Personal protective equipment
Occupational health and safety at the workplace
Personal protective equipment (PPE) serves to protect the health of employees from potential hazards at the workplace and to maintain performance capabilities. It is used when there is a risk of injuries and impairment to health at the workplace, which cannot be prevented by any other technical or organisational measures. Collective technical measures include risk prevention. An organisational measure will either isolate the risk / keep the employee away from the risk or limit the exposure time to a minimum.
Comprehensive protection from head to toe
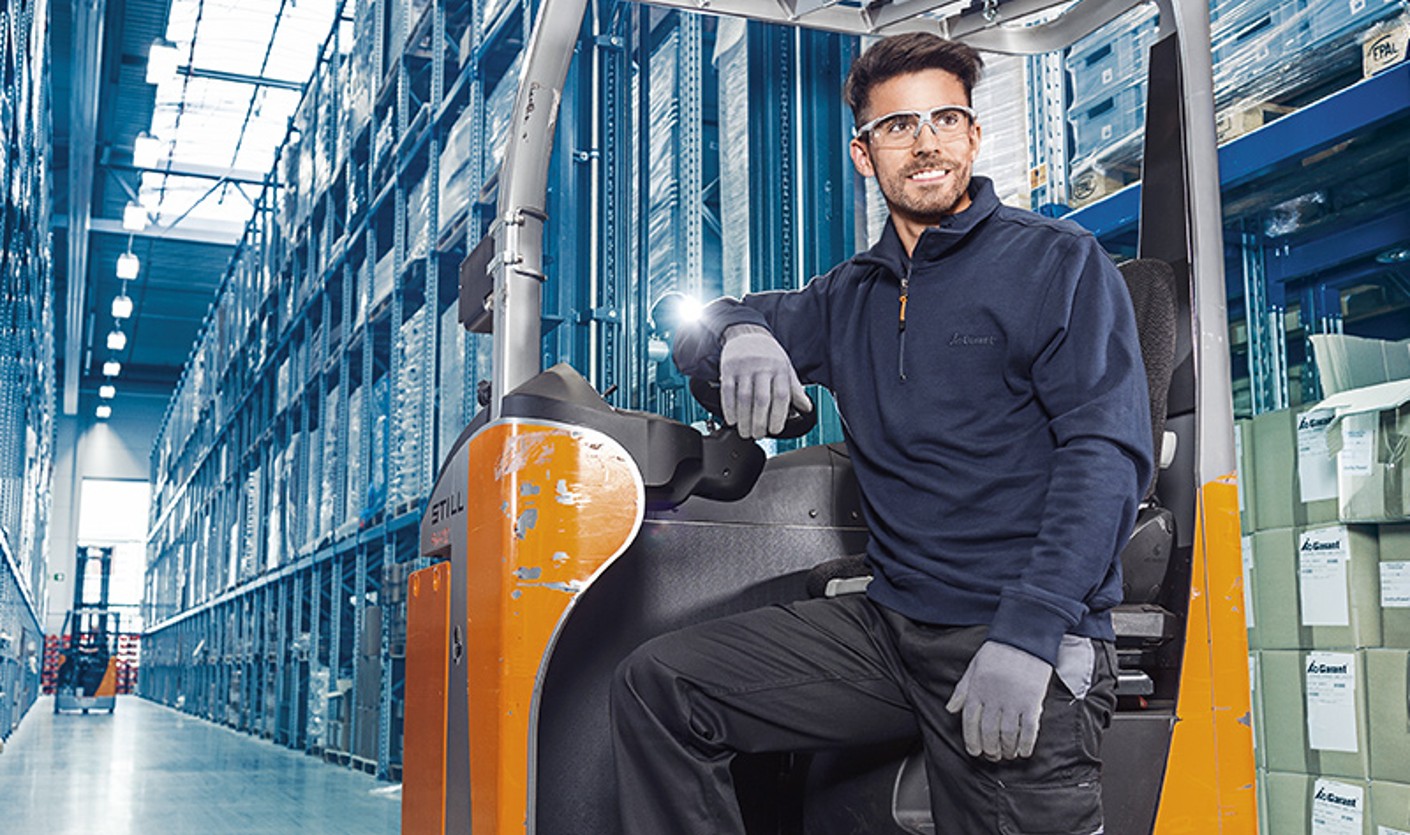
Depending on the working environment the individual elements of personal protective equipment can protect all areas of the body from head to toe - ranging from head and face protection to protective workwear and gloves right down to foot protection. Respirators for example provide protection from poisonous gases. Special protective gloves enable safe working with sharp-edged materials or with chemicals, and safety shoes provide optimum protection from falling objects or sharp objects on the floor.
