The day-to-day hazard of dust and dirt in the workshop
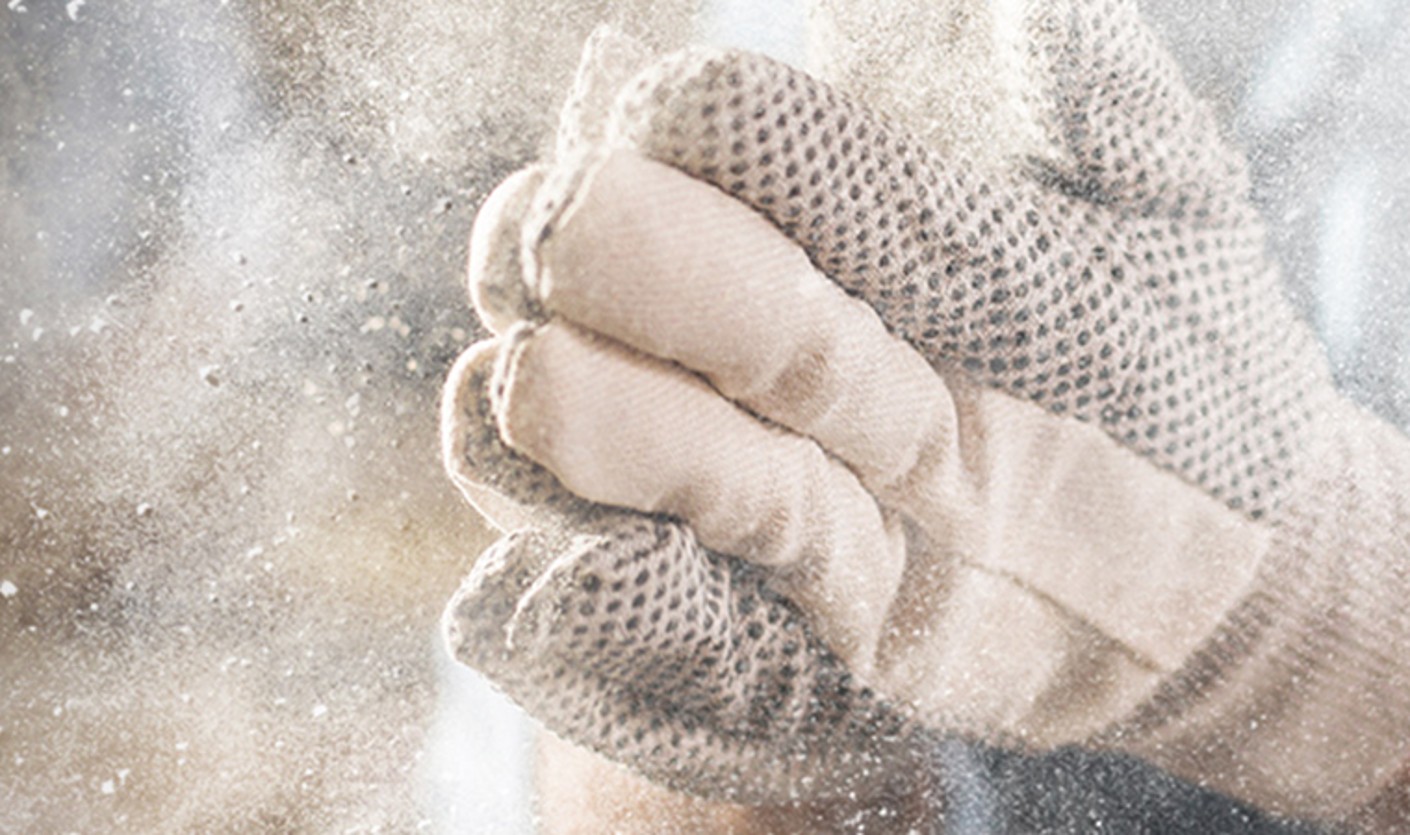
Dust and dirt are one of the clearest signs of how hard you’ve been working in your workshop. Coarse swarf from machining blanks into parts, the polishing dust used for the final finish...
