GARANT Master Chuck hydraulic chuck: Stretches the limits of what is possible!
Advantages and disadvantages of conventional hydraulic chucks
The advantages of a conventional hydraulic chuck are plain to see. In practice, however, the problems of clamping with conventional chucks are also well-known – high temperatures during machining can cause the oil to expand in the chambers and the bushing to burst at the soldering point, for example. In addition, not all chucks are suitable for all applications – partly because the holding forces are insufficient and partly because it is impossible to access hard-to-reach areas.

How does a hydraulic chuck work?
The pressure pin is moved via an actuating screw, which generates pressure in the oil chambers. The generated pressure compresses the pressure sleeve in the elastic area and thus clamps the respective tool in a manner that creates a frictional connection.
Advantages of a conventional hydraulic chuck
- Longer tool life
Thanks to outstanding vibration damping. - Perfect results and maximum precision
Both in terms of the concentricity and the repetition accuracy. - Easy to use – just one screw required
No special additional equipment/accessories are needed. - Incredibly versatile due to reducing adapters
All common tools can be held.
Disadvantages of a conventional hydraulic chuck
- Insufficient clamping force
Particularly for heavy-duty machining. - Interference contour
Hard-to-reach areas are not reached. - Temperature
Possible failure due to increase in temperature – especially in continuous operation.

The new GARANT Master Chuck hydraulic chucks
When developing the new GARANT Master Chuck, we took the well-known merits of a hydraulic chuck a step further and added several more compelling, advantageous features. This means you can take tool clamping work in your Production department to the next level and achieve the best results and maximum repetition accuracy.
With the new GARANT Master Chuck, we have significantly expanded the possible application areas for hydraulic clamping technology.
Highlights include the changed design of the chambers inside and the resulting clearly improved properties – a clever solution that maximises power and precision.
Would you like to find out more? Simply contact us.Arrange a consultation now
The GARANT Master Chuck is available in 2 versions and offers unbeatable advantages
FULL SPEED AHEAD:
Master Chuck Performance
Ideal for heavy-duty machining
Thanks to the highest possible holding forces

ACCESS ALL AREAS:
Master Chuck Slim
Perfect access
Thanks to slim outer contour
Master Chuck Performance: Maximum performance. Extra-long tool life.
- Even easier to use
Thanks to the new position of the clamping screw. - Higher temperature resistance
The new, patented bushing technology reduces the oil volume, improving stability and safety when subject to high temperature influences. - Improved application/distribution of the forces
Thanks to new, patented bushing technology. - Significantly less manual tightening force required
Thanks to special mechanics, less torque is required whilst simultaneously achieving the highest possible clamping force. - Longer tool life
Up to 10x more clamping cycles than conventional chucks

Blue: GARANT Master Chuck | Grey: Hydraulic chuck | Red: Shrink-fit chuck
Master Chuck Slim: Ideal shape. For the best access.
- Very easy to use
No shrink-fit unit required. - Better surface quality
As vibrations are minimal. - Quicker machining
- Higher clamping force
Compared to conventional hydraulic chucks. - Protect your employees
No injuries caused by the shrink process. - Higher temperature resistance
Thanks to new, patented bushing technology.

Find the right hydraulic chuck for you
Simply the perfect choice
We have put together a brief overview of the various tool chucks and their special features. Even just a quick glance at the table shows
that in terms of the application range, you can’t go wrong with the GARANT Master Chuck. And the clamping force can more than keep up!
Fields of application
![]() | ![]() | ![]() | ![]() | ![]() | |
---|---|---|---|---|---|
Applications / Chucks | Standard hydraulic chuck | HT hydraulic chuck | Slim hydraulic chuck | Master Chuck Slim | Master Chuck Performance |
Drilling | |||||
Deep hole drilling | |||||
Milling, roughing | |||||
Milling, finishing | |||||
3D finishing | |||||
Reaming | |||||
Countersinking |
Holding torques
Diameter (mm) | Master Chuck Performance | Standard Hydro Chuck | HT hydraulic chuck | Standard shrink-fit chuck |
---|---|---|---|---|
6 | 24 Nm | 20 Nm | 24 Nm | |
8 | 47 Nm | 35 Nm | 45 Nm | |
10 | 85 Nm | 50 Nm | 82 Nm | |
12 | 130 Nm | 90 Nm | 130 Nm | 145 Nm |
14 | 240 Nm | 120 Nm | 190 Nm | |
16 | 350 Nm | 170 Nm | 200 Nm | |
18 | 430 Nm | 240 Nm | 290 Nm | |
20 | 520 Nm | 330 Nm | 520 Nm | 450 Nm |
25 | 400 Nm | 530 Nm | ||
32 | 650 Nm | 900 Nm | 700 Nm | |
Tested in continuous operation up to: lm 1.2343 | 1.5 x D slot milled from solid | 0.5 x D slot milled from solid | 1 x D slot milled from solid | 1 x D slot milled from solid |
My production. My system. From GARANT.
A crucial factor in your production workflows is how the various components interact. A balanced system of high-quality tools and accessories can make a key difference. We help you achieve the perfect result with the GARANT system concepts, expert advice and the extensive Hoffmann Group portfolio – so you’re guaranteed to take no risk.