Find out more about the various types of personal protective equipment:
Duties of the employer
The employer has a duty by law to ensure and protect employee health and safety. He has a duty to identify risks at the workplace and to take the appropriate protective measures.
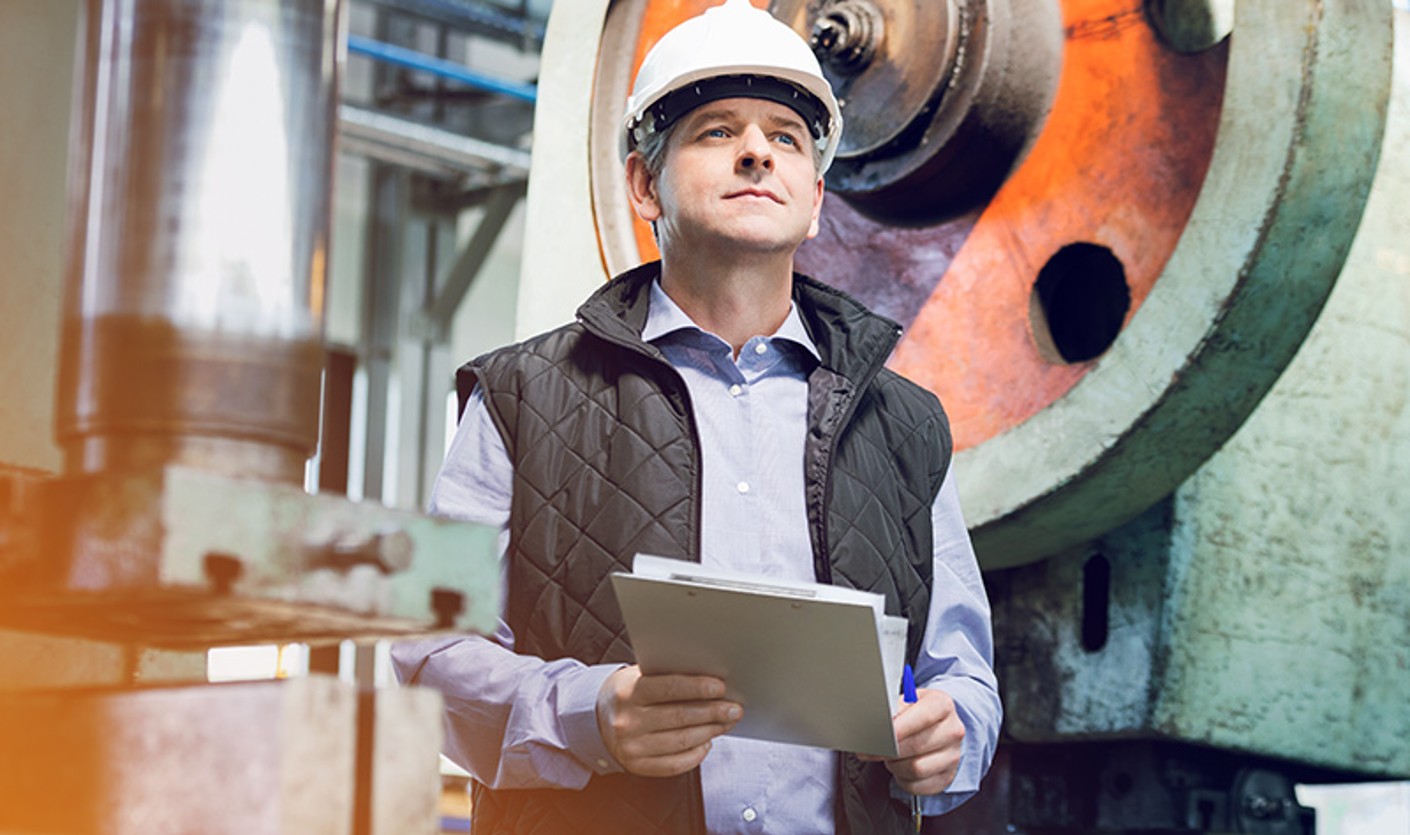
Risk assessment
Before suitable personal protective equipment for employees can be selected, it is necessary to carry out a so-called risk assessment. For this, the respective workplace is analysed:
- Which type of danger are the employees exposed to?
