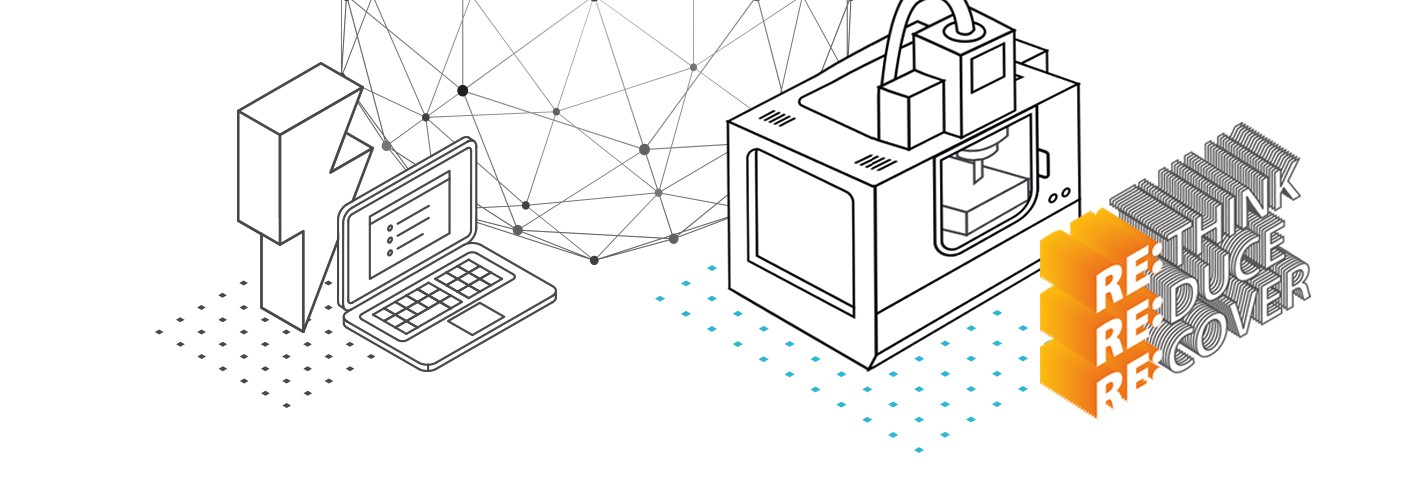
La digitalizzazione della produzione per migliorare l’impiego delle risorse
Un esempio pratico con il Connected Manufacturing
Dopo aver visto più da vicino le possibili leve per ottimizzare il processo produttivo, fornendo una panoramica sulle possibilità della digitalizzazione, illustriamo in particolare il potenziale di un migliore utilizzo delle risorse attraverso il Connected Manufacturing.
Quando si parla di ottimizzazione del processo produttivo, di solito ci si riferisce ai tempi di attività delle macchine; tuttavia, è necessario distinguere tra tempo di funzionamento della macchina e tempo di funzionamento del mandrino.
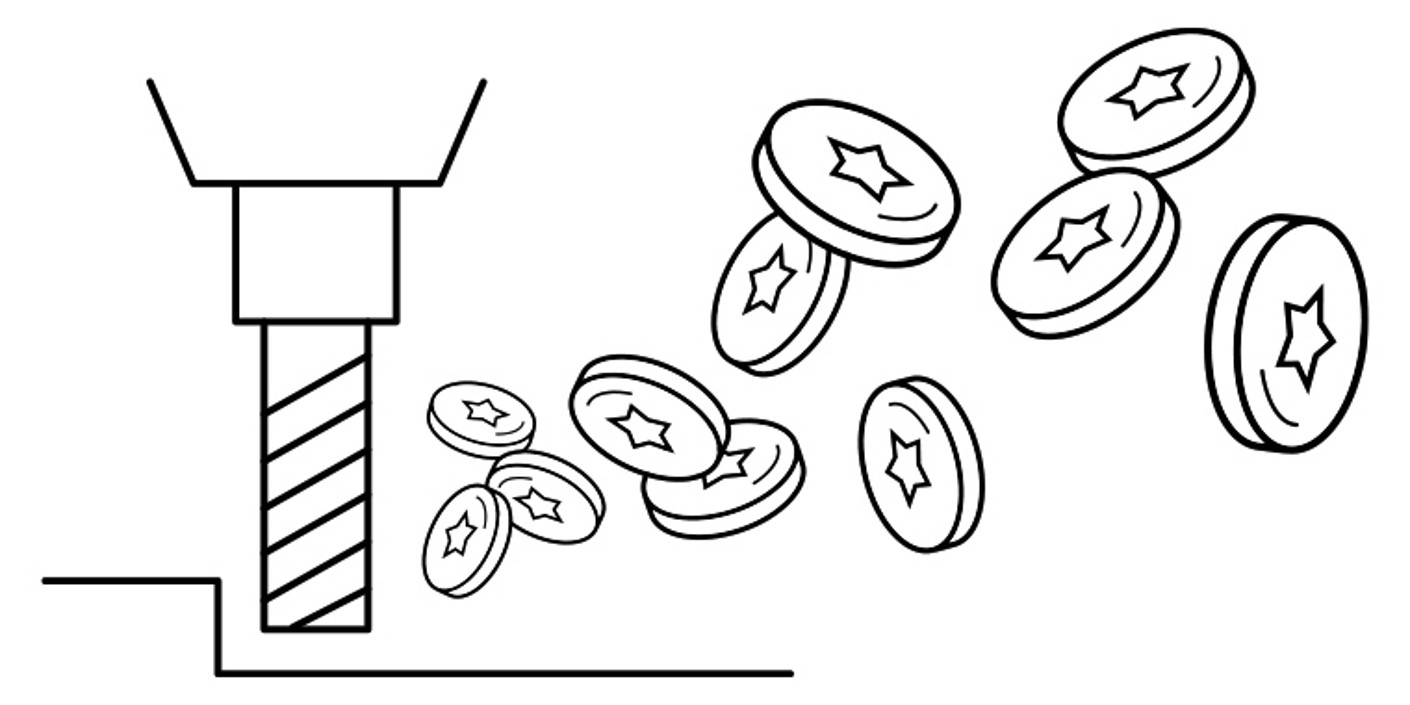
Tempo di funzionamento del mandrino
Tempo durante il quale la macchina produce effettivamente un pezzo. La macchina non è solo accesa, ma lavora in modo produttivo e produce trucioli.
Durante il tempo di funzionamento del mandrino si produce profitto.
Tempo di funzionamento della macchina
Tempo totale in cui una macchina è accesa, sia che sia produttiva sia che sia inattiva.
Durante i tempi di inattività delle macchine, vengono sostenuti costi inutili o riducibili.
Il tempo di funzionamento del mandrino come indicatore di efficienza economica
Il tempo di funzionamento del mandrino rappresenta il parametro essenziale per valutare la redditività di un'azienda. Non a caso, i tempi di funzionamento del mandrino sono il KPI (Key Performance Indicator) della lavorazione. In economia aziendale, con questo termine ci si riferisce a indicatori che descrivono il successo, le prestazioni o l'utilizzo dell'azienda, delle sue singole unità organizzative o di una macchina*. I dati del 2022 del Marktspiegel Werkzeugbau lo dimostrano chiaramente:

