Meeting all the challenges of DEEP-hole drilling without problems
With the deep-hole drill GARANT Master Steel DEEP

Technical perfection meets creative innovation
GARANT Master Steel DEEP: The ultimate solution for deep-hole drilling GARANT Master Steel DEEP offers a multitude oftechnical highlights to meet all the challenges of DEEP-hole drilling without problems:
- Very high productivity.
- Maximum cost-efficiency.
- Extreme tool life.
- Very high process reliability and precision.
Deep-hole drilling - one of the biggest challenges in machining.
Deep-hole drilling usually starts from a machining depth of 16×D.The standard processes in the diameter range of 3 to 14 mm comprise:
- Single-lip drilling
- Double-lip drilling
- HSS drilling with tools to DIN 1869
- Solid carbide deep-hole drilling
Depending on the machining task a selection can be made due to the achievable various nominal diameters,length and diameter ratios, tolerances and surface qualities and the required productivity.
Basic challenges forsolid carbide deep-hole drilling
Deep-hole drilling generally involves large and expensive components.The demands placed on the tools for this production process are correspondingly high:
- Achieving the highest possible productivity due to high metal removal rates.
- Maximum cost-efficiency due to reduced machine time and long tool life -in particular regarding comparatively high tool costs.
- Ensuring the highest possible process reliability.
- Precision during machining in compliance with the required tolerances in respect of thedrilled hole, shape and position as well as the desired surface quality of the bore wall.
Specific tool requirements
Drilling at extreme depths leads to particularly intensive loads on the tool.Expensive and complex components also increase the difficulty and the risk of machining.For this reason, deep-hole drilling can be referred to as the “supreme discipline”of machining.
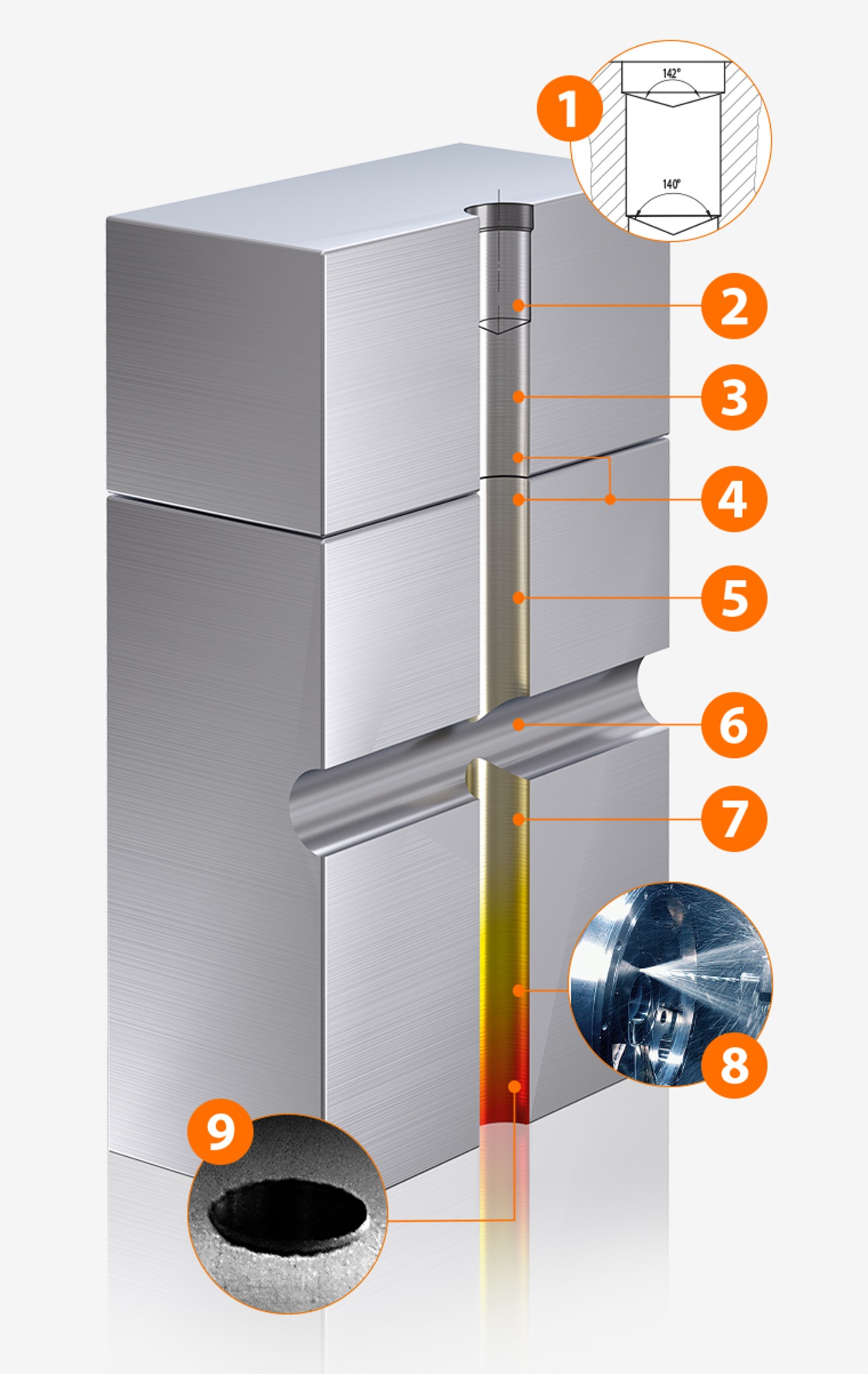
- 1. Centring / spot drilling
The centring and spot drilling allow the subsequenttool to be positioned precisely.This reduces lateral forces due to misalignment.
- 2. Pilot hole
The pilot drill generates the guidanceand the direction for the subsequenttool. Point angle and cutting edgetolerance are appropriate and areminimally larger than that of thedeep-hole drill.
- 3. Deep-hole drilling
The drilling process can be performedwithout problems due to the correctpreparation and use of a suitabledeep-hole drilling tool.
- 4. Drilling stacked items
Stacks made from different materials -where there may be intervals betweenthe individual components often posecritical and complex challengesto the tool and the designof the machining process.
- 5. Boring tolerances
Exact hole quality and compliance withthe tolerance limits.
- 6. Cross drilling
Cross holes require the tool to perform anadditional material exit and entryduring machining.
- 7. Chip evacuation
As the drilling depth increases, chip evacuation becomesmore challenging. It is however essential for aperfect drilling result and to prevent the tooljamming and breaking.
- 8. Cooling
As the hole depth increases, the generationof sufficient cooling in the machining zonebecomes more challenging. Insufficientvolumetric flow of coolant meansthe frictional heat isno longer sufficiently dissipated.
- 9. Drill exit
The drill exit places stresson the drill. In addition, burr formationoften occurs which requires additionalpost-processing operations.
GARANT Master Steel DEEP: The ultimate solution for deep-hole drilling
The new system offers unique advantages right across the board
