Arbeiten mit Druck nicht unter Druck - Energiesparpotenziale bei der Druckluft
So sparen Sie Kosten durch einen effizienten Druckluft-Einsatz
Hätten Sie geschätzt, dass deutsche Industrieunternehmen jährlich rund 16 Terawatt-Stunden Strom aufwenden, um Druckluft zu erzeugen? Die Zahl, ermittelt von der Deutschen Energieagentur dena, ist beachtlich und trotzdem nicht verwunderlich. Immerhin ist Druckluft für 90 Prozent der Industrie-Prozesse unverzichtbar. Abblasen, trocknen, kühlen, absaugen, reinigen, abdichten, ionisieren, transportieren - Druckluft ist eines der wichtigsten Betriebsmittel. Aber eben auch ein großer Energiekostenfaktor. Darum lohnt es sich, den Druckluft-Verbrauch genauer unter die Lupe zu nehmen, wo hier Energiesparpotenziale liegen.
Der höchste Druckluft-Verlust entsteht auf dem Weg zur Anwendung
Wussten Sie, dass durch nicht oder schlecht optimierten Druckluft-Einsatz bis zu 50 % der erzeugten Druckluft ungenutzt verschwendet werden? Obwohl Druckverluste ein bekanntes Thema sind, gehen laut einer Studie der Europäische Kommission nur 9 % der Befragten den Ursachen für den überflüssigen Verbrauch von Druckluft auf den Grund. 75 % gaben bei dieser Umfrage fehlendes Know-how an. Das möchten wir ändern. Denn die Gründe für unnötigen Druckluft-Verlust sind relativ einfach zu finden.
In diesem Beitrag wollen wir uns auf die Optimierung der Druckluftkomponenten konzentrieren, mögliche Hinweise für Leckagen ansprechen und Sie bei der Wahl des passenden Werkzeugs beraten. Denn: Die unnötigen Kosten entstehen nicht bei der Beschaffung der Luft, sondern auf dem Weg zur Anwendung.
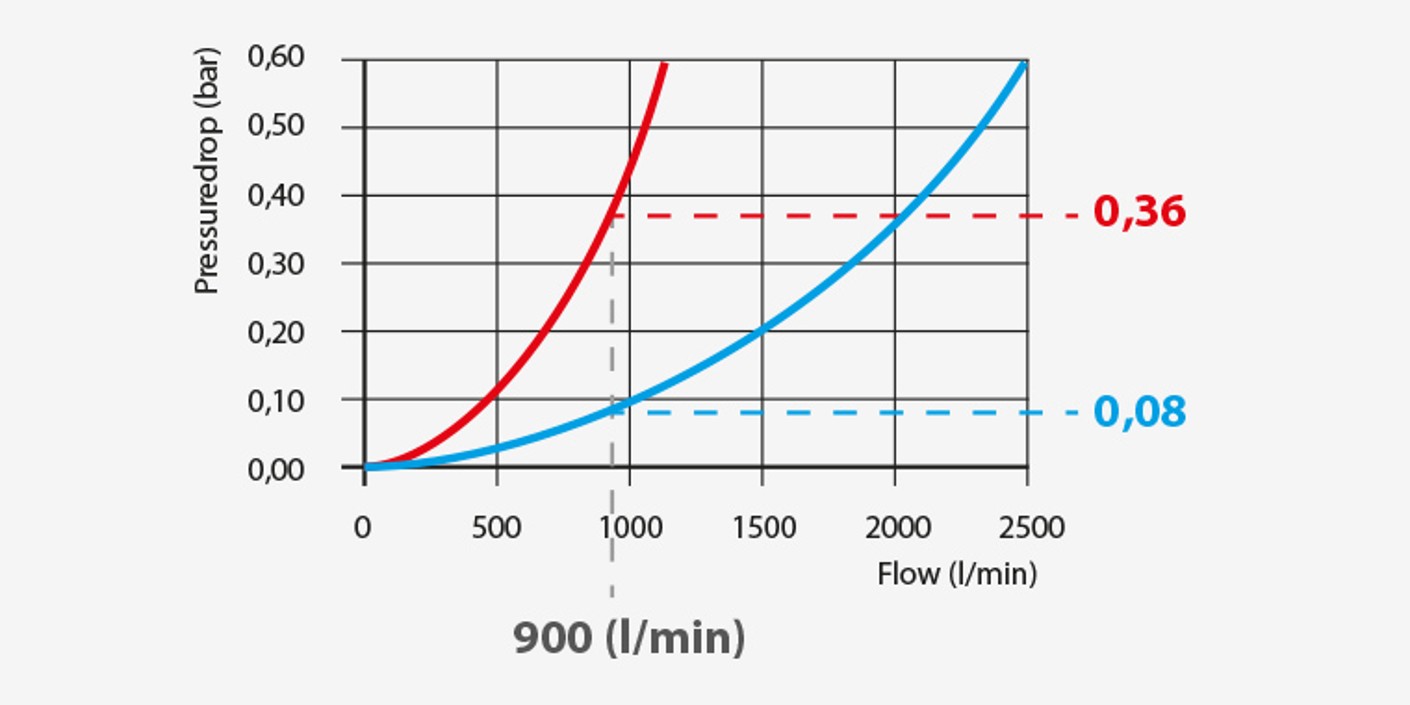
Bei abfallendem Druck sinkt die Effizienz beträchtlich
Druckluft-Werkzeuge sind für einen bestimmten Arbeitsdruck ausgelegt, üblicherweise sind das 6,3 bar. Man geht dabei vom Fließdruck aus, der sich einstellt, wenn die Ventile geöffnet sind. Er ist immer etwas niedriger als der statische Betriebsdruck, der sich am Manometer von einem geschlossenen Ventil ablesen lässt. Bei niedrigerem Druck sinkt die Kompressorleistung beträchtlich. Oft erscheint es daher naheliegend, am Kompressor anzusetzen. Stattdessen sollten zuerst die Druckluft-Komponenten, vor allem die Anschlussstellen überprüft werden.
