Štíhlý přístup k logistice nákupů zvyšuje transparentnost a zvyšuje výnosy.
Celkový obrázek: počátky štíhlého řízení
Termín „štíhlá výroba“ pochází ze studie Massachusettského technologického institutu (MIT) nazvané „The Machine That Changed The World: The Story of Lean Production” (v překladu: „Stroj, který změnil svět: Příběh štíhlé výroby“.
Tehdy vědci analyzovali všechny výrobní systémy japonských výrobců automobilů vyvinuté na základě výrobního modelu společnosti Toyota, známého jako Toyota Production System (TPS). Samotný model TPS vznikl v 50. letech minulého století v důsledku krize japonské automobilky Toyota zapříčiněnou očekáváním trhů ve vztahu ke stále širší nabídce vozidel v malých objemech. Dva inženýři společnosti Toyota proto spojili výhody hromadné výroby (rychlost, nízké jednotkové náklady) s výhodami ruční výroby (flexibilita a vysoká kvalita) a na tomto základě navrhli nový výrobní koncept, který označili jako štíhlý. Tento model umožnil společnosti enormní zvýšení produktivity, zajištění vysokých standardů kvality a schopnost flexibilně se přizpůsobit měnícím se požadavkům zákazníků.
Prvky štíhlé výroby se osvědčily a dodnes jsou synonymem pro efektivní a moderní materiálový tok v průmyslové výrobě.
Příslušné termíny ze štíhlé výroby jsou dnes již pevně ukotveny v kultuře mnoha společností. Říkáme Muda, když mluvíme o prevenci činností, které nepřidávají žádnou hodnotu, Muri, když mluvíme o přetěžování zařízení a obsluhy, a Mura, když mluvíme o předcházení nevyrovnanosti ve výrobě.

Muda
Činnosti, které nijak nepřidávají hodnotu, ale spotřebovávají prostor, úsilí/peníze nebo čas, aniž by zvyšovaly hodnotu výsledného produktu.
Muda rozlišuje sedm druhů odpadu:
1. Přeprava je v zásadě doplňkový proces, protože obrobky, materiál a nástroje musí být nevyhnutelně přepravovány napříč výrobním oddělením.
2. Zásoby ve formě materiálu nebo polotovarů nebo hotových výrobků. Maskují problémy ve výrobě, protože se předpokládá, že jejich existence má kompenzovat nedostatečnou spolehlivost dodávek, vysokou zmetkovitost, špatně koordinované procesy nebo poruchy strojů.
3. Pohyb při provádění procesů, jako je zbytečná manipulace, hledání nebo čas strávený získáváním materiálu a nástrojů z oblastí vzdálených od pracovních stanic. Důvodem je neefektivní design pracovní stanice, který může mít za následek závady v kvalitě nebo dokonce pracovní úrazy.
4. Období strávená čekáním ve smyslu prázdných časů a prostojů, během kterých není vytvářena žádná přidaná hodnota.
5. Nadprodukce, což znamená, že se vyrábí více, než si zákazník přeje.
6. Zbytečné kroky v procesu zpracování, tedy procesy nebo technologie, které jsou zbytečně složité pro výrobu konečného produktu.
7. Vady, protože mohou negovat dosud přidanou hodnotu produktu a vyžadovat zdroje pro případné přepracování, které by jinak nebylo potřeba.
Muri
Muri znamená přetěžování lidí a strojů nad přirozenou či únosnou hranici. Takové přetěžování má za následek špatné pracovní prostředí, problémy s kvalitou a nehody nebo mechanické přetížení a poruchy strojů.
Mura
Mura označuje nerovnoměrné vytížení lidí a strojů. To je způsobeno nepravidelnými výrobními plány v důsledku kolísání tržeb, měnícími se dobami procesů nebo pracovních úkolů nebo kolísajícími objemy výroby v důsledku prostojů strojů a chybějících dílů.
Je důležité si uvědomit, že Mura je současně příčinou Muda a Muri: není možné vytvářet dostatek činností s přidanou hodnotou (Muda), pokud jsou stroje, zaměstnanci a materiál drženy po ruce navzdory nízkému využití kapacity, zatímco vyšší než průměrné využití kapacity povede k přetížení zdrojů – Muri.
Zejména v rámci konceptu Muda a při zvažování pohybu při provádění procesů, konkrétně nutnosti předcházet zbytečné manipulaci, hledání a času strávenému získáváním materiálu a nástrojů, je zřejmé, že nepravidelné nákupy sabotují štíhlé řízení, což znamená, že je třeba se jim bezpodmínečně vyhnout.
