Vitki pristop na področju nabavne logistike povečuje preglednost in prihodke.
Velika slika: izvori vitkega upravljanja
Izraz »vitka proizvodnja« izvira iz študije tehnološkega inštituta Massachusetts Institute of Technology (MIT) z naslovom »The Machine That Changed The World: The Story of Lean Production« (sl. Stroj ki je spremenil svet: Zgodba vitke proizvodnje).
Takrat so znanstveniki analizirali vse proizvodne sisteme, ki so bili v uporabi pri japonskih proizvajalcih avtomobilov, razvite po modelu Toyotinega proizvodnega sistema (Toyota Production System/TPS). Sam model TPS je nastal v petdesetih letih prejšnjega stoletja kot posledica krize japonskega avtomobilskega proizvajalca Toyote, ker so trgi pričakovali vedno večjo ponudbo vozil v majhnih količinah. Zato sta dva Toyotina inženirja združila prednosti množične proizvodnje (hitrost, nizki stroški na enoto) s prednostmi ročne proizvodnje (fleksibilnost in visoka kakovost) in na tej osnovi zasnovala nov proizvodni koncept – imenovan vitki. Končno so bili omogočeni ogromna produktivnost, visoki standardi kakovosti in sposobnost fleksibilnega prilagajanja spreminjajočim se zahtevam strank.
Elementi vitke proizvodnje so do danes dokazali svojo vrednost in so sinonim za učinkovit in sodoben pretok materialov v industrijski proizvodnji.
Ustrezni izrazi iz vitke proizvodnje so zdaj tudi trdno zasidrani v kulturi številnih podjetij. Muda rečemo, ko govorimo o preprečevanju dejavnosti, ki nimajo dodane vrednosti, muri, ko govorimo o preprečevanju preobremenitve opreme in upravljavcev, mura pa, ko govorimo o preprečevanju neenakosti.
Muda
Dejavnosti, ki ne dodajajo vrednosti, vendar porabljajo prostor, trud/denar ali čas, ne da bi povečale vrednost izdelka.
Muda razlikuje med sedmimi vrstami odpadkov:
1. Transport je v bistvu pomožni proces, ker je treba obdelovance, material in orodja neizogibno prevažati skozi proizvodni oddelek.
2. Zaloge v obliki materiala ali vmesnih ali končnih izdelkov. Prikriva težave v proizvodnji, saj se domneva, da je njegov obstoj namenjen kompenzaciji neustrezne zanesljivosti dostave, visokih stopenj zavrnitve, slabo usklajenih procesov ali okvar strojev.
3. Gibanje pri izvajanju postopkov, kot je nepotrebno rokovanje, iskanje ali čas, porabljen za pridobivanje materiala in orodij iz območij, ki so oddaljena od delovne postaje. To je posledica neučinkovite zasnove delovne postaje in lahko povzroči napake v kakovosti ali celo nesreče pri delu.
4. Obdobja čakanja, v smislu praznih in prostih časov, v katerih ni nobene dodane vrednosti.
5. Prevelika proizvodnja, ker se proizvede več, kot si kupec želi.
6. Nepotrebni procesni koraki, kar pomeni procese ali tehnologijo, ki so po nepotrebnem zapleteni za proizvodnjo končnega izdelka.
7. Napake, saj lahko izničijo dosedanjo dodano vrednost izdelku in zahtevajo sredstva za morebitno predelavo, ki sicer ne bi bila potrebna.
Muri
Muri pomeni preobremenitev ljudi in strojev čez naravno mejo. Posledica tega je slabo delovno ozračje, težave s kakovostjo in nesreče ali mehanske preobremenitve in okvare strojev.
Mura
Mura opisuje neenakomerno izkoriščenost ljudi in strojev. To je posledica nepravilnih proizvodnih načrtov zaradi nihanj v prodaji, različnih procesnih časov ali delovnih nalog ali nihanja obsega proizvodnje zaradi izpadov strojev in manjkajočih delov.
Upoštevajte, da je mura tudi vzrok za muda in muri: ni ustvarjenih dovolj dejavnosti, ki dodajajo vrednost (muda), če so stroji, zaposleni in material kljub nizki izkoriščenosti zmogljivosti vedno pri roki, medtem ko bo izkoriščenost zmogljivosti, ki je višja od povprečja, povzročila preobremenitev – muri.
Zlasti pri mudi in ob upoštevanju gibanja pri izvajanju procesov ter posebej pri potrebi po preprečevanju nepotrebnega ravnanja, iskanja in časa, porabljenega za pridobivanje materiala in orodij, je jasno, da samosvoja nabava sabotira vitko upravljanje, kar pomeni, da se ji je treba v vsakem primeru izogniti.