But from your experience with metal, you know that these by-products of your efforts also constitute a health risk – swarf can leave nasty tears in your skin, and dust in the air can make it harder to breathe. As the craftman in charge of your workshop, you are responsible for yourself and your employees. This is a challenging task that requires an extensive knowledge of occupational safety issues.
On the following pages, we will tell you about the all-important legal aspects relating to occupational safety when performing grinding and cutting tasks. We will also introduce you to the STOP principle and explain each of the measures involved in detail. Once you’ve finished reading, you will know all the most important facts you need on the current legal framework for occupational safety and risk assessment. Read on now, and you’ll be up to date in no time!
The Occupational Safety Act – Compulsory guidelines for every workshop

Take one look at the wide range of potential hazards and risk factors involved in grinding and cutting work, and it quickly becomes clear just how complex the legislative texts required for this field are. The mechanical procedures carried out during grinding and cutting, such as the rotation of the grinding point, are potentially just as dangerous as thermal factors, such as hot component surfaces. Dust is also extremely hazardous to both you and your colleagues. Particles of various sizes can harm your health by damaging your airways and lungs, and can also trigger explosions in your working environment. Even the grinding process itself can be harmful to you and other machine operators. For instance, if a workstation is designed poorly from an ergonomic perspective, this can lead to damaging hand/arm vibrations. It is also important to remember the potential dangers caused by electricity if the person wielding the grinder accidentally severs the power feed. Due to these dangers, cutting and grinding processes are subject to a wide range of laws, requirements and regulations, which must be observed both universally and on a case-by-case basis.
As varied as your work: the risk assessment
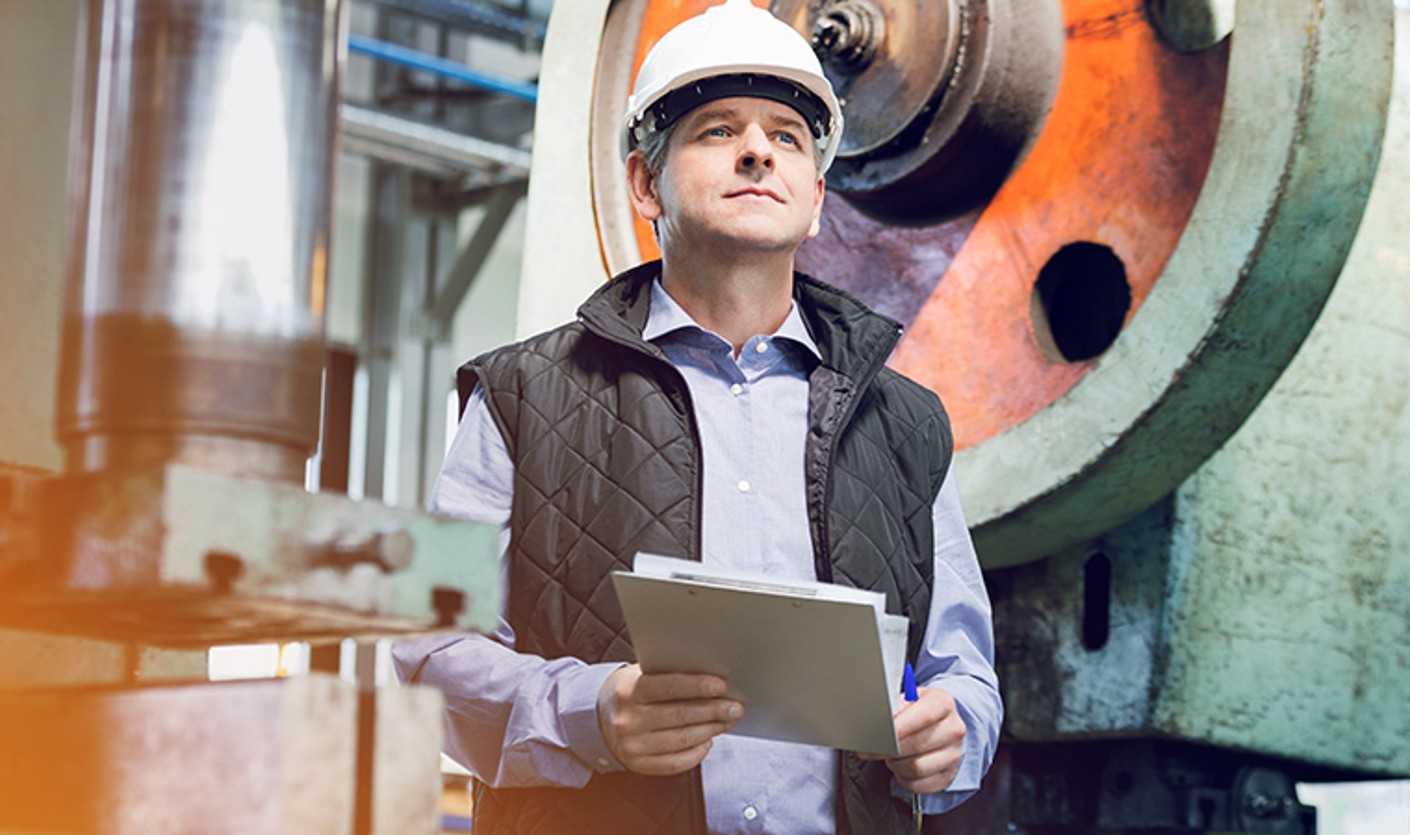
Alongside noise and hand/arm vibrations, dirt and dust are probably the most common hazards found in workshops. Yet despite this, there is no single, universal risk assessment procedure for grinding and cutting. As a craftman, you understand that both materials and tools are incredibly varied, and each one – or combination thereof – brings with it individual risks that need to be suppressed, prevented or protected against.
Occupational safety measures are classified hierarchically – from most effective (risk completely eliminated) to least effective.
While it is impossible to completely eliminate the hazard posed by a rotating disc during cutting or grinding, a workstation inspection can help to make the process safer. In addition to this, as the craftman in charge of your workshop you can check whether your employees are handing the grinder correctly and implementing the material machining process safely and professionally. The most important factor is the use of personal protective equipment.
Observe the following tips to optimise occupational safety in your workshop:
1. Evaluate the risks involved in grinding and cutting work at your work place.
2. Assess the potential danger caused by each risk.
3. Define concrete occupational safety measures.
