On the cutting edge of quality – avoiding burrs

Some days, you’ll feel like you’re just chipping away at your work. On other days, there won’t even be any chips for you to cash in. Whenever you’re machining metals, polymers or stoneware, you’ll be first in line to see the cutting edge – forming burrs.
The principle mode of action in machining displaces material, thus forcing up unsightly and hazardous ridges along the edges of the workpiece. Burrs pose a tremendous risk of injury for yourself and your team.
Read on to learn about key aspects of how burrs form. We’ll also be showing you some simple and professional ways to remove burrs. Add knowledge of the ideal manual and power tools for burr removal to your skill set.
Burrs – a whole field of research in itself
You and your team will benefit greatly from understanding the complex mechanisms of burr formation. We’ve put all the essential information together for you at a glance:
- Burrs divide into primary and secondary burrs depending on the tool used. The former protrude at right angles to the surface and form mainly when punching or drilling.
- Secondary burrs, however, are parallel to the surface and form from planing, finish grinding, shearing, turning or milling.
- Another factor in burr formation is the width of the blade gap: cutting tools with a normal blade gap at the contact point with the cut part always produce a cut-off burr. The thicker your workpiece, the more prominent the burr. Tensile strength has the opposite effect: if it’s low, the burr is also smaller.
- Unlike cut-off burrs, what we commonly call tear burrs will always form when the blade gap is very wide. The cracks produced above and below no longer meet. This pulls part of the material downwards, tearing it off. This kind of burr is particularly strong and noticeably jagged.
- With too narrow a blade gap, a tensile burr forms: the material is not cut as the cracks pass each other by. This burr is thin and high.
- Bending produces rollover burrs, caused by the material bending around a punch.

Deburring – often the finishing touch
First choice of tools for machining burrs off edges or for finish grinding would be grinding wheels and brushes, for example. For smaller jobs, files will also do. You likely keep these on hand, already. When you need to remove burrs from rounded surfaces, grinding points or die grinder bits (themselves also referred to as burrs!) are well suited. Whatever the method or tool you're using, you’re always trying to remove excess material and smoothen rough surfaces. Sounds simple. And it is, too – provided you have the right tool handy.
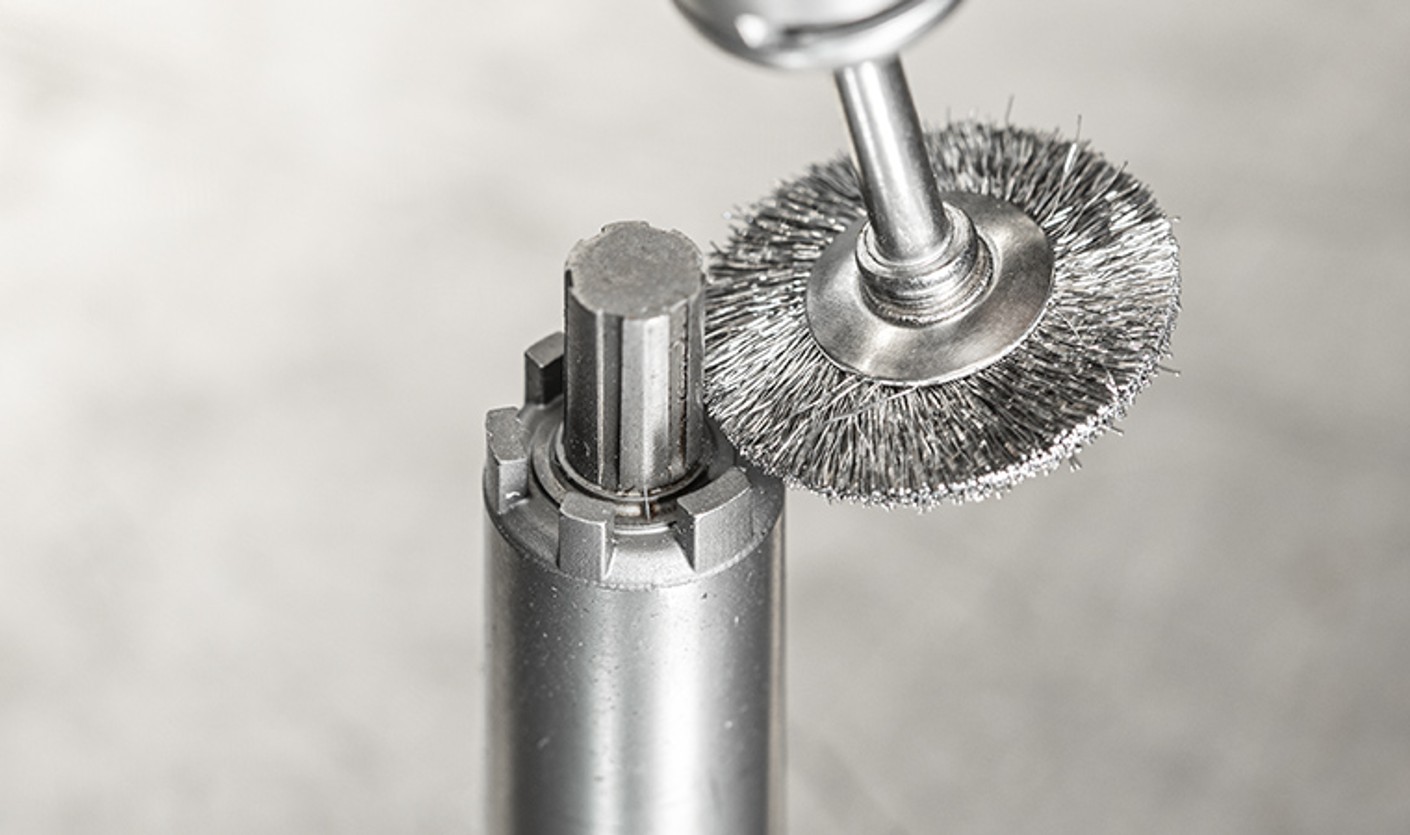
Ready, steady, brush!