In sintesi, per generare un'ora di funzionamento del mandrino sono necessarie in media 1,3 ore di personale. La quota operativa ammonta a ben il 75%. Ciò significa che solo il 25% del lavoro nell'industria viene svolto senza l'intervento umano, rendendo l'impegno del personale un fattore molto importante.
I dati medi del settore metalmeccanico sono stati confrontati con quelli delle cinque migliori aziende, le quali presentavano un grado di automazione superiore del 58%. Digitalizzazione e automazione sono quindi un elemento centrale per la redditività che le aziende dovrebbero tenere sotto controllo**.
Digitalizzazione della produzione con il Connected Manufacturing
Con Connected Manufacturing offriamo una soluzione semplice e flessibile per la digitalizzazione della produzione. L'obiettivo è sfruttare al meglio le risorse esistenti, in particolare le macchine di lavorazione e le loro periferiche. Con l'uso della soluzione digitale, è possibile ottenere un tempo di mandrino più lungo rispetto al tempo totale di funzionamento della macchina.
In media, in tutto il settore, solo un massimo del 45% del tempo di produzione della macchina disponibile viene effettivamente utilizzato in modo produttivo. Dal punto di vista delle aziende, la leva più importante per lavorare in modo sostenibile ed efficiente dal punto di vista energetico è aumentare di conseguenza l'uso attivo della macchina. Grazie a operazioni preparate in modo ottimale, che evitano inutili tempi di ricerca e di cambio, questo valore può essere aumentato in modo significativo con poco sforzo.
I vantaggi della produzione connessa
In che modo il Connected Manufacturing può contribuire a un migliore utilizzo delle risorse?
