Structural steels – a real multitalent, and more
When you’re managing industrial production or overseeing craftsmen at work, you’ll see them everywhere: structural steels. Among metals, they’re the ultimate allrounders!
Read on to find out how you can get the best results when working with structural steels and maintain safety at the same time. Learn what specific properties are key in which industry and what you need to look out for when machining structural steels. These useful tips will certainly make one thing easier for you – your daily work.
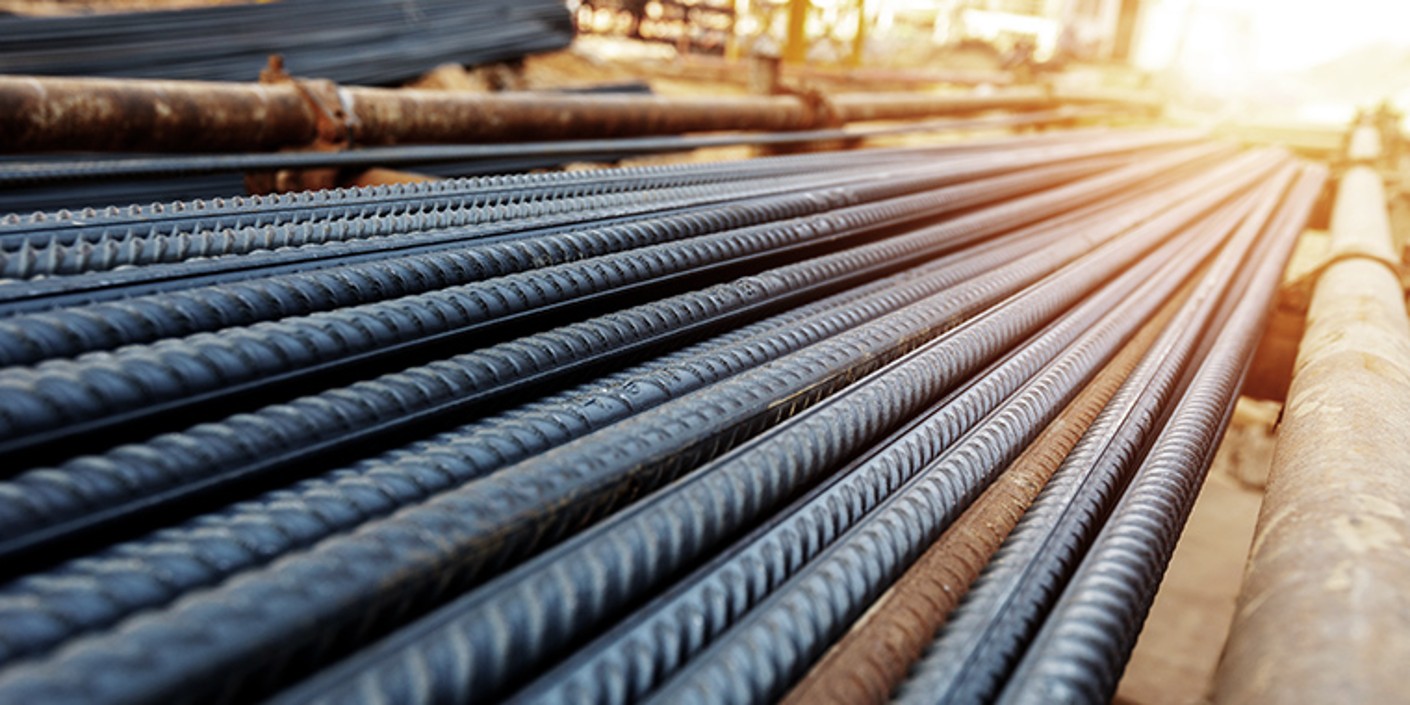
Telling steel from steel
Once treated and machined appropriately, structural steel is suitable for almost any purpose. From your experience with metal, you know that mechanical engineering or the automotive trade rarely choose a material based on a single requirement alone. The desired steel instead needs to match a complex profile of requirements.
As a consequence, steels are often distinguished according to their practical application. While tool steels are a major asset for the manufacture of hand and machine tools, mechanical engineering, vehicle design or steelwork all favour structural steel.
You’re likely as familiar with sorting the different structural steels according to their properties and potential fields of application as you are with their chemical composition or primary grades. Just like yourself, designers and purchasers usually look to the material designations based on the DIN EN 10027-1 and DIN V 17006-100 standards.