4. Carry out regular checks to ensure that your occupational safety measures are adhered to.
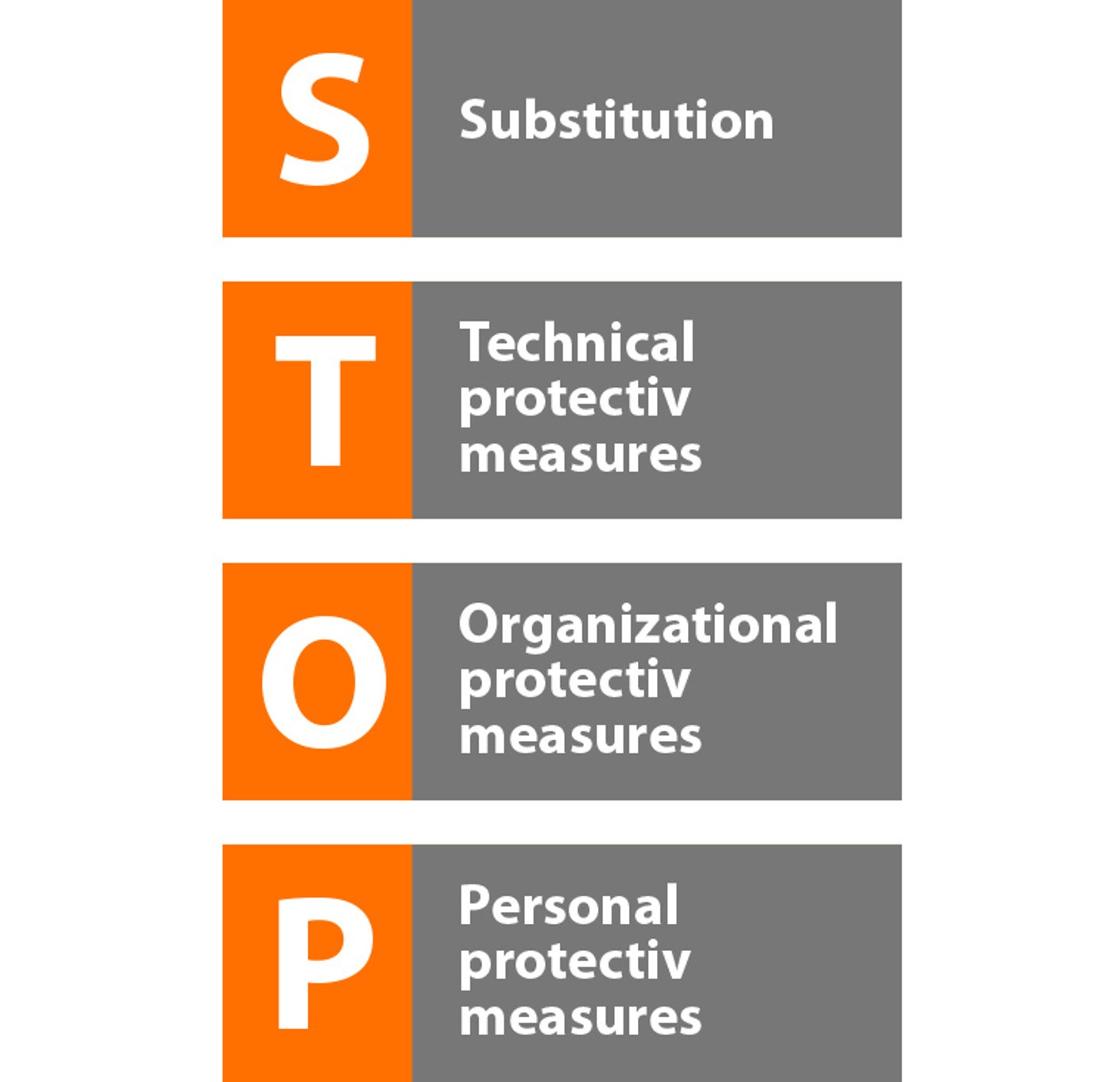
STOP – The name says it all
The “STOP principle” stands for the order of priority that you and your company are also required to follow when it comes to defining and implementing safety measures.
STOP stands for:
S - Substitution
T - Technical safety measures
O - Organisational safety measures
P - Personal safety measures
As the craftman in charge of the workshop, this means you need to implement each measure as follows:
- Design your work processes in such a way that there are no risks involved. Check that the equipment you are using is fully functional and is not a source of potential hazards (i.e. make sure all your discs are intact).
- Eliminate any risks, or take measures to reduce them or install protective equipment (e.g. covers on angle grinders, sound protection).
- Take a look at the strains your colleagues are subjected to during cutting and grinding work. Can you make their work processes shorter or more efficient? Can the process be adjusted to reduce their exposure to these strains? Could you use different technology to reduce the strain?
- Check your employees’ personal protective equipment, making sure that all the relevant items are both in place and fully functional. Are there any cracks in their goggles? Are their mouth and nose masks still fully functional? Are their gloves intact? Does their hearing protection fit, and does it provide sufficient protection?
By applying the STOP principles, you can reduce risks at your work place and play an important role in improving the health, safety and well-being of your employees.