Physical cleaning is the foundation of flawless parts

As a master craftsman in an industrial environment, you know the component production process chain down to a tee – including final component clean-up in your workshop. But this step in the process, right at the end of production, isn’t the only one where cleanliness is critical. Maintenance, surface treatment before coating and of course when cleaning in industry sectors with stringent hygiene requirements all require working efficiently and without mistakes. DIN 8592 summarises the theory’s essentials. It defines cleaning as the “removal of undesired substances (contamination) from the surface or workpieces to a necessary, agreed or achievable degree”. Read on for some practical advice. Precleaning, interim cleaning, final cleaning – we’ll tell you how to get surfaces clean effectively, how this can considerably reduce the risk of component wear and corrosion and how subsequent work will achieve ideal results. We’ll also be telling you how to remove swarf, particles and chemicals without leaving a trace, and what you’ll need to look out for when doing so.
Cleaning components – there’s more to it than you’d think
As a proficient craftsman in the field of production, you and your team are judged not least on the quality and quantity of your department’s production. This applies to all of your workpieces and components whose surfaces need to meet high quality standards. But it applies just as much to the scrap that explicitly fails to meet these same requirements. So when it comes to cleaning, the benchmark you and your coworkers are measured against is as high as anywhere else. Contamination is prevented, and consequently functionality ensured, only if passive layers are removed completely, corrosion protection is complete and surface activation guaranteed – on every component. Because all of this is far more complicated than the simple term cleaning implies, the DIN 8592 standard doesn’t sort cleaning methods by their respective aim, but instead by their physical effect.
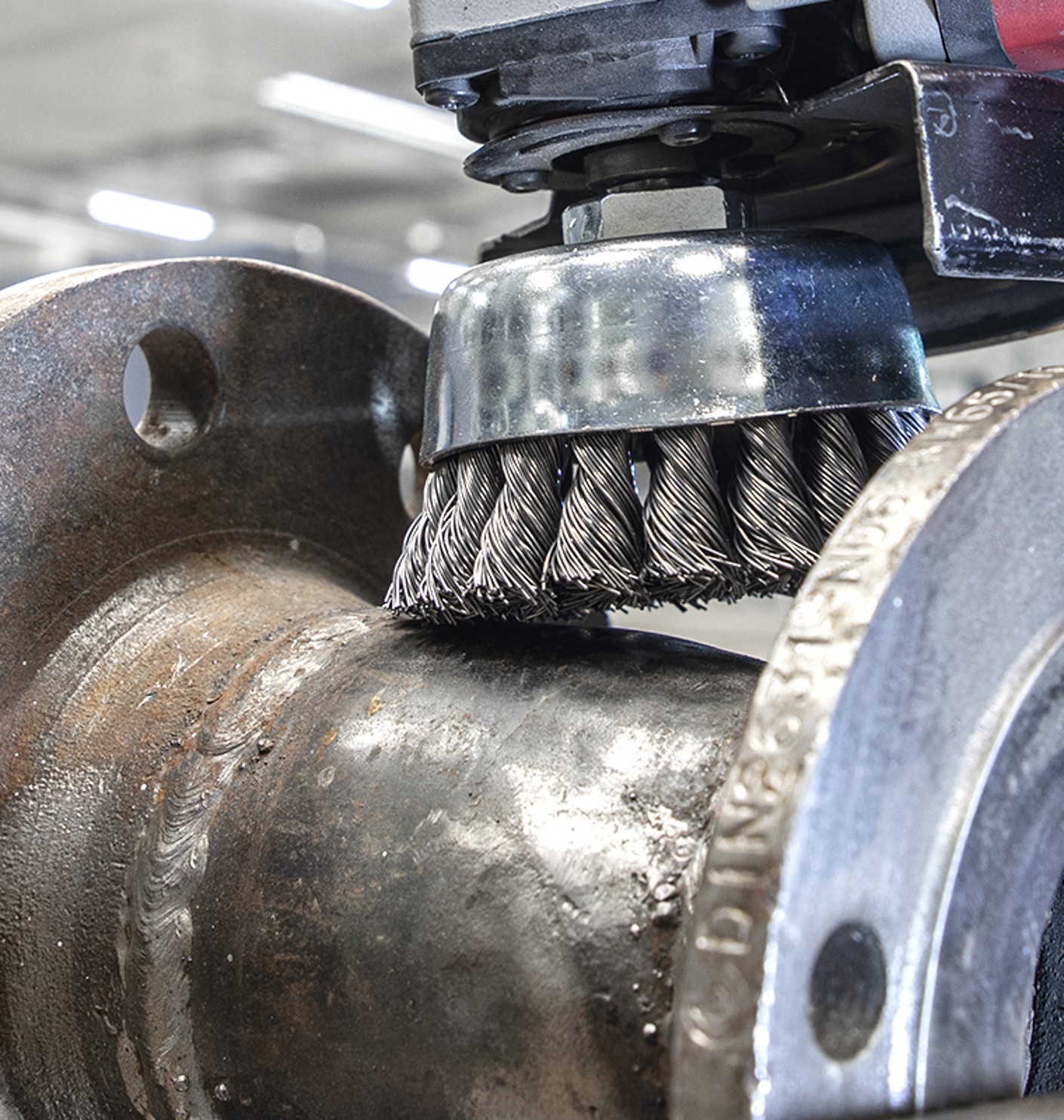
- Blast cleaning (compressed air, steam)
- Flow cleaning (washing or ultrasonic cleaning)
- Solvent cleaning
- Chemical cleaning (lye washes)
- Thermal cleaning (e.g. burn-off or glow cleaning)
- Physical cleaning (wiping, brushing etc.)