Every sector has their own structural steel
Structural steels are used in almost every industry. They vary in their initial form. Rolled or forged, extruded or die cast – there are a myriad methods, producing classic sheet steel, strip steel or long steel bars, tubes or beams. The steel's original form is intended to match what it will be used for, and where. Structural steel for use as a frame and bed for tool machines will look quite different from sheet steel used in lightweight design. Tool machine production or general mechanical engineering, tool design or mould construction – structural steels frequently need to withstand extreme mechanical and thermal loads.
The automotive industry and transport sector are where structural steel really gets to show off its full diversity. Here, role and location of a component defines the required grade of structural steel. After all, a motorcycle, a van and a railway vehicle differ somewhat in design and structure. Roller bearings, valve springs, camshafts or electrical steel sheets of varying design require different structural steels. While automotive components’ roles don’t differ so much from corresponding roles in aerospace technology, aircraft design and shipyard operations, the dimensions and requirements profiles do so all the more. In short, you’re not getting anywhere without structural steel.
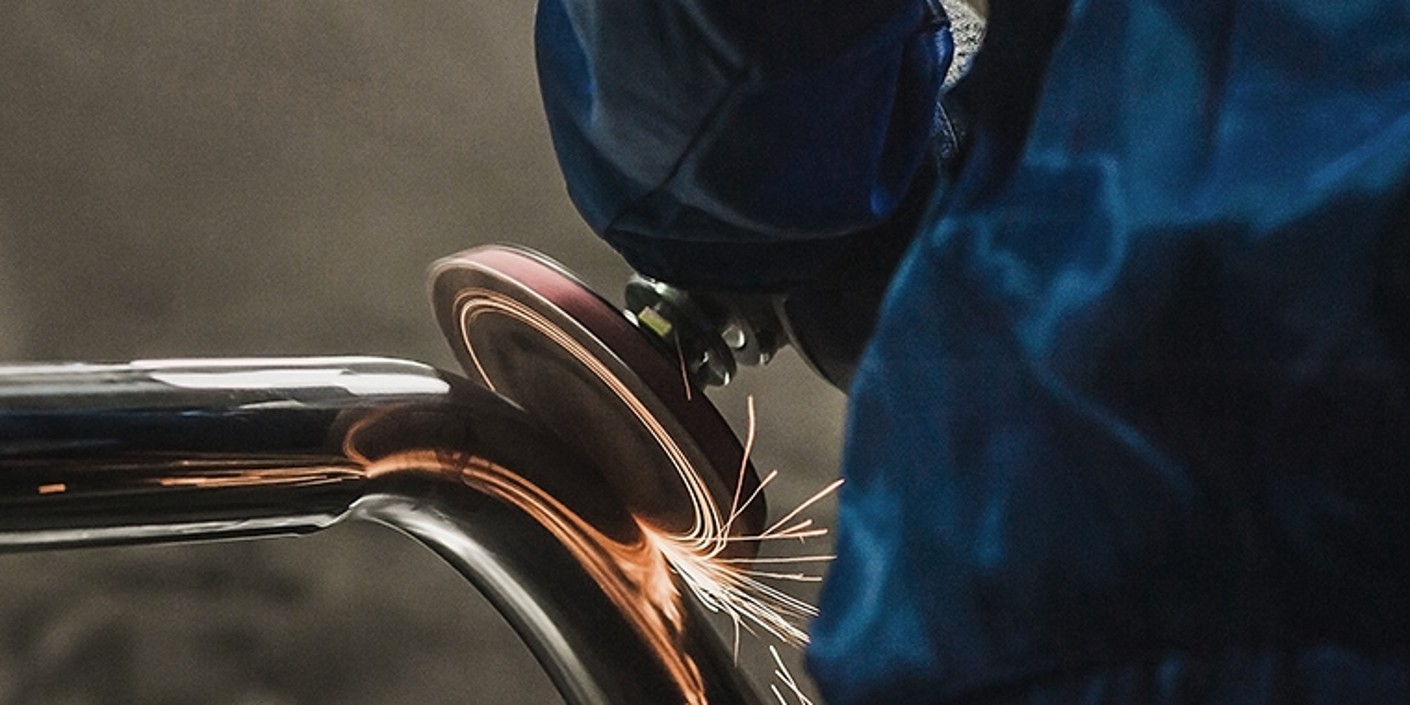
Beware of hazards, they’re everywhere: cutting and grinding structural steels
How to machine structural steel depends on its size, surface quality, geometric and positional accuracy, the desired number of units and, of course, on the desired result. Besides joining, cutting and grinding are key production methods used across a variety of industries.