- What are the prevailing operational and environmental conditions?
- Does the employees‘ state of health allow them to use the PPE?
Collective and individual protective measures
After the risk assessment has been carried out, the employer initially has a duty to take technical and organisational measures to keep the risk of injuries or impairments to health to a minimum. If additional protective measures are required, then personal protective equipment will be used. The employer has a legal duty to make available to his employees free of charge those items of personal protective equipment (PPE) that are necessary for their safety.
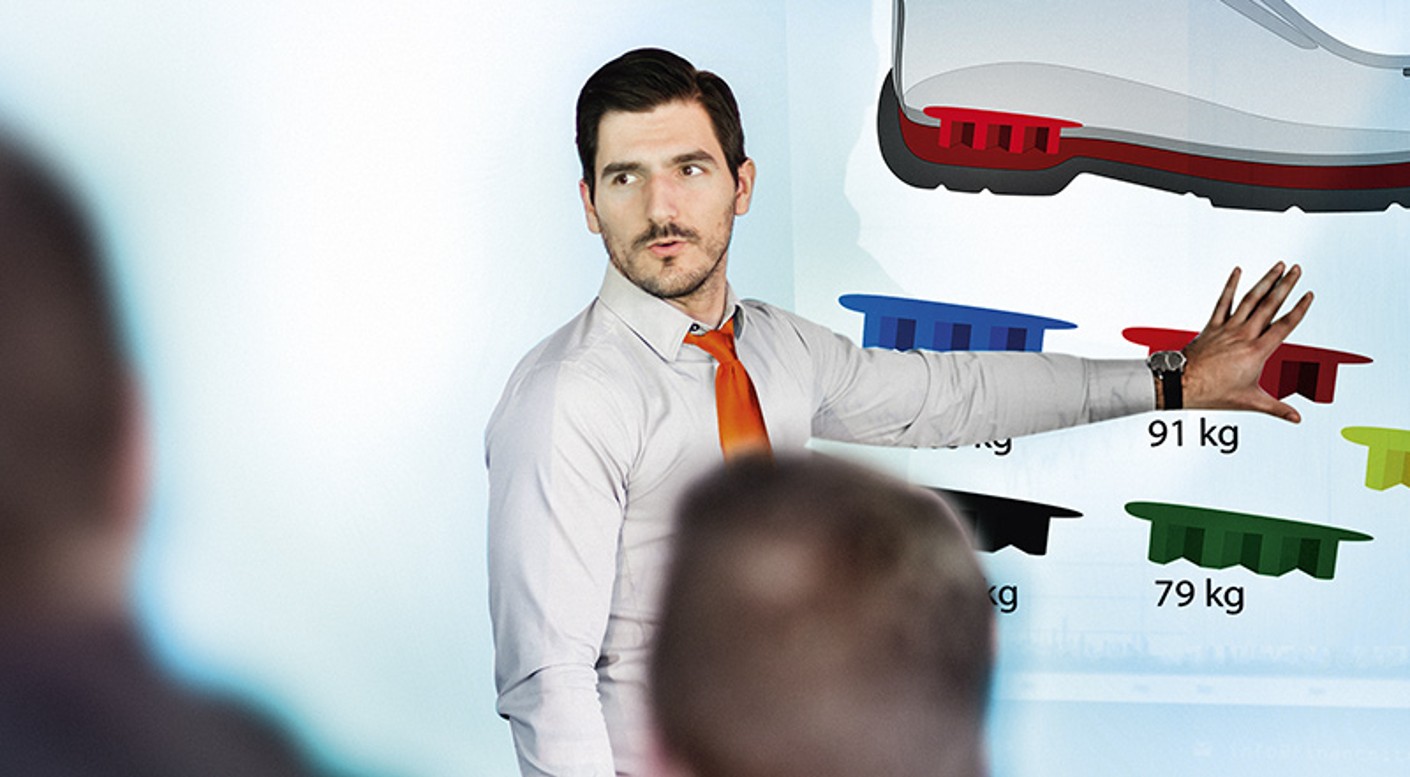
In addition, the employer also has a duty to train employees in the correct use of PPE. Areas within the company or outside (for example on building sites) where PPE is necessary, have to be marked accordingly. The employer has a duty to keep the personal protective equipment clean, to maintain it, repair it and, if necessary, replace it, ensuring that it is in first-class condition at all times. Moreover, the company’s safety officer has to be involved in the whole process.