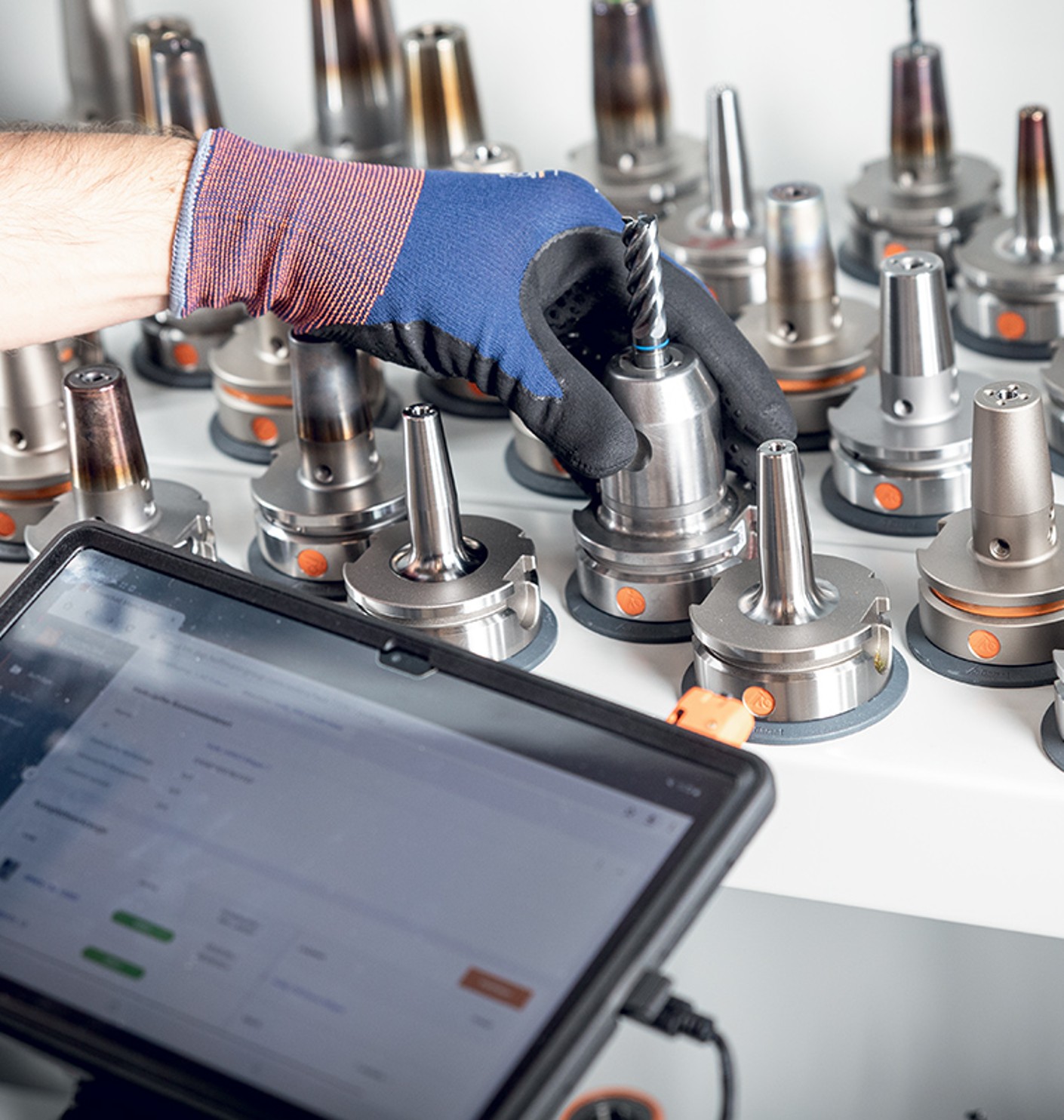
Eliminazione dei tempi di ricerca degli utensili
Con i metodi di lavoro tradizionali, di solito non è chiaro al programmatore CAM quali utensili siano disponibili in produzione. Ciò aumenta spesso i tempi di ricerca, perché l'operatore della macchina o presetting degli utensili deve cercare, assemblare o ordinare gli utensili utilizzati dal programmatore CAM. Purtroppo, questo processo richiede ha tempi così stretti che la macchina può bloccarsi. Il Connected Manufacturing rende trasparente quali utensili sono in magazzino e disponibili nello stesso momento.
Aumentare la sostenibilità
La sostenibilità gioca un ruolo fondamentale anche in relazione alle conoscenze aziendali già acquisite. In passato, il know-how su determinati processi di lavoro, suggerimenti e soluzioni per compiti specifici dell'azienda era spesso immagazzinato nelle teste dei dipendenti, ma oggi queste conoscenze devono essere rese disponibili a livello centrale nel senso dello sviluppo sostenibile. In questo modo, non si dipende dal know-how dei singoli e non si devono cercare nuove soluzioni per i compiti risolti, ad esempio in caso di cambiamento nell'area di responsabilità.