The metalcutting production methods cutting and grinding take many forms and are primarily useful for structural steel with coarser structures and surfaces. Whether you're working on a single component or multiple welded parts, the aim of grinding is always to make dimensions and shape accurate. Consequently, grinding also improves surface quality and looks. Finish machining – as the name implies – adds the finishing touches by getting rid of the last minimal irregularities, the burrs.
Each of these steps, performed using angle grinders, orbital sanders or CNC machines for example, has inherent risks:
- Both cutting and grinding involve tremendous force. So you need to take precautions to keep yourself and your workforce safe from ejected workpiece chippings and grinding particles. Also always remember that splinters breaking off the grinding wheel also pose a significant danger.
- This is why we recommend checking the expiry date on grinding wheels before using them. Grinding wheels are produced using artificial resin. When the resin ages, the grinding wheel becomes brittle and may break.
- Manual utensil or permanently installed disc, sparks, disc fragments or swarf – faulty equipment or missing safety hoods increase danger and force you to rework mistakes. If your manual utensils don't feature safety guards sufficiently sized for flexible use, you and your workforce will need faceshields to protect against these dangers.
- Like your face, your hands are also exposed to danger. Never touch spinning grinding points, not when they’re running at full speed nor when they’re powering down – you can come away with massive cutting injuries.
- Breathing protection
- Bear in mind, too, that fixed installations without guard hoods can catch and trap limbs, clothing or hair in moving machine parts.
Less obvious hazards
- Secure the surroundings and remove anything that might catch fire from spraying sparks or glowing embers, causing a fire or even explosions.