Our qualified team of PPE specialists will gladly help you to select the correct personal protective equipment for your company, from risk analysis and product wearing tests through to staff training.
Do you have any questions? Our team of experts will be happy to help:
PPE risk categories
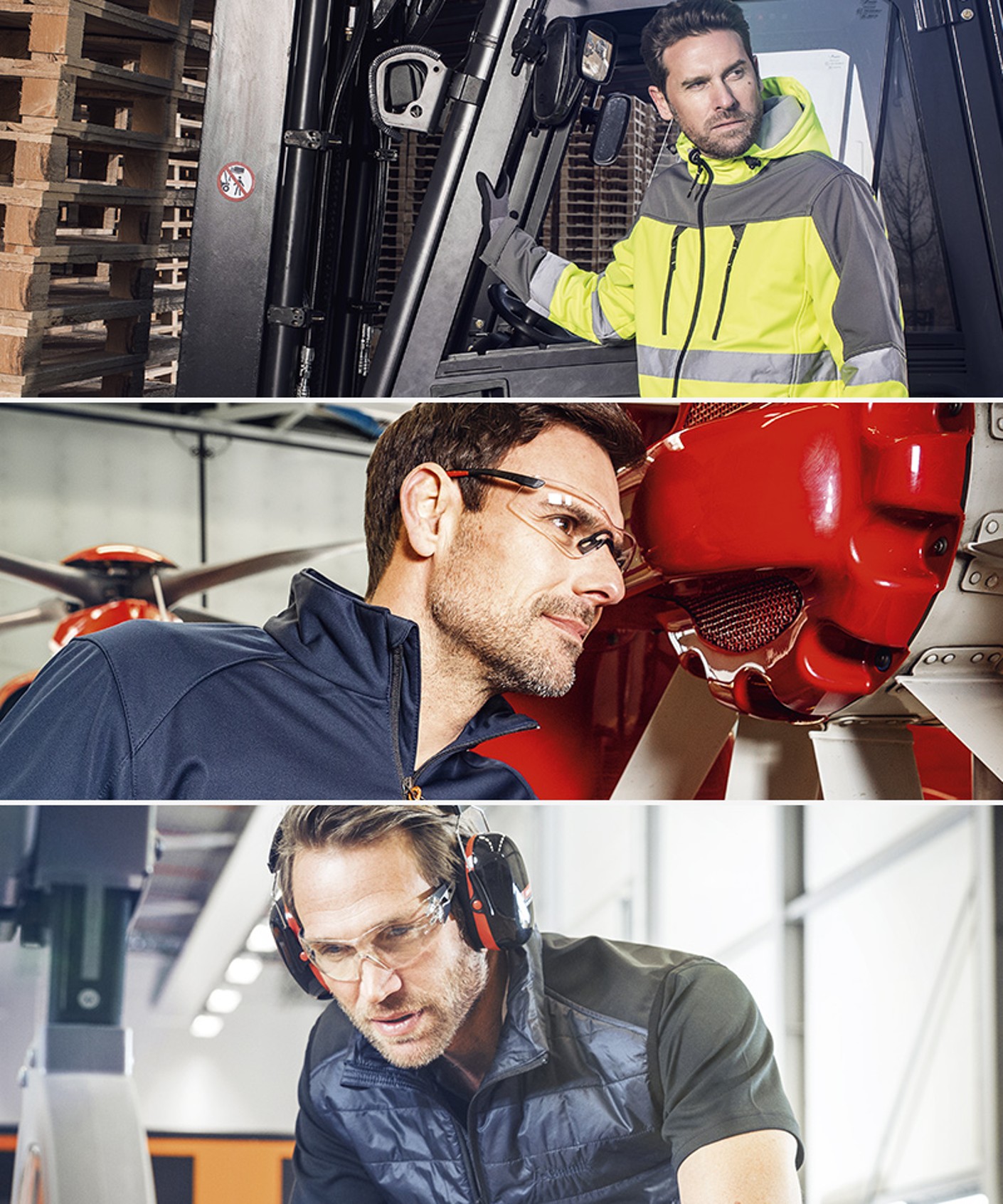
Personal protective equipment is divided into three risk categories depending on its protective function and on the required test procedures.