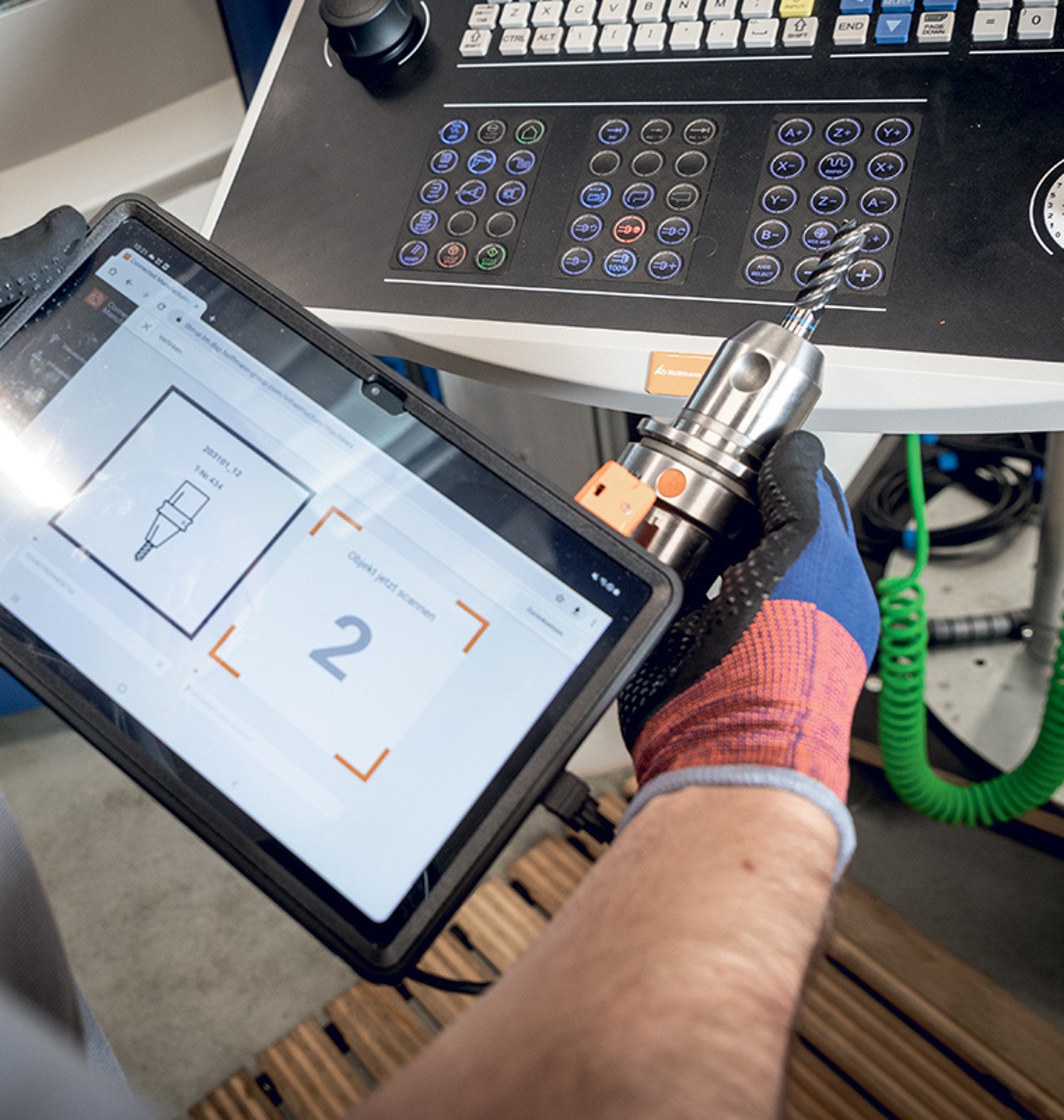
Trasmissione automatica dei parametri degli utensili
Con il Connected Manufacturing, i valori misurati rimangono sempre aggiornati e i valori modificati vengono continuamente sincronizzati. Con i metodi tradizionali, un utensile viene misurato x volte nel suo ciclo di vita, mentre con il Connected Manufacturing non sono necessarie altre misurazioni dopo quella iniziale. Grazie all'affidabilità operativa dei parametri dell'utensile, già documentati e quindi confermati, si possono evitare i pezzi di rodaggio; si evitano errori di digitazione che, in determinate circostanze, possono causare costosi danni alle macchine, rotture di pezzi, utensili, attrezzature e dispositivi di serraggio e si evitano lunghi tempi di fermo macchina dovuti alla ricerca di guasti.
Le macchine moderne richiedono tutta una serie di parametri per ogni utensile. Ad esempio: l'utensile ha un raffreddamento interno? È sovradimensionato o in sovrappeso? O che tipo di utensile è? Se non si tiene conto anche di un solo parametro, le macchine automatizzate potrebbero non funzionare per tutta la notte o il fine settimana. Il Connected Manufacturing trasmette automaticamente anche questi valori.
