Why you need the right technology to get a perfect surface finish
The nitty-gritty’s done, but we’ve not quite reached the final touches yet: as an industrial master craftsman, you and your workshop team tackle component surface grinding. Getting good machining results depends on a range of aspects: size of the surface, choice of the right tool and rotation mode, adjustment of speed to perfectly match the workpiece surface. Your aim: making the workpiece more visually attractive and the surface even smoother. Surface grinding doesn’t seek to remove material, nor any changes in shape. Because what you’re after is to refine the material’s surface further while painstakingly avoiding any removal of material, it’s especially important for surface grinding that you choose tool and grinding media with extra care. Continue reading to see what methods and tools we can present for surface grinding and to find out how to get the best-possible results.
Round and round are not alike – finding the right pattern of movement
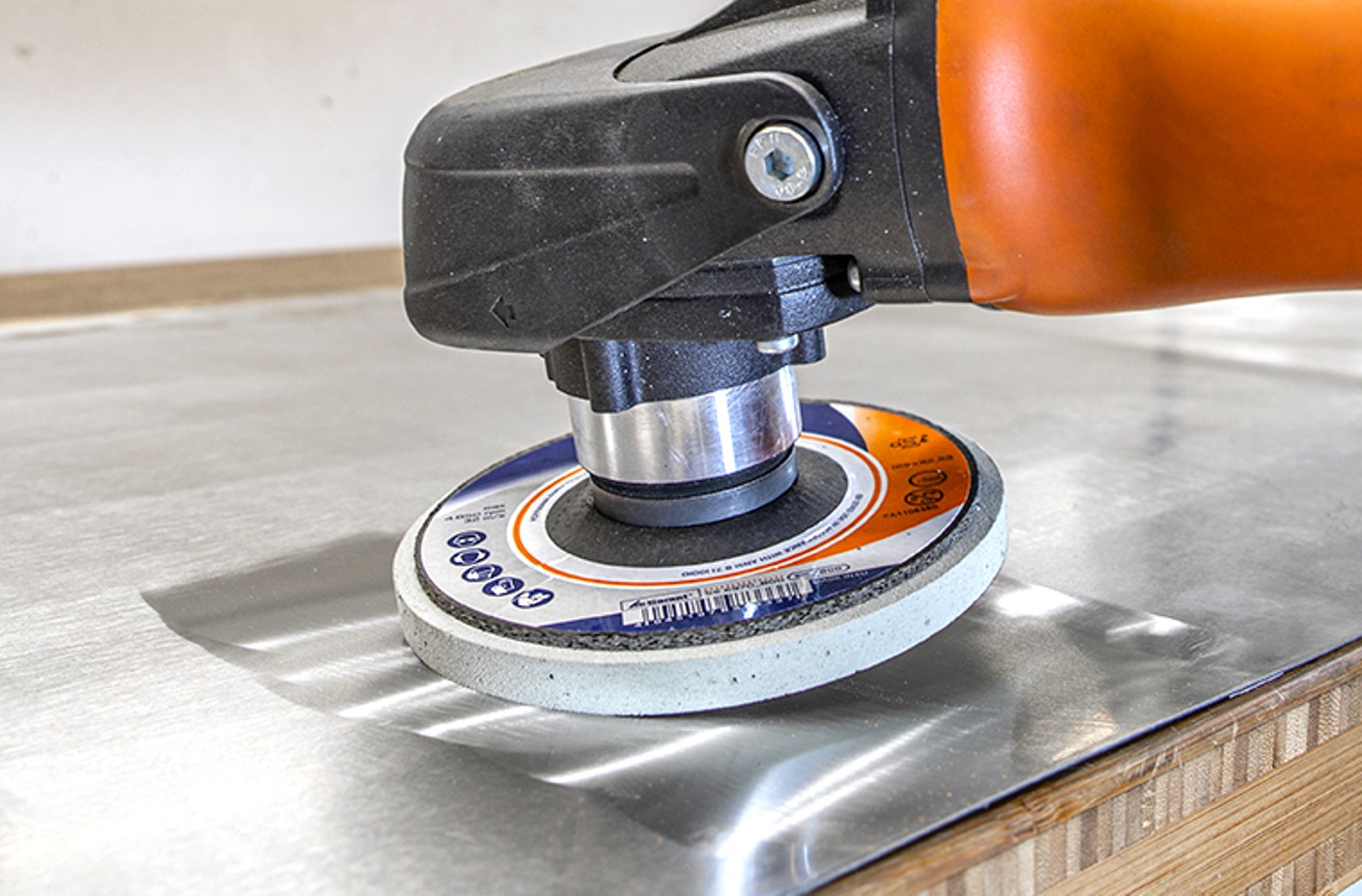
Unlike coarse grinding, surface grinding has only one purpose: obtaining the best surface quality technically feasible on a component. Because the parts and components used in industrial environments are manifold and vary incredibly from sector to sector and application to application, industrial workshop masters like yourself face a true test of skill: you need to handle all kinds of sizes and shapes, alongside a myriad different materials.