Wie hoch ist Ihr Druckluft-Verbrauch?
Besteht auch bei Ihnen Anlass, Ihren Druckluft-Verbrauch zu überdenken? Bei acht von neun Unternehmen zumindest ist dies der Fall. Nehmen Sie sich die Zeit, eine Bestandsaufnahme zu machen. Es lohnt sich gerade jetzt, denn die Energiekrise macht unnötige Druckluftverschwendung noch schmerzlicher. Die folgende Tabelle gibt ein Beispiel, wie sich die steigenden Energiepreise zusätzlich auf die Kosten auswirken können.
Um Ihren tatsächlichen Druckluftkosten berechnen zu lassen, empfehlen wir eine Fachberatung bei entsprechenden Fachspezialisten oder Fachfirmen. Wir beraten Sie im Anschluss gerne bezüglich der entsprechenden Druckluftkomponenten oder Werkzeuge.
Hohe Folgekosten vermeiden
Nicht nur der unnötige Druckluft-Verlust fällt stark ins Gewicht. Falsch dimensionierte oder zu lange laufende Kompressoren verursachen ebenfalls sehr hohe Kosten.
Wenn Sie bemerken, dass sich die Stückarbeitszeiten bei einer Druckluft-Anwendung verlängern, besteht Handlungsbedarf. Denn sonst erhöhen sich die Kosten für alle mit der Druckerzeugung verbundenen Stufen. Das kann bis zu mehreren Zehn- bis Hunderttausend Euro im Jahr ausmachen. Dazu steigen auch die Instandhaltungs- und Neuanschaffungskosten infolge der stärkeren Beanspruchung von Werkzeug und Kompressor.

Einsparpotenzial am Beispiel der Bohrmaschine
Am Beispiel der Bohrmaschine soll der Einfluss eines zu geringen Fließdrucks an der Abnahmestelle auf die Gesamtkosten veranschaulicht werden. Bei einem Druckluft-Abfall von nur 0,5 bar zeigt sich, dass sich die reine Bohrzeit bereits um 60 % erhöht! Daraus ergeben sich Mehrkosten von über 240,- Euro im Monat. Dieses Beispiel ist leider keine Ausnahme in den meisten Betrieben.