Background: A number of cutting methods with geometrically undefined blades are used, among other purposes, to clean surfaces – some of these methods are indeed designed specifically for this. In DIN 8592, the various cleaning methods overlap where multiple physical effects interact.
The destination determines the journey – choosing the right cleaning method
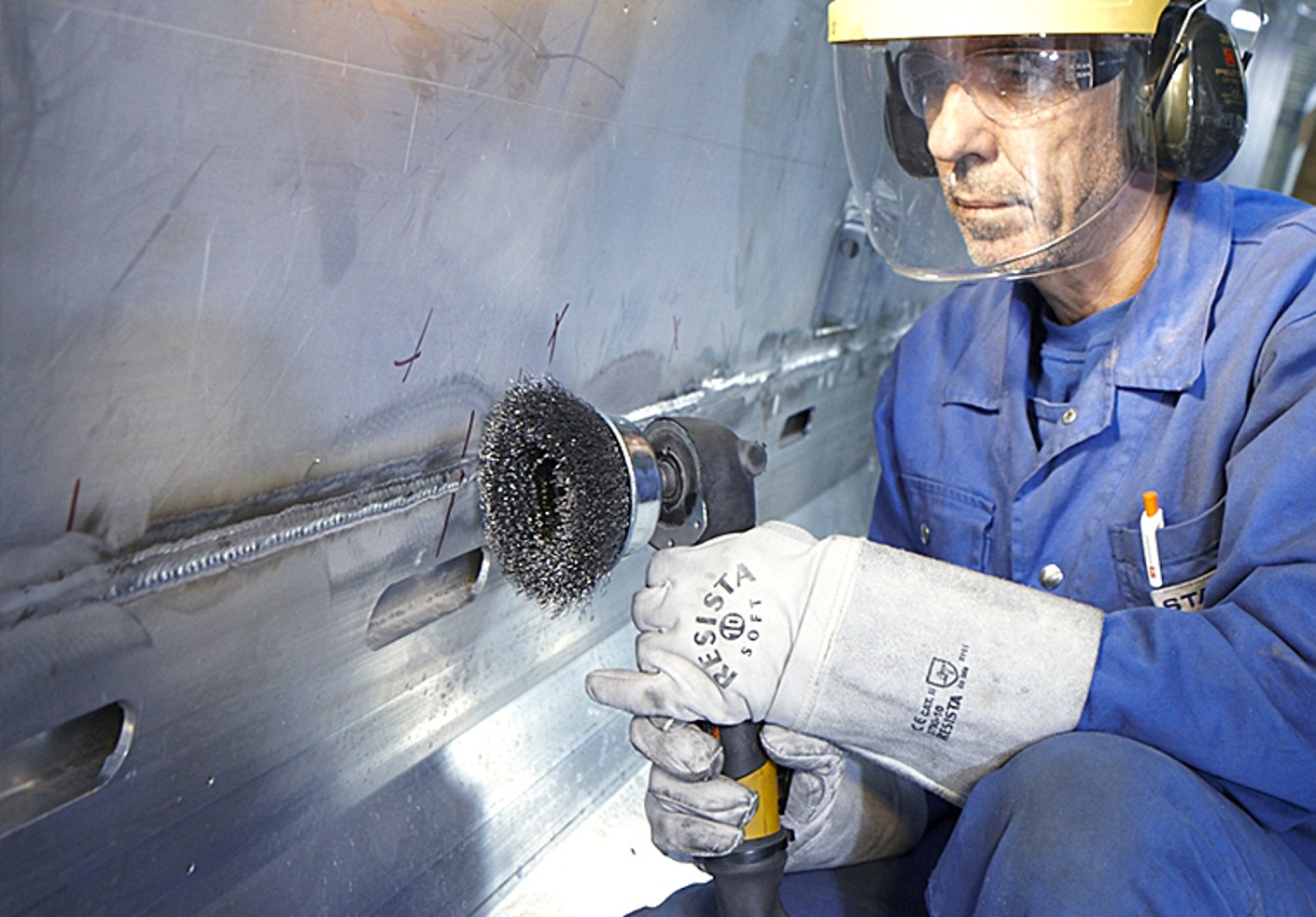
Physical cleaning methods can be further divided by looking at how they apply energy:
- Mechanical – abrasive: peening, grinding, brushing
- Mechanical – non-abrasive: stirring, mixing, ultrasonic, spraying

Talk to our specialists right away to find out what cleaning tools are best for your process.
Find out about the latest developments and get detailed advice on your options with a variety of materials.