The range of available tools is accordingly diverse. One aspect are the machines, whose highly varied patterns of movement can impact surface grinding decisively:
- Rotation: your tool performs a simple axial or radial rotation.
- Circular: the underlay performs small, eccentric movements. The grit shifts to remove material from an irregular surface.
- Random circular: every circular rotation is overlaid with another rotary movement to create new circular motion and vortices. Technical jargon for this is ‘dual action’.
Tip: When choosing your tool, make sure you're getting the right pattern of movement. Circular and random-circular tools differ in their design. This gives you the option to employ a swinging action mode rather than classic rotation. Random-circular tools create eccentricity between spindle and motor. Although both kinds of motion patterns work for surface grinding using media on an underlay, you will get a smoother surface feel using random-circular grinders.
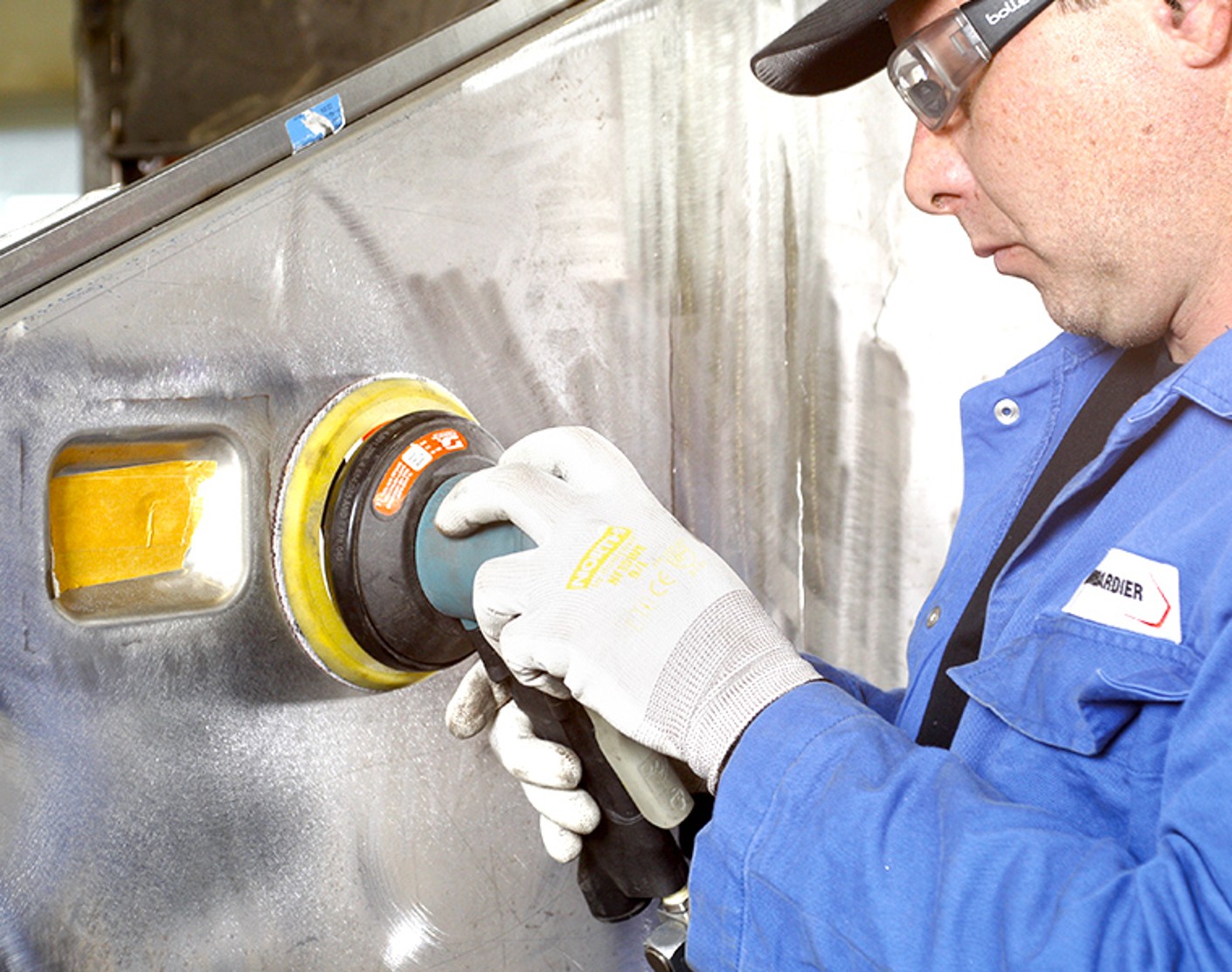
Disc, point or flaps – it’s the grit that defines surface grinding
Alternatively to classic grinding media on underlays, abrasive rollers or flap wheels are also suitable for surface grinding, and offer the benefit of greater grinding surface areas. The support discs for abrasive flap wheels can be made of plastic and glass fibre, paper, polyester fabric, cotton fabric, foil underlays or even sheet steel. Grit types you could use include aluminium oxide A, silicon carbide grit or zirconium-carborundum oxide, ceramic grit (CER) and diamond (D).
By using flap grinding discs for surface grinding, you’ll be benefiting from uniform wear on the separate flaps and constant feed of new abrasive cloth. Your disc will last longer and your work results’ quality will be higher.
Note: Flap grinding discs must always be used along the carrier body’s direction of action. This is indicated in the sleeve’s core.
Depending on component shape, you may need to employ grinding points. Possible grit types are aluminium oxide, standard aluminium oxide or mixed aluminium oxide but you could also use grinding points with polishing felt or that combine with diamond paste, for example.
Tip: If you need to get your surface extremely smooth, you should consider adding fluids. This way, worn-down grit is effectively washed off the workpiece surface during grinding. The fluid will also act as a coolant. Once you’ve finished surface grinding, you can further refine your surface by polishing.