Category I
- Effectiveness: simple PPE for protection against minimal risk
- Test procedure: without external testing, with CE mark
- Example: gloves for gardening work, sunglasses, winter caps
Category II
- Effectiveness: PPE for protection against medium risk
- Test procedure: CE mark, tested by a certified laboratory and issued with type approval by a notified office licensed to issue certificates
- Example: safety helmets, welder’s protective gloves, safety glasses with side arms
Category III
- Effectiveness: complex PPE for protection against fatal injuries or irreversible damage to health
- Test procedure: CE mark, laboratory testing, type approval, internal yearly review of production procedures and identity code of the notified office next to the CE mark
- Example: harnesses for preventing falls, flameproof clothing, breathing protection
Hoffmann Group: The specialist for personal protective equipment

To maintain and protect the health and performance capabilities of people at the workplace is a major undertaking. Our PPE range of the best quality brands for protection from head to toe and a committed team of specialist advisers will support you to perfection in solving this challenge.
The Hoffmann Group provides you with everything from a single source. We use our 100 years of experience in providing customer service and as a tooling specialist to make your business one of the safest places in the world. Our qualified team of more than 60 PPE specialists has the required specialist knowledge about the protective functions and the legal regulations and standards. They understand the PPE market and offer you perfect support in purchasing and in improving occupational health and safety in your company. We offer professional support from risk analysis through product selection and wearing test to staff training.
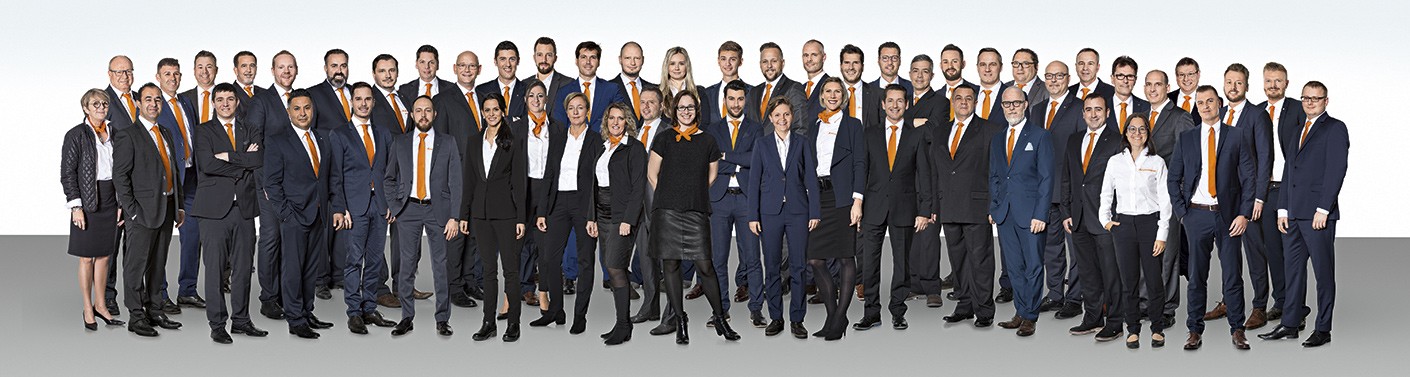
Your advantages:
- Comprehensive selection of personal protective equipment from head to toe
- Manufacturer-neutral, competent and individual advice on site
- High-performance logistics for reliable supply
An overview of the most important universal standards
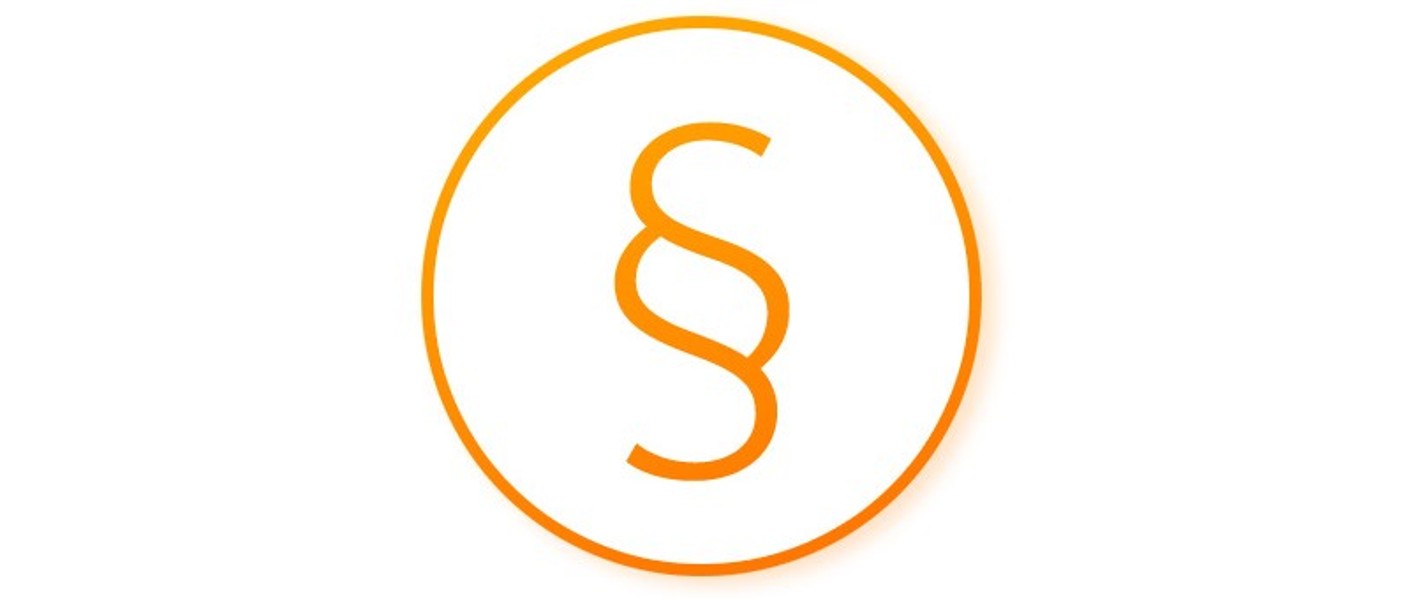