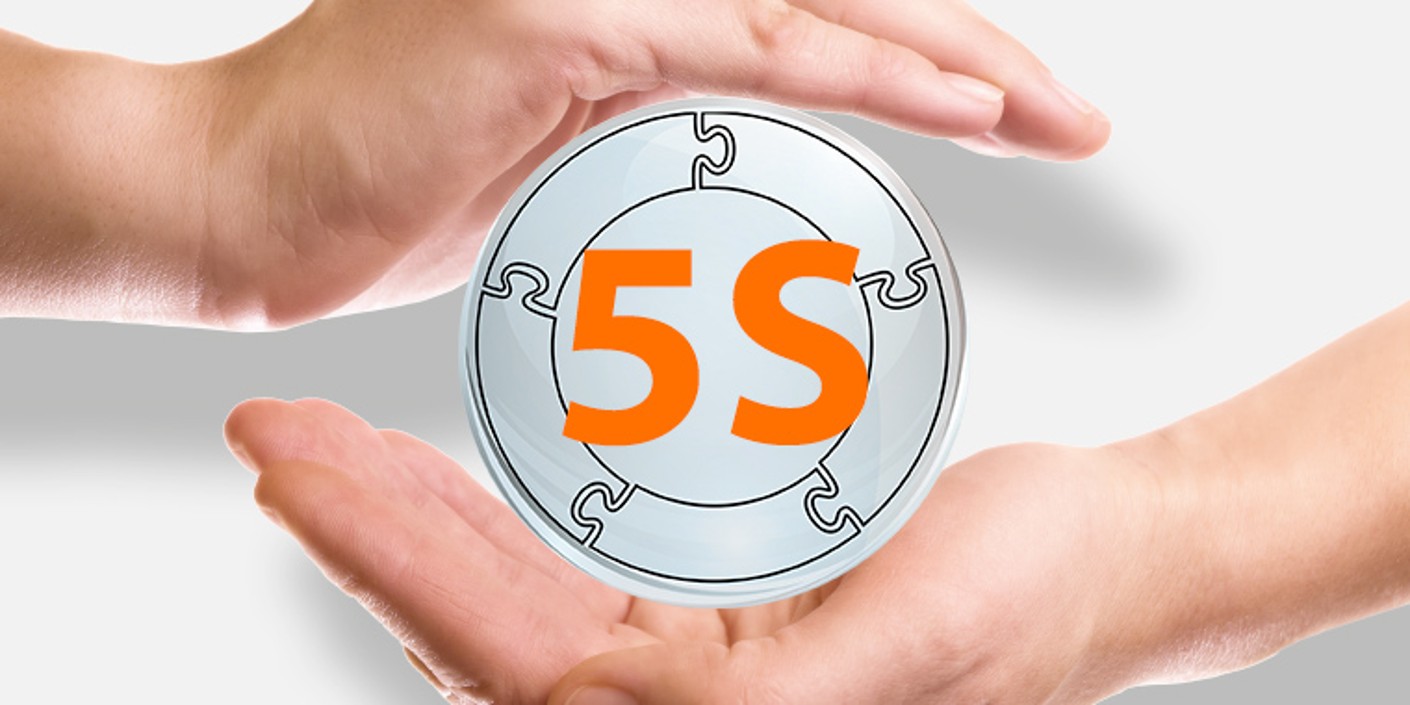
Prvotní možností, jak tyto problémy překonat, je tzv. metodika 5S, která pomáhá s navržením pracoviště tak, aby nedocházelo k plýtvání. Výhodou je vyšší účinnost. Tato metoda navíc nabízí jasný přehled, zajišťuje uspořádanou pracovní stanici a podporuje používání definovaných pracovních postupů.
Tento přístup zaručuje reprodukovatelnost procesů a také zlepšuje kvalitu. Zaměstnanci jsou méně vystresovaní, protože nemusí shánět nástroje. Vaši pracovníci jsou tak motivováni k tomu, aby nadále sami optimalizovali pracovní prostředí okolo sebe a těžili z dostupného potenciálu. Strukturované, bezpečné a ergonomické pracovní stanice navíc snižují prostoje.
Podkladové informace: Není překvapením, že také metodika 5S pochází z Japonska. Cílem je zaujmout systematický přístup k navržení pracovního prostředí, aby se pracovníci mohli soustředit na činnosti, které přidávají hodnotu a zároveň eliminují plýtvání – stejně jako Muda.
Jak vám pět jednoduchých zásad pomůže s přidanou hodnotou:
Motivujte své pracovníky, aby tyto principy uplatňovali ve svém každodenním pracovním životě. Jděte příkladem ve své roli jednatele společnosti, pracovníka nákupního oddělení a hlavního technika.
Mějte odvahu vybrat jen to nejnutnější. Pracovníci, kteří odstraňují cokoli nepotřebného, tím zároveň vytvářejí prostor pro efektivitu a kreativitu. Jakých nástrojů máme více, než je potřeba? Které z nich jsou nepoužitelné nebo již hodně opotřebované? Zkontrolujte také, zda se na pracovním stole nenachází věci, které by tam neměly být, například časopisy.
Roztřiďte všechny předměty ve své pracovní oblasti a vytvořte určitou úroveň pořádku. Zbavte se vybavení, které používáte jen zřídka. Stojí za to zvážit, jak si uspořádat věci na pracovním stole: co potřebujete neustále, každou hodinu, denně nebo jen jednou týdně nebo dokonce jednou měsíčně? Každé položce přiřaďte pevné místo, aby ji mohl kdykoli kdokoli najít.
Udržujte čistotu. V mnoha případech je čistota sama o sobě polovina úspěchu. Určete potřebné cykly čištění a zaznamenávejte je. Udržování čistého a uklizeného pracovního prostředí přináší řadu výhod: veškeré závady zjištěné na nářadí lze okamžitě odstranit čištěním nebo výměnou a při návštěvách zákazníků zanecháte pozitivní dojem.
Přistupte ke standardizaci. Zaznamenejte výsledky metodiky 5S a využijte je k vytvoření standardů použitelných všemi technickými obory. Pravidelné audity a akční plány vám usnadní zavádění a stanovení těchto standardů.
Motivujte své zaměstnance k disciplinovanosti a pravidelně ověřujte, zda všichni zaměstnanci dodržují normy. Za tímto účelem definujte cykly a stanovte potřebná opatření pro monitorování. To vám umožní postupně vylepšovat pracovní stanice ve výrobě na celopodnikové úrovni.