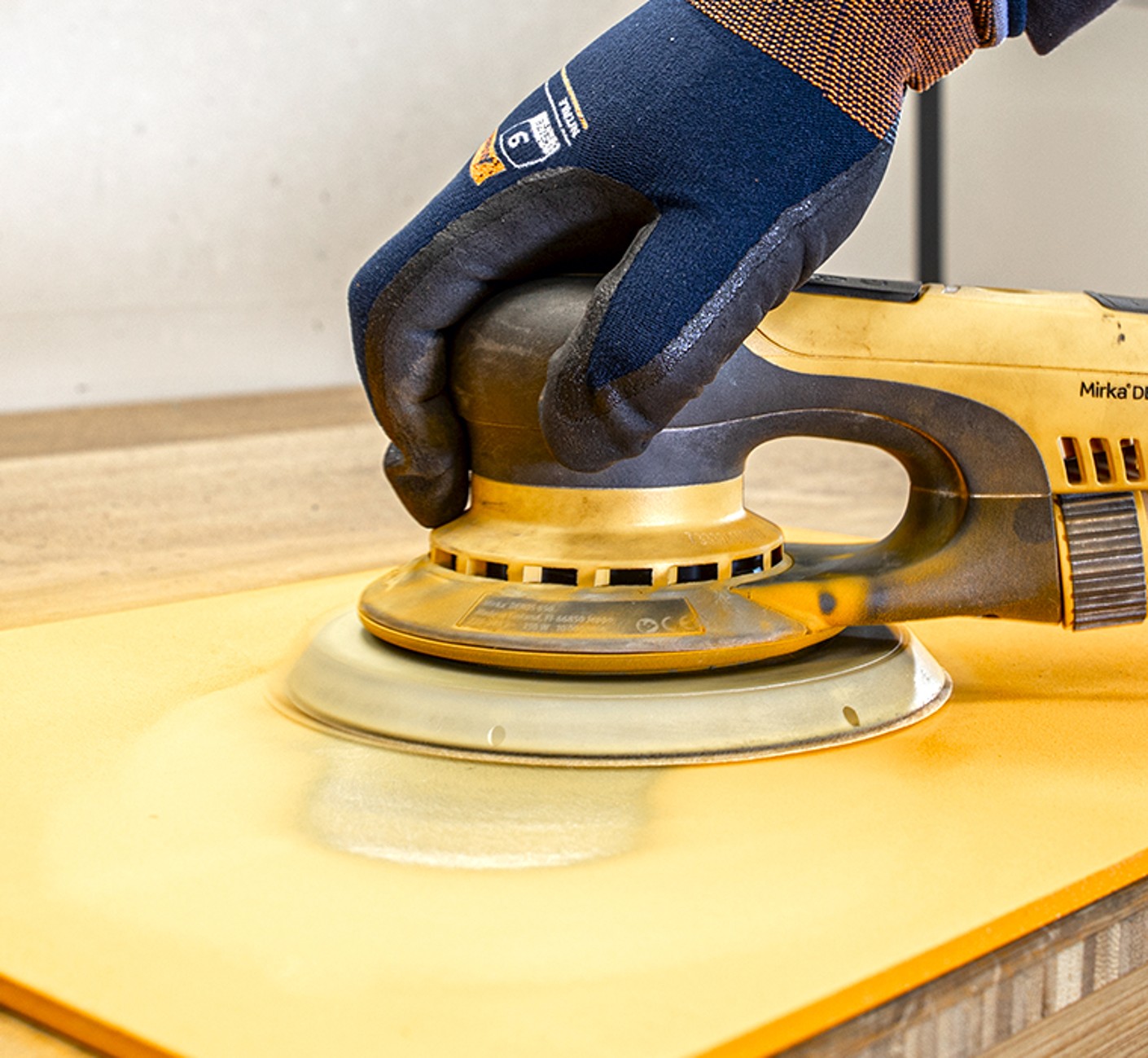
Why dialling it back is a good idea
1. Before starting on surface grinding, clean dirt, grease and material residue remaining from previous work steps off your workpiece’s surface.
2. Choose a tool and grinding media suitable for your workpiece, its size and its shape.
3. Start off by moving your grinding tool across the grinding surface cautiously and slowly. Apply only little contact pressure.
Tip: To test for results, vary speed rather than contact pressure. Alternatively, try different grinding media or grit. Make sure feed rate always matches speed. For surface grinding, we recommend never exceeding between 60 and 80% of the tool’s maximum speed.
4. Finish your work by wiping off all grinding detritus with a microfibre cloth.
5. If necessary, change your sanding disc for the next-smaller grit size and continue finish grinding.
Tip: Don’t skip any grit size steps. Your surface grinding will all be the finer for it.
Caution: The only way to get a regular finish is to keep the grinding media/tool in constant motion. Holding it in position impairs quality – the grinding media can literally dig into the surface.

You’d like to improve your surface grinding results while also extending tool life?
Are you looking for specific grinding media for an application? Do you need help choosing grit size for the perfect surface grind?