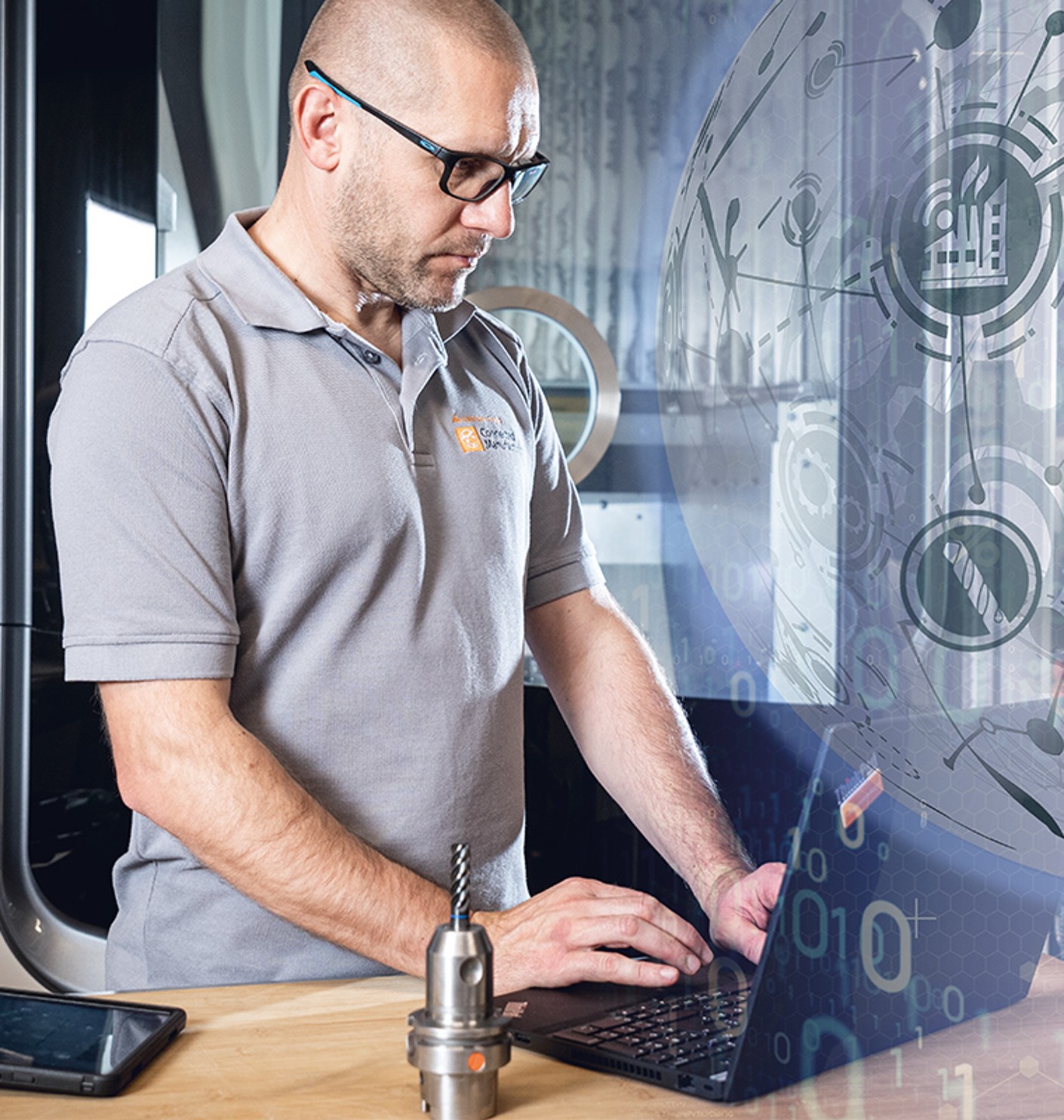
Panoramica della durata degli utensili
Con i metodi di lavoro tradizionali, il monitoraggio della durata degli utensili richiede molto tempo o è difficilmente realizzabile. Con il Connected Manufacturing è possibile avere una panoramica completa della durata di tutti gli utensili in officina. Soprattutto con le macchine automatizzate, spesso si verificano i cosiddetti "turni fantasma" in cui le macchine rimangono ferme perché la durata degli utensili è stata raggiunta o superata. Con il Connected Manufacturing è possibile controllare attivamente, prima della fine del turno, quali utensili sono prossimi alla fine della loro vita utile. In questo modo si riducono notevolmente i tempi di fermo macchina.