Machine tools
What does a machine tool have to do to achieve perfect results?
- It must have the required stability.
- It requires a suitable spindle in terms of speed, balancing quality and bearing.
- Performance parameters (speed, feed rate, etc.)
- Production options (e.g. 5-axis machining)
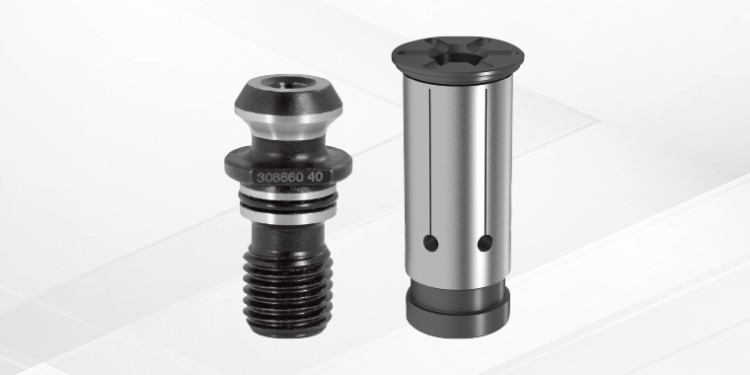
Accessories
- Pull stud
The interface between the spindle and the arbor (e.g. for an SK adapter). The pull stud should be suitable for your machining job. - Reducing adapters
Not only make the hydraulic chuck more versatile, they also increase the clamping forces on the tool.
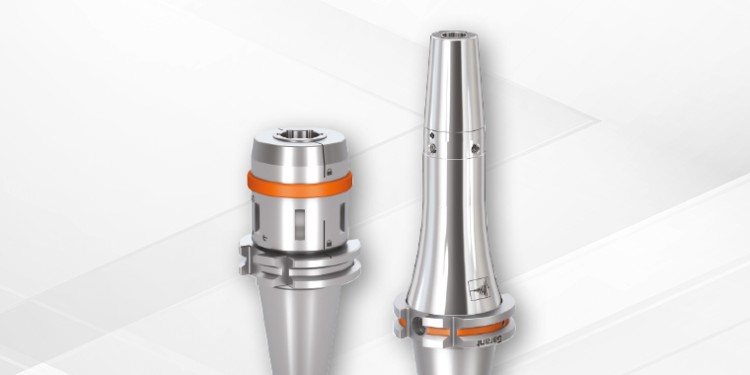
Tool chuck
The arbor has the task of clamping the tool and absorbing the forces. The following factors are important when selecting tool clamping devices:
- Concentricity
- Repetition accuracy
- Balancing quality
- Process reliability
- Flexibility

Workpiece clamping
As the workpiece clamping device is what connects the workpiece and the machine, you should not make any compromises here. Observe the following parameters:
- Flexibility
- Automation capability
- Clamping force
- Repetition accuracy
- Accessibility
- Handling

Machining technology
The effectiveness of your machining tool makes all the difference to how productive and reliable your work is. When selecting the right machining tool, observe these criteria in particular:
- What material is being machined?
- What cooling method is being used?
- Which machining strategy did you choose?
Do you need advice?
Our experts will be delighted to advise you on the new GARANT Master Chuck or
will work with you to optimise your production process.