de 2/3 – 1/3
- Pour matériaux de faible épaisseur et conditions instables
- En cas de problèmes avec le taraudage conique en raison du déport d’outil
- La répartition de coupe radiale permet de réduire nettement les forces de torsion et le moment de flexion
Répartition de coupe radiale
Le filetage est d’abord formé à env. 2/3, puis terminé lors d’une deuxième étape.
Répartition de coupe axiale
Dans ce cas, une partie seulement du filetage est réalisée, puis la profondeur de filetage totale est usinée.
Choix du mouvement d’outil idéal :
Fraisage en avalant
La force radiale F s’exerce en direction du centre. Faible épaisseur de copeau à la sortie de l‘arête de coupe
Fraisage en opposition
La force radiale F s’exerce en direction de la pièce. Epaisseur de copeau plus élevée à la sortie de l‘arête de coupe
Avantages :
- Les vibrations sont réduites (marques de vibrations)
- Durées de vie de l’outil prolongées
- Pour les pièces de faible épaisseur grâce à la pression de coupe réduite
Inconvénients :
- Coûts d’outillage élevés
- Programmation complexe et
- exigences élevées vis-à-vis de la machine
- Délai d’usinage souvent peu rentable lors de la production de masse
Fraise à fileter circulaire :
Lors du processus de fraisage-alésage par interpolation, il convient de tenir compte de certaines divergences dans la stratégie d’usinage, qui diffèrent du fraisage de filets standard.Répartition de l’effort de coupe :
Une fraise à fileter circulaire permet de réaliser un filetage calibré à la profondeur de filetage requise en un seul cycle d’usinage. Une répartition de l’effort de coupe n’est pas nécessaire, car les forces radiales générées restent constantes, même à des profondeurs de filetage différentes.Mise en place de l’outil :
A l’aide du rayon de programmation indiqué (valeur RPRG), gravé au laser sur la queue, l’utilisateur peut immédiatement réaliser un alésage fileté calibré lors du premier filetage.Stratégie :
La fraise à fileter circulaire est de type coupe à gauche. C’est pourquoi l’usinage s’effectue en avalant pour les filetages à droite et en opposition pour les filetages à gauche. Le refroidissement à l’air comprimé permet d’atteindre des volumes maximum dans les matériaux trempés jusqu’à 63 HRC. Le chanfreinage de protection peut être réalisé avant le processus de fraisage de filets proprement dit ou ultérieurement.Fraisage de filets :
La coupe au centre produit le diamètre d’âme du filetage. L’arête frontale est conçue de manière à ce que le ⌀ d’avant-trou se situe dans la tolérance d’avant-trou une fois le milieu de la tolérance de filetage atteint. Ainsi, l’exactitude du calibrage de l’avant-trou et du filetage est atteinte. La première arête de la fraise à fileter circulaire sert d’ébaucheur du profil de filet. Au cours du processus de fraisage de filets, elle effectue le travail d’usinage principal du profil de filet terminé. La deuxième arête assure le travail de finition. Le travail d’usinage de la troisième arête est très faible et sert plutôt au nettoyage du filetage que de coupe à vide.Prévention des problèmes lors de l’utilisation de fraises à fileter
Les problèmes de fraisage de filets n’ont généralement que de petites causes, qui peuvent être corrigées très facilement :
Problème
Résolution du problème
Vibrations/Broutage- Modifier les paramètres d’utilisation (vitesse de coupe et avance).
- Opter pour la répartition de coupe axiale ou radiale.
- Vérifier la concentricité et veiller à un serrage suffisant.
- Utiliser des outils avec un porte-à-faux réduit.
Rupture de l’outil au démarrage- Vérifier l’avance.
- Vérifier le rayon de fraisage programmé.
- Vérifier les arêtes gênantes et les contours de collision de la pièce ou du dispositif.
- Vérifier l’usure de l’outil
Usure élevée au niveau des faces de dépouille- Passer au fraisage en avalant.
- Utiliser des outils dotés d’un revêtement approprié.
- Réduire la vitesse de coupe.
- Sélectionner une avance par dent supérieure.
- Vérifier l’alimentation en lubrifiant.
Mauvaise qualité d’état de surface- Remplacer les outils usés.
- Sélectionner les paramètres d’utilisation adaptés au matériau à usiner.
- L’outil n’est pas adapté au matériau.
Nos produits phares GARANT pour le fraisage de filets et le fraisage-alésage par interpolation :
4. Procédé : fraisage-alésage par interpolation
L’utilisation d’une fraise à fileter circulaire nécessite, comme pour une fraise à fileter classique, une commande CNC 3D. Contrairement au fraisage de filets, la fraise à fileter circulaire pénètre dans le matériau avec un mouvement hélicoïdal sans perçage d’avant-trou. Le perçage, le fraisage de filets et le chanfreinage sont possibles en une seule opération.
Fraises à fileter circulaires pour répondre aux exigences les plus diverses :
Une fraise à fileter circulaire est synonyme de sécurité de processus, notamment pour les tâches d’usinage finales sur des pièces complexes. Elle est idéale pour le filetage sur des surfaces inclinées ou non planes.
Tout glissement de la fraise à fileter circulaire en raison des entrées et sorties de filets obliques est exclu. Elle convient également pour des conditions de serrage instables. Cet outil offre une excellente sécurité de processus même pour les matériaux difficilement usinables jusqu’à 63 HRC.
Commande directeAjouter directement un article au panier: Veuillez indiquer une référence article ou un code article ici.Produits trouvés:
-
Réf. {{ combinedCodeWithHighlight }}Référence:EAN / GTIN:Réf. fabricant:
Aucun article ne correspond à votre recherche :
Veuillez vérifier votre saisie ou adapter le code article / la référence client.
Cet article ne peut pas être commandé.Les prestations de service ne peuvent pas être commandées sans l’article correspondant. Veuillez ajouter la prestation de service à l’article désiré.Pour cet article, d’autres configurations sont nécessaires sur la page de détail des produits.Veuillez vérifier ces informations ou adaptez le code article / la référence client.Veuillez sélectionner une variante concrète.Une erreur est survenue.L’article n’est plus disponible.Une saisie multiple est possible via notre formulaire de saisie rapide.Sign in to your Account