Alternatively, you could also go for brush deburring. This method often uses an aqueous or oil-based emulsion additive or cooling lubricant and brushes off the unwanted burr. Dry brush deburring is rarely done in practice. A deburring brush’s abrasive filaments, threads and bristles are usually corrugated. They are made of polyamide, for example, which embeds silicon carbide (SiC) abrasive grit. Aluminium oxide or diamond grit (grit sizes from 40 to 8000 mesh) are widespread.
Tip: When removing primary burrs, we recommend using deburring brushes with comparatively rigid and straight bristles. For secondary burrs, brushes with angled bristles – angled against the grain – are better suited.
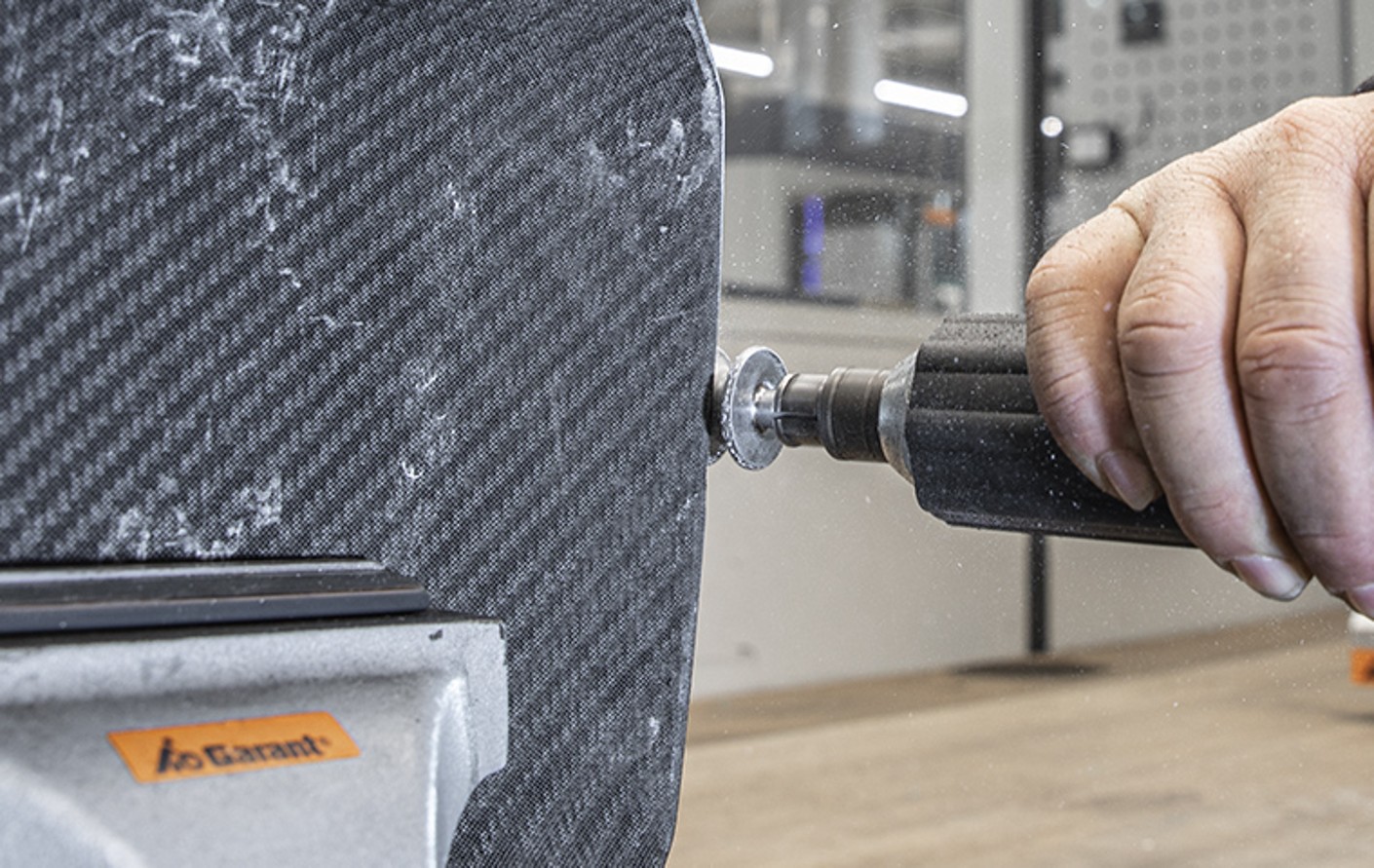
Different rules for plastic – fibre-reinforced and classic
If your workshop routine includes deburring polymers or plastic after injection moulding, you’ll need a range of tools on hand that allow for gentle but complete deburring of softer material. Brush, file, countersink bits, grinding disc, mill or tools with heat tech for thermal deburring – here, too, size and shape of the processed workpiece determine what tools are best. To debur small CRP and GRP components, for example, galvanically bonded diamond grinding points serve especially well. Just like when you’re doing grinding work, make sure your tools have large flutes between the diamond grit to ensure material is removed cleanly.