- And remember that, depending on the material, the grinding dust produced may be flammable itself. Make sure that dust is siphoned off with a fluid or install suitable dust extractors.
- With respect to health and the considerable harm that dust, for example nickel dust, can do, dust extractors and fully functional personal protective equipment are indispensable.
- Another key aspect in terms of health and safety is noise protection. Cutting and grinding typically produce a lot of loud, unpleasant noise. Make sure that you and your workforce are always wearing the necessary hearing protection.
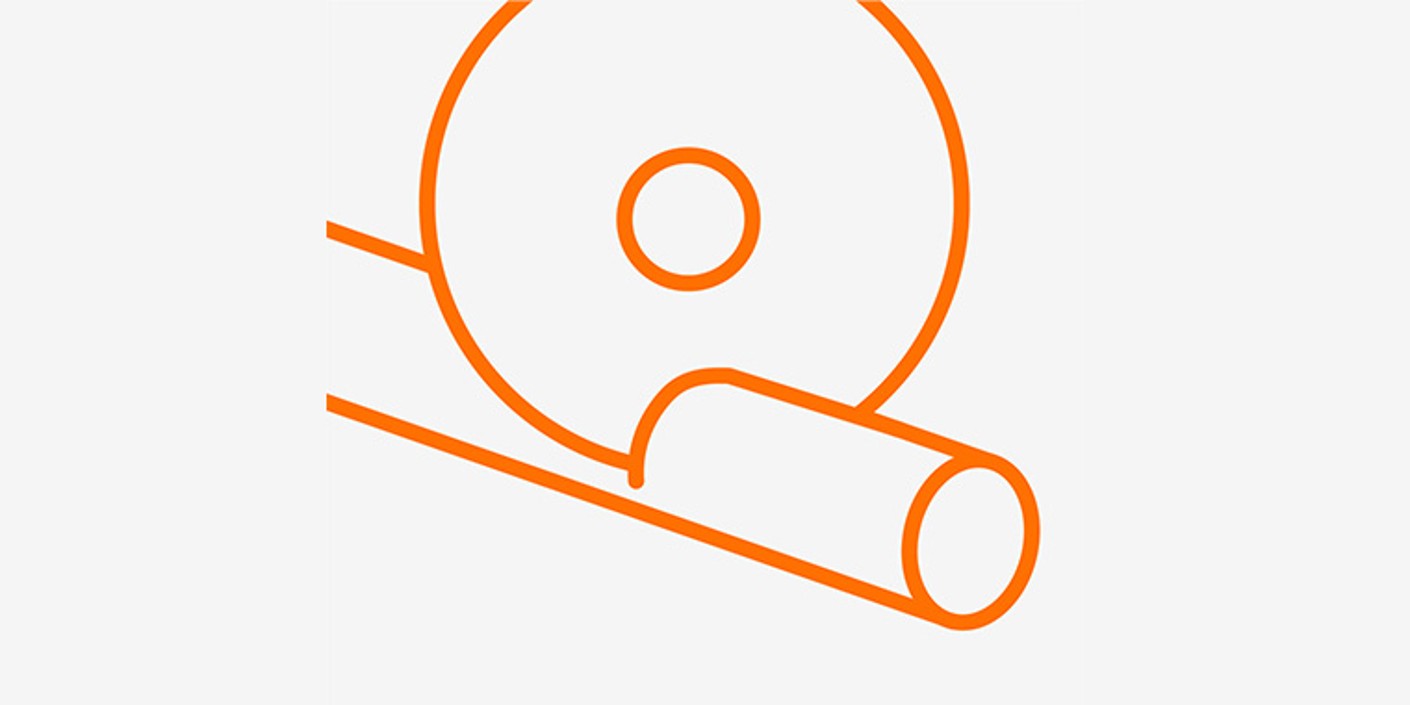
Cutting structural steel takes skill
It’s among the most common sights in any workshop or building site – beams, flat steel bars or pipes need cutting to size. But cutting structural steels takes knowing what you're doing, regardless of whether you're cutting it by hand or using a machine. The forces involved in the material and how difficult it is to do should not be taken lightly.
If you’ve decided to use an angle grinder, choose the matching cutting disc carefully and check that it's firmly fastened before beginning. Pay close attention to the cutting process – a wedging angle grinder can be fatal.
Before getting to work, remember to check your surroundings for dust and other flammable substances. If necessary, ready the immediate vicinity for the work you’ll be performing. Always wear flame-retardant clothing and your personal protective equipment. A point of note: if this kind of work comes up regularly, getting a custom set of adjustment mechanism and tool can really help you work more efficiently.
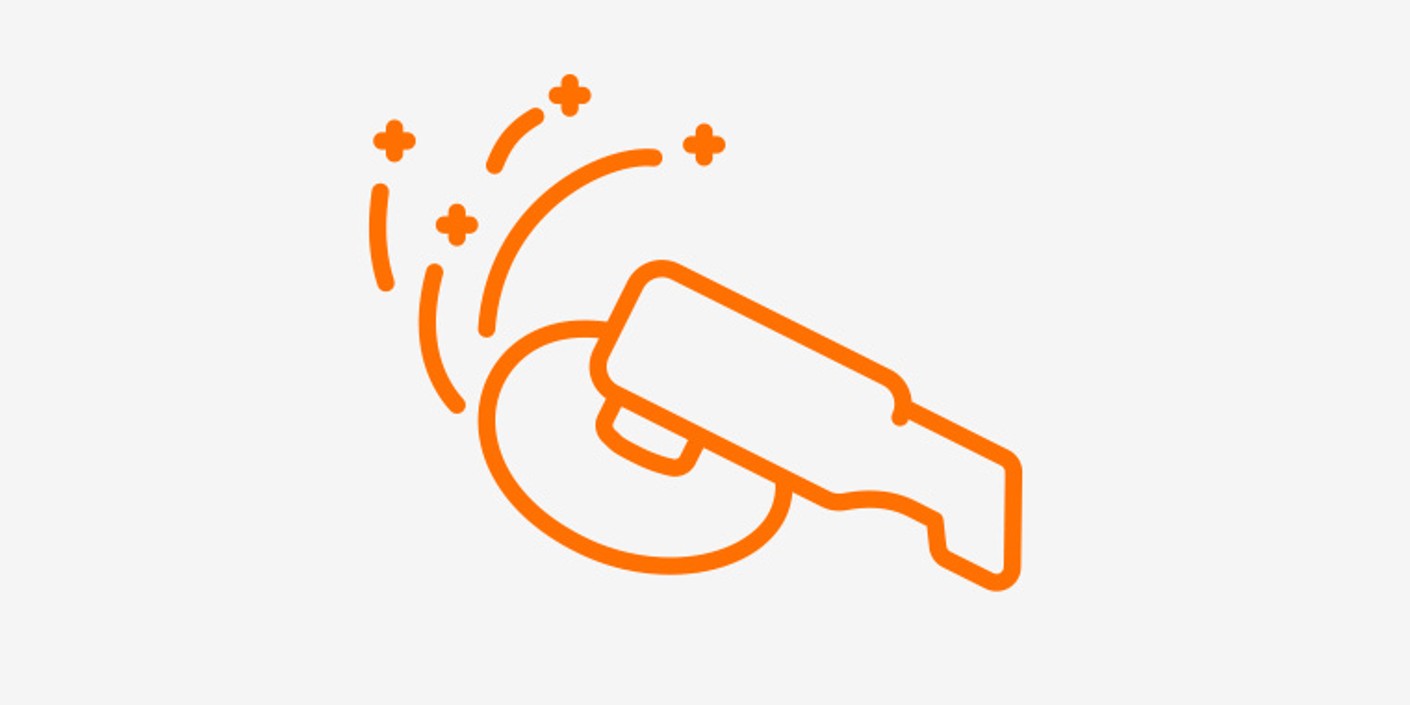
Press to remove
Grinding technology comes in lots of variants – rotating tools like grinding discs, linishing machines or orbital sanders. All of them are designed to refine and improve the surface quality of semi-finished steel products, precursor products like slabs, ingots or billets, near-final products like iron beams, sheets or plates and to shape structural steel to order.