Le risorse vengono risparmiate grazie all'utilizzo ottimale dell'utensile. Poiché il monitoraggio della durata degli utensili non è solitamente possibile con lotti di piccole dimensioni, un'elevata miscela di materiali e utensili universali, gli utensili vengono spesso sostituiti prima del limite di usura come misura preventiva e un utensile ancora efficiente può venire smaltito troppo presto. Il Connected Manufacturing fornisce una visione reale del lavoro svolto dagli utensili e consente di eseguire ulteriori lavorazioni in modo sicuro.
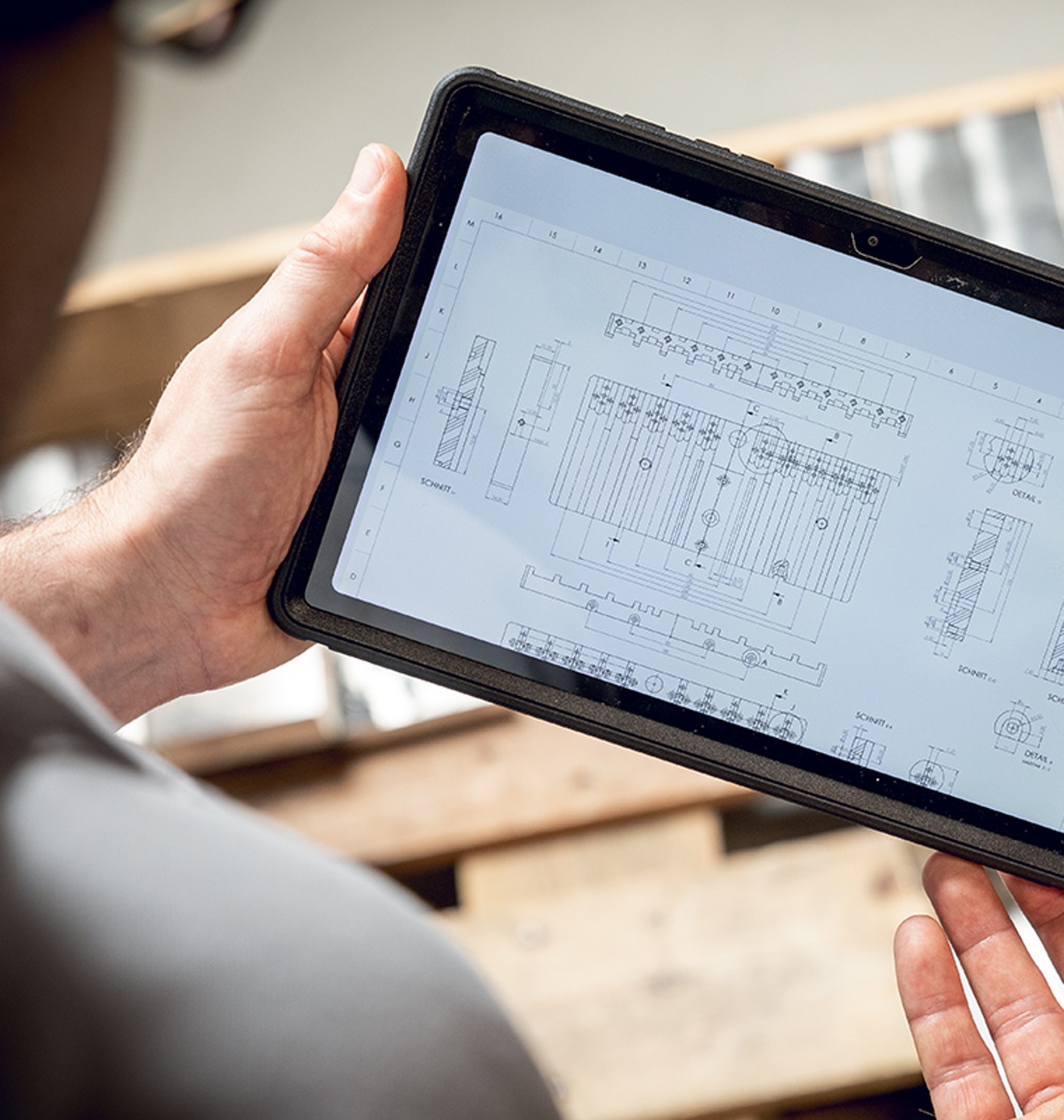
Affidabilità del processo grazie alla documentazione dell'intera sequenza
Affinché un processo di lavorazione sia affidabile, molti parametri devono essere corretti: programma NC corretto, utensili, dispositivi di serraggio, disegno, piano di serraggio o foto del serraggio, descrizione del punto di zero, protocollo di misura e ulteriori informazioni. Se manca uno solo di questi, non è possibile evitare un fermo macchina. Il Connected Manufacturing rende disponibili tutti questi dati a livello centrale. La documentazione di processo è a portata di clic: utensili, istruzioni di serraggio o di montaggio possono essere creati in pochi secondi con un tablet o uno smartphone e allegati direttamente all'elemento associato. Le liste utensili vengono generate automaticamente dai programmi NC "estratti" automaticamente dalle macchine. In questo modo si garantisce che l'ultima versione di un programma sia sempre collegata al componente corrispondente.