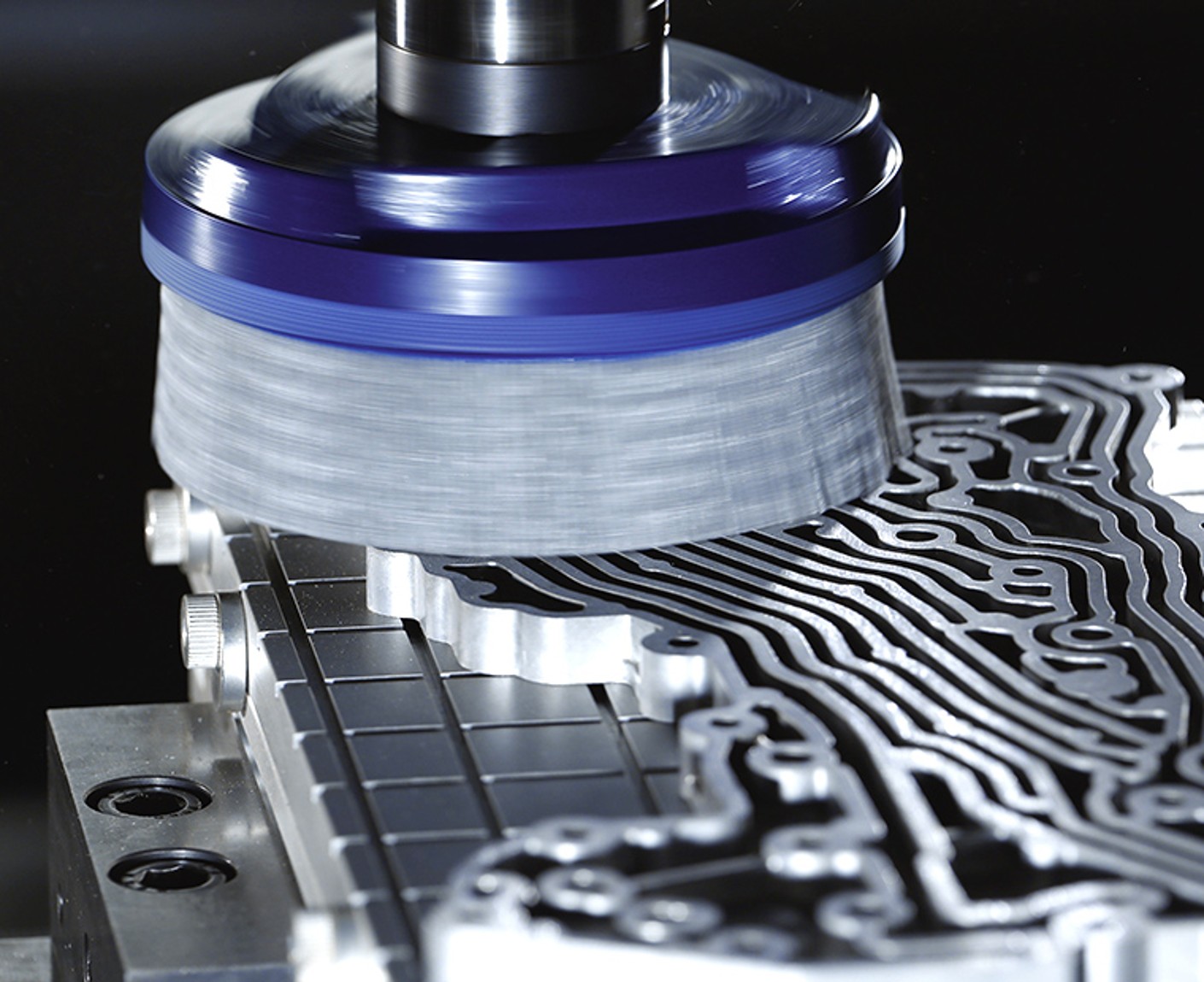
You can feel the quality
Quantity is key – no less true for choosing a deburring method than anywhere else. Recurrent deburring of large batches or entire production runs at industrial scale usually occurs through some sort of automated process immediately after production of the parts. The machines used often feature quick-change fixtures for smooth retooling. If your workshop includes an automated deburring machine, you’ll often have the luxury of being able to freely choose the tool to use. Otherwise, you’ll be familiar with the satisfaction you get when checking a part after deburring confirms A++ quality. It’s one of the reasons deburring is still done in many sectors in person, by manually operating machines – visual quality checks are fully incorporated. Note that you should always wear your personal protective equipment when deburring manually!
Note: Deburring by hand requires utmost concentration and skill, alongside solid experience with the material in question. Proceed with caution to avoid removing too much material.

You produce components and require top-quality deburring?
Do you think there’s scope for improving your products’ quality? Our experts will happily investigate your options and help you find the best tools for perfect deburring.