But besides the tools, how high a force is applied for how long is also a key aspect: greater pressure means greater removal rate. And there's grit size, too. The larger the grit, the more material gets removed.
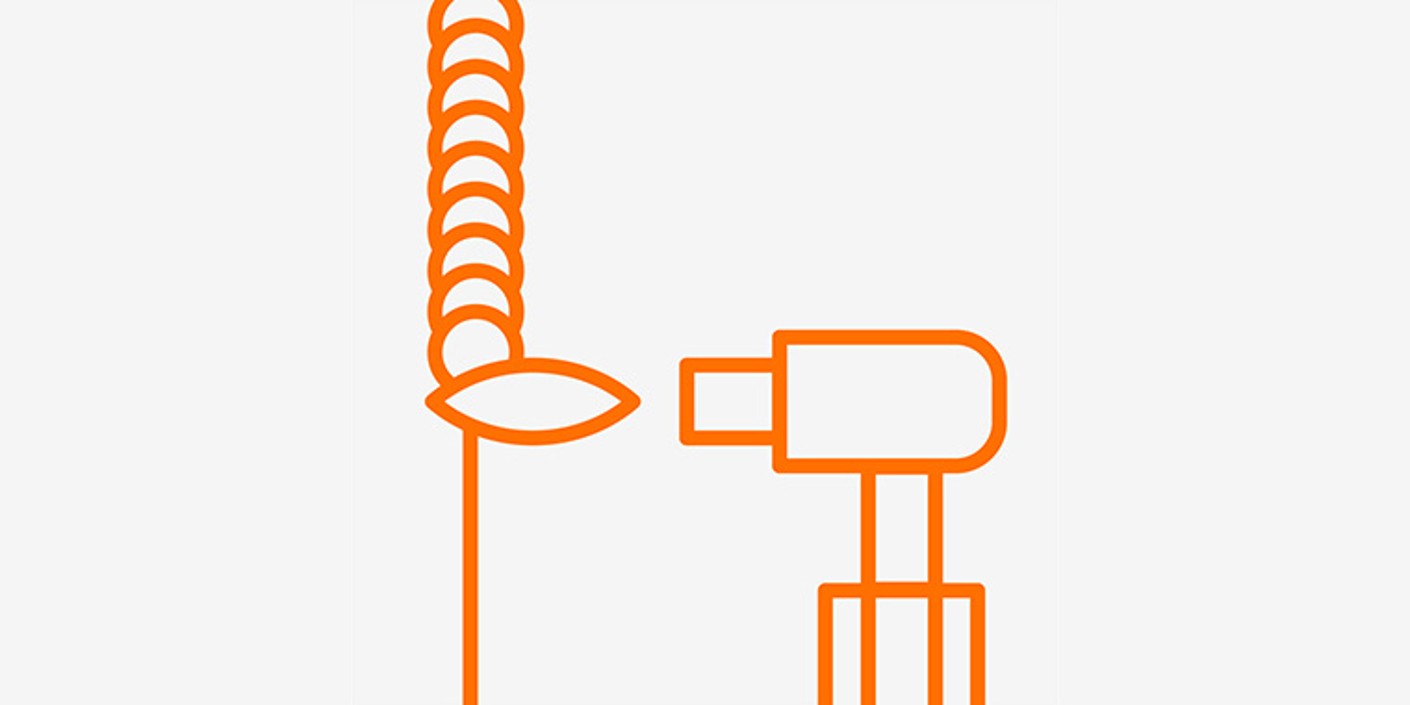
What we want and what we get – invisible weld seams
Smooth to the touch – precisely what you can get any weld seam on structural steel to be if you follow a number of rules. Choose your grinding tool to match your workpiece, its surface and geometry and then identify the appropriate grinding media. For this step, it makes no difference whether you merely want to grind down a weld seam or actually machine the surface itself.