The new PPE Regulation 2016/425 came into force on the 21st April 2018, replacing the PPE Directive 89/391 EWG. As of that date PPE is only certified to the new Regulation. For users of personal protective equipment, the changes are only minor. Manufacturers must, however, in future undergo more rigorous and more regular quality assurance measures to ensure not only quality checks but also sustained quality assurance. In addition, the new CE mark together with the protective effectiveness must be shown on all products and also on their packaging.
In addition, the labour protection law defines the duties of the employer and the employees in order to improve safety at the workplace and to ensure protection of employee health. In addition to these universal standards there are specific national and European standards that apply to every category of personal protective equipment.
You can find these on the following pages:
Frequently asked questions on personal protective equipment
1. What does „personal use“ mean?
Companies should always provide their employees with personal protective equipment. This is mainly for hygienic, but also for ergonomic reasons. PPE should be tailored to each individual employee, for example in the case of shoes, protective workwear or respirators. Some items can be used by more than one person, for instance life vests or high visibility vests. However, after these items have been used they must be cleaned and disinfected according to the manufacturer’s instructions and to the DGUV rules 112-139 to 112-201. Chemical protection overalls on the other hand are disposable items.
2. Who will bear the cost of personal protective equipment?
The employer will bear the cost, as the provision of personal protective equipment is required by law.
3. Do employers have to train their employees in how to use PPE?
Yes. Companies are obliged to train their employees in the correct use of PPE before they use it for the first time. This teaches employees how to put on / take off personal protective equipment correctly, how to use it in the course of their professional activities and how to react correctly in dangerous situations. Employees should also know which potential defects to look out for when checking their protective equipment before use. How often instruction should be given, if at all, depends on the category of the respective PPE.