Migliore utilizzo delle risorse con il Connected Manufacturing
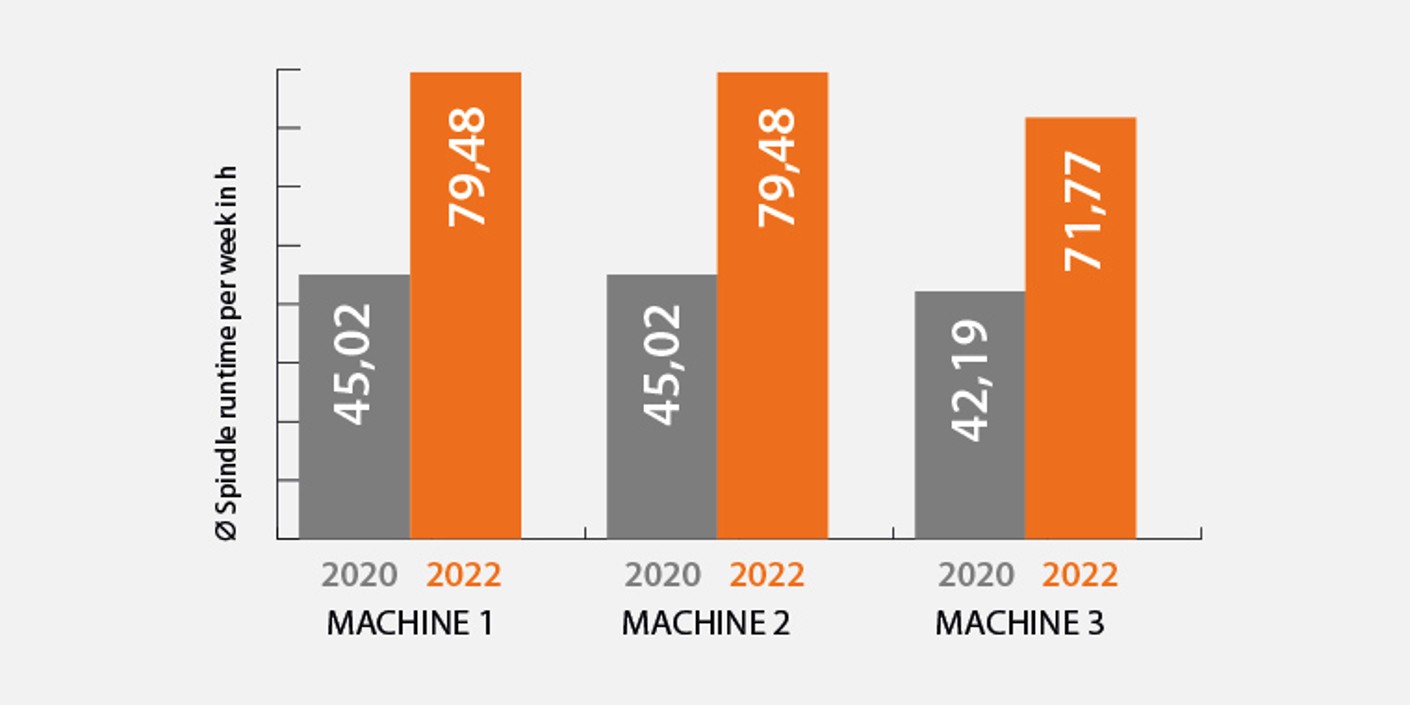
Vediamo l'effetto del Connected Manufacturing con un esempio concreto e come questa forma di automazione influisce sul tempo di lavorazione del mandrino. I dati sono stati raccolti da Hoffmann Group in collaborazione con il reparto di produzione utensili di Mühlhoff Umformechnik GmbH. L'affermata azienda produce componenti per il settore automobilistico ed è stata digitalizzata nel 2020 con la soluzione digitale Connected Manufacturing per quanto riguarda l'elaborazione degli ordini, la gestione dei dati e la gestione degli utensili. Abbiamo potuto vedere come il passaggio al digitale abbia influito sulla redditività.
Nell'esempio di Mühlhoff, abbiamo confrontato il modo in cui il grado di digitalizzazione o automazione influisce sul tempo di funzionamento del mandrino. Nel primo ciclo, il passaggio alla gestione manuale dei dati tramite Connected Manufacturing e alla programmazione sulla macchina ha già mostrato un aumento significativo del tempo di esecuzione del mandrino, pari al 45%.