- Begin with the smallest grit size if you’re after a perfect surface finish.
- Don’t switch to a higher grit size until removal no longer meets your demands.
- Keep an eye on the contact pressure – sometimes less is more!
- Watch out, too, for disc vitrification, excessive heat generation and unusual grinding noises. All of these can mean that contact pressure is too high or that the grinding media’s tool life is reaching its end.
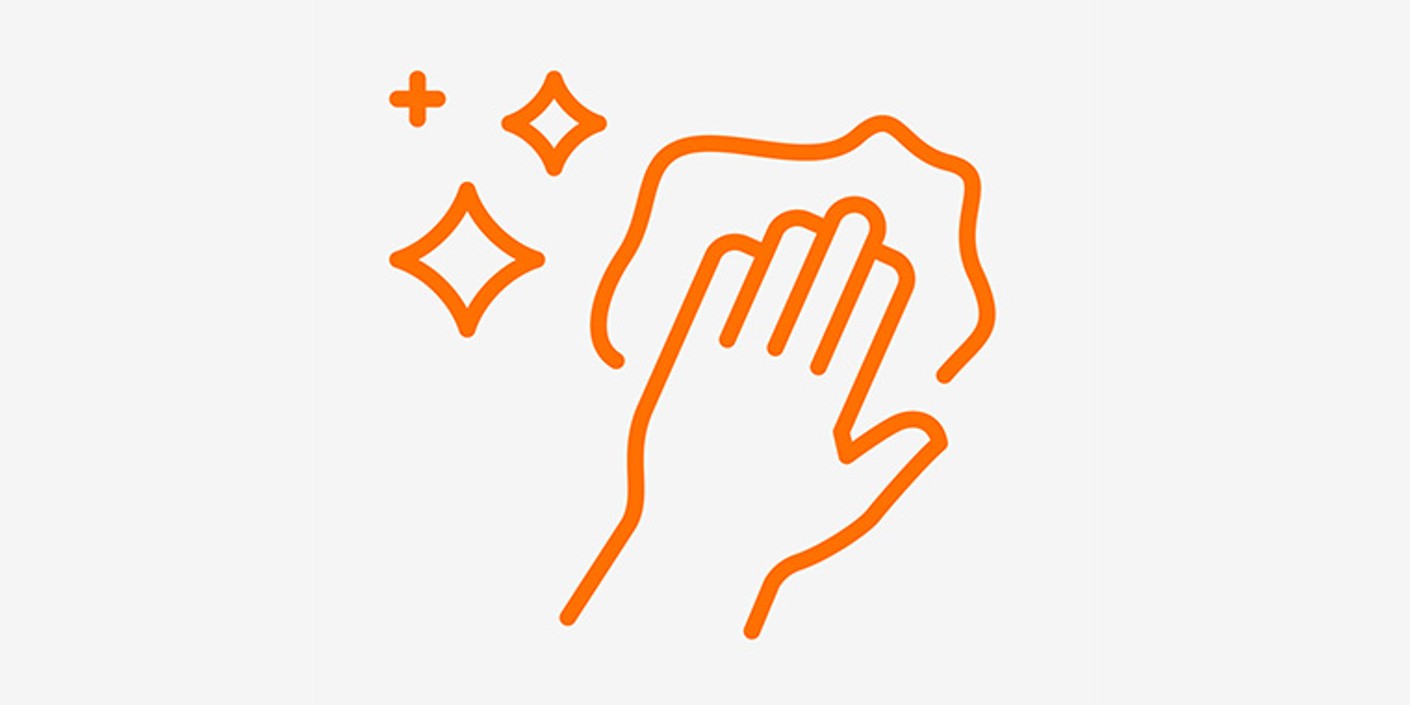
Polish – beauty treatment and more
Occasionally, structural steel needs to meet requirements concerning both function and form. At times like these, polishing is the remedy of choice, with the added benefit that you’ll also be sealing and protecting the surface. You can polish manually or using machines, which come in a whole range of power classes. To get a result to please the eye, make sure to look out for the following:
- Prepare your workpiece properly by pre-grinding/finishing
- Make sure that your polishing tool is compatible with the material
- Use optimum contact pressure
Tip: Use a scrap part to try out different contact pressures. - Keep your workspace clean and protect your polishing tool from contamination and soiling
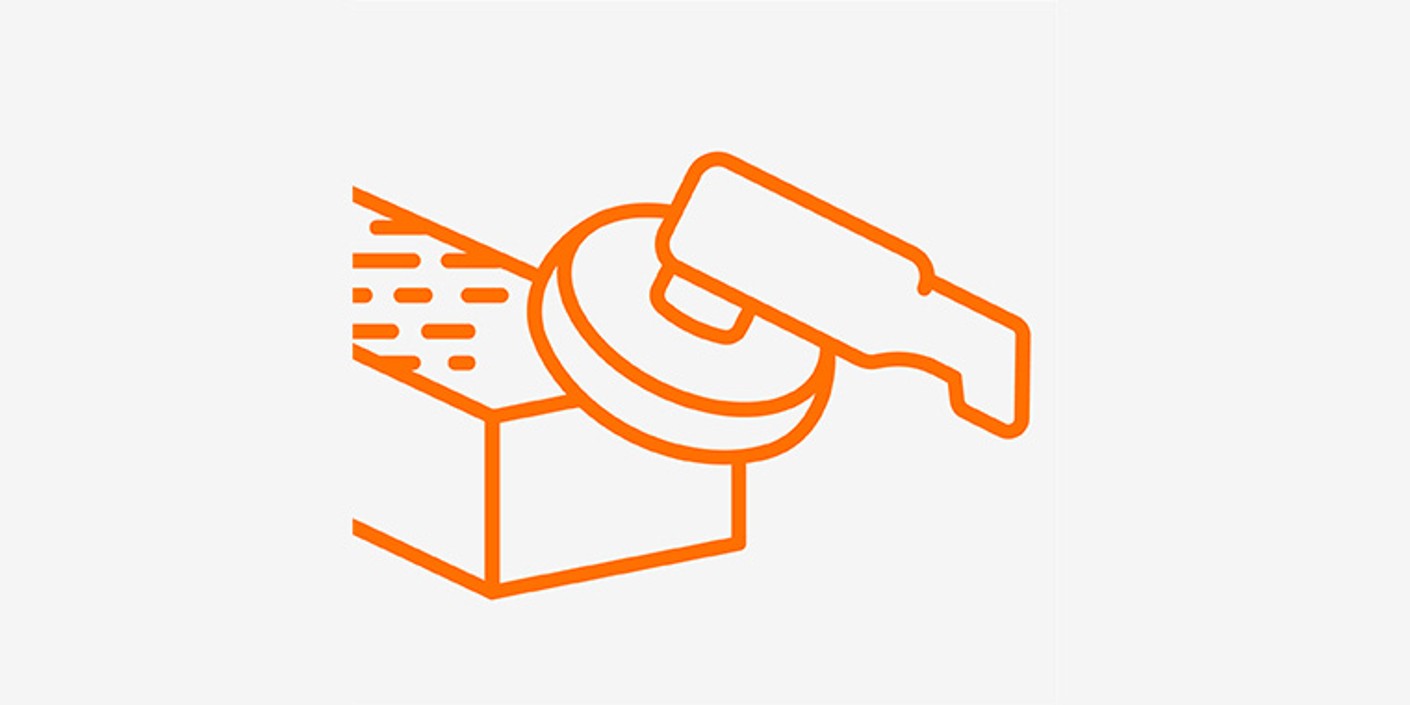
Sneaky opponents – water and oxygen
Structural steel will stand up to almost anything. Except, however, to water and oxygen. Ways to prevent corrosion include corresponding surface finishing, for example varnishing or galvanising. Regardless of form – pre-machined or raw sheet from your warehouse – structural steels require thorough cleaning before surface finishing. Oils and grease, for example, can be removed from the structural steels’ surface perfectly in a degreasing immersion tank.