Do you have any questions? Would you like to receive advice on PPE?
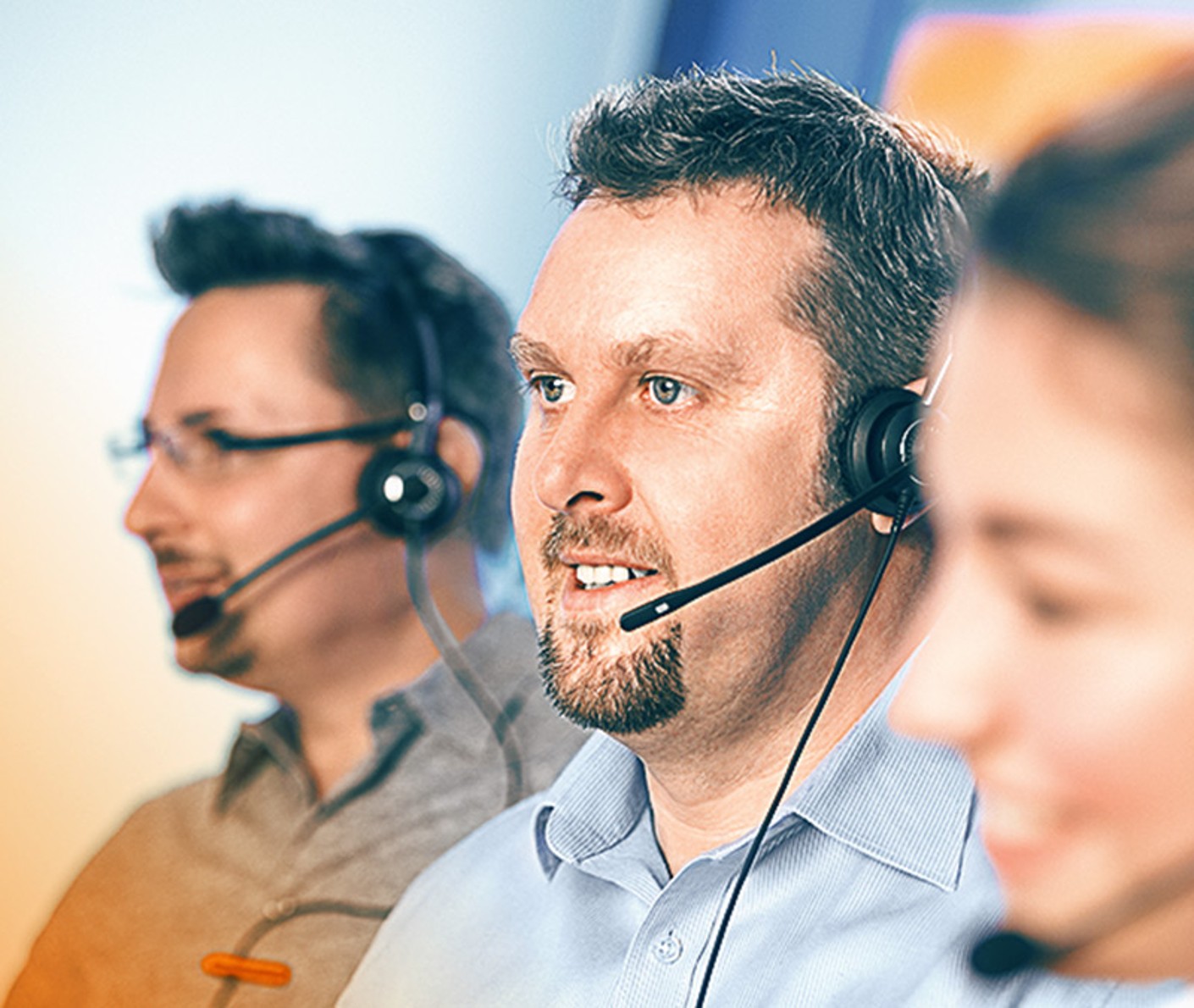
The Hoffmann Group provides you with everything from a single source:
- We provide individual advice, tailored to your needs
- Risk analysis, help with product selection, wearing tests, training sessions and special service offers (glove plans, skin protection plans)