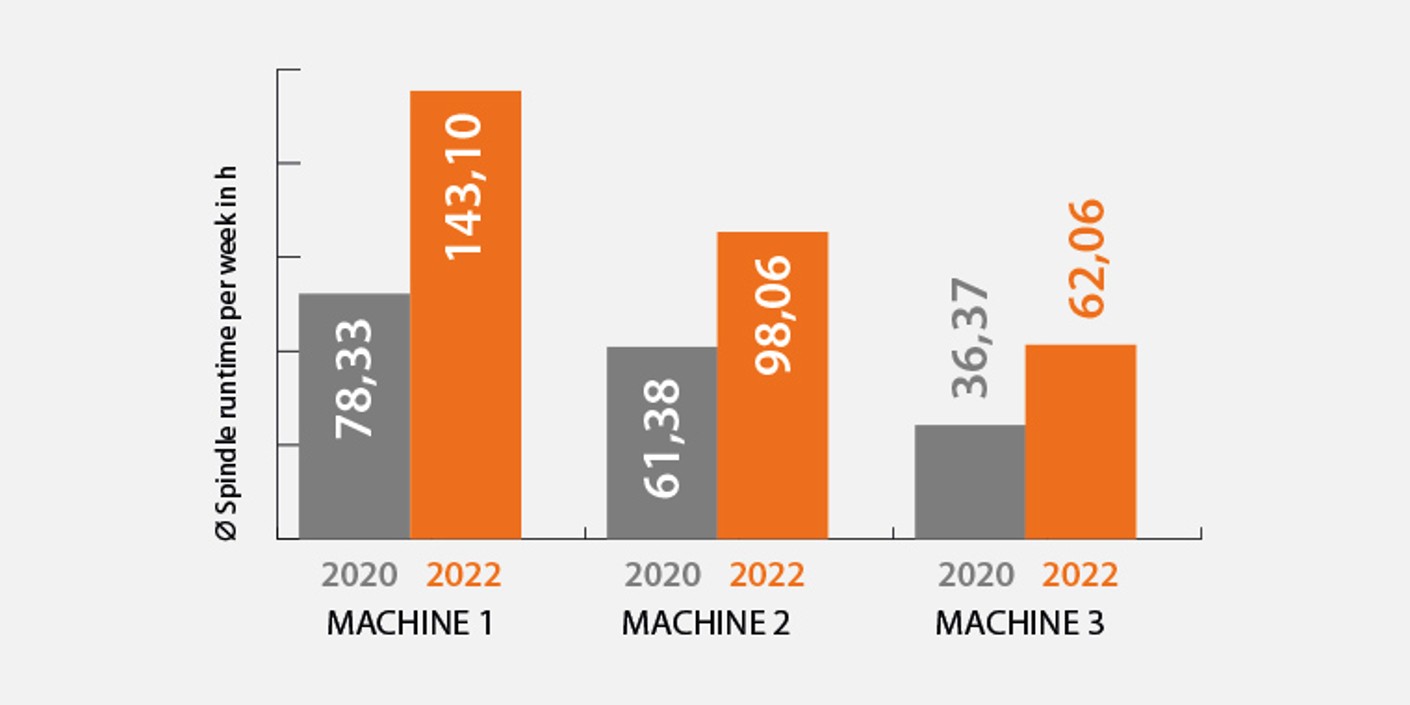
Se il livello di digitalizzazione è stato ulteriormente aumentato grazie alla gestione dei dati tramite Connected Manufacturing, alle soluzioni di programmazione tramite CAM e alle macchine automatizzate, nonché al metodo di approccio, il tempo di esecuzione del mandrino potrebbe addirittura aumentare del 75%.
Un dipendente ha generato 1,7 ore macchina per ogni ora utilizzata. In sintesi, è stato ottenuto un aumento del 33% nell'utilizzo del tempo di funzionamento del mandrino su tutte le macchine utilizzate. Il tempo di funzionamento teorico delle lamine si riferisce alle ore di lavoro dei dipendenti utilizzate a settimana.
Naturalmente si tratta di un esempio. L'impostazione deve sempre essere considerata individualmente. L'aumento del tempo di esecuzione realizzabile in ogni singolo caso dipende sempre dalla situazione di partenza. Tuttavia, le cifre registrate confermano il grande potenziale della digitalizzazione e dimostrano che la produttività aumenta in modo significativo.
* https://wirtschaftslexikon.gabler.de/definition/key-performance-indicator-kpi-52670
** Marktspiegel Werkzeugbau: Figures for the month of April 2022 • Pergler Media