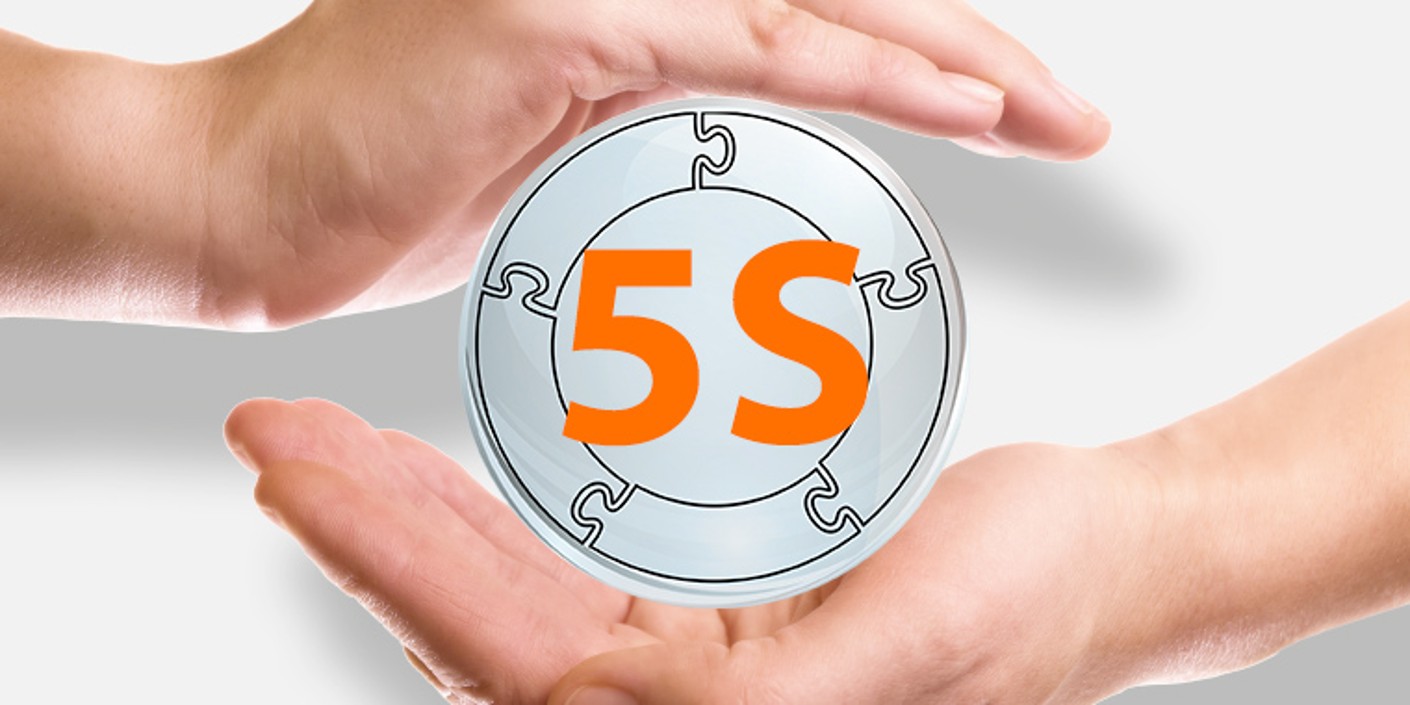
Začetna možnost za premagovanje teh težav je tako imenovana metodologija 5S, ki pomaga oblikovati delovne postaje tako, da se odpravijo odpadki. Prednost tega je večja učinkovitost. Poleg tega ta metoda zagotavlja jasen pregled in zagotavlja urejeno delovno postajo ter spodbuja uporabo definiranih delovnih rutin.
Ta pristop zagotavlja, da so procesi ponovljivi, izboljšana pa je tudi kakovost. Zaposleni so manj pod stresom, ker jim ni treba iskati orodja. Vaši zaposleni so motivirani, da sami še naprej optimizirajo delovno okolje in imajo koristi od sproščenega ustvarjalnega potenciala. Strukturirane, varne in ergonomske delovne postaje prav tako zmanjšajo izpade.
Ozadje: Ni presenetljivo, da tudi metodologija 5S prihaja z Japonske. Ideja je sistematičen pristop k oblikovanju delovnega okolja, tako da se lahko zaposleni osredotočijo na dejavnosti, ki dodajajo vrednost, hkrati pa odpravljajo odpadke – tako kot pri muda.
Kako vam bo pet preprostih načel pomagalo dodati več vrednosti:
Motivirajte svoje delavce, da ta načela udejanjajo v vsakdanjem delovnem življenju. Bodite dober zgled v svoji vlogi generalnega direktorja, nabavnega referenta in glavnega tehnika.
Bodite pogumni in izberite le najnujnejše. Zaposleni, ki odstranijo vse nepotrebno, ustvarjajo prostor za učinkovitost in ustvarjalnost. Katera orodja se nam podvajajo? Katera so neuporabna ali že močno obrabljena? Preglejte delovno mizo tudi za predmete, ki tam ne bi smeli biti, na primer revije.
Pospravite vse na svojem delovnem področju in ustvarite osnovno raven reda. Opustite opremo, ki jo uporabljate le redko. Vredno je razmisliti, kako razporediti stvari na delovni mizi: kaj potrebujete ves čas, vsako uro, dnevno ali samo tedensko ali celo mesečno? Vsakemu predmetu dodelite določeno mesto, tako da ga lahko najde kadar koli in kdorkoli.
Vzdržujte čistočo. V mnogih primerih je že to pol uspeha. Določite potrebne cikle čiščenja in jih zabeležite. Vzdrževanje čiste in urejene delovne mize prinaša številne prednosti: morebitne napake, ugotovljene na orodjih, se takoj odpravijo s čiščenjem ali zamenjavo, ob obisku strank pa pustite pozitiven vtis.
Standardizirajte stvari. Zabeležite rezultate metodologije 5S in jih uporabite za ustvarjanje standardov, ki jih lahko uporabljajo vse tehnične discipline. Redne revizije in akcijski načrti vam bodo olajšali uvedbo in vzpostavitev teh standardov.
Motivirajte svoje osebje, da ostane disciplinirano in redno preverja, ali vsi zaposleni izpolnjujejo standarde. Za to določite cikle in vpeljite spremljanje. To vam bo omogočilo postopno izboljšanje proizvodnih delovnih postaj na ravni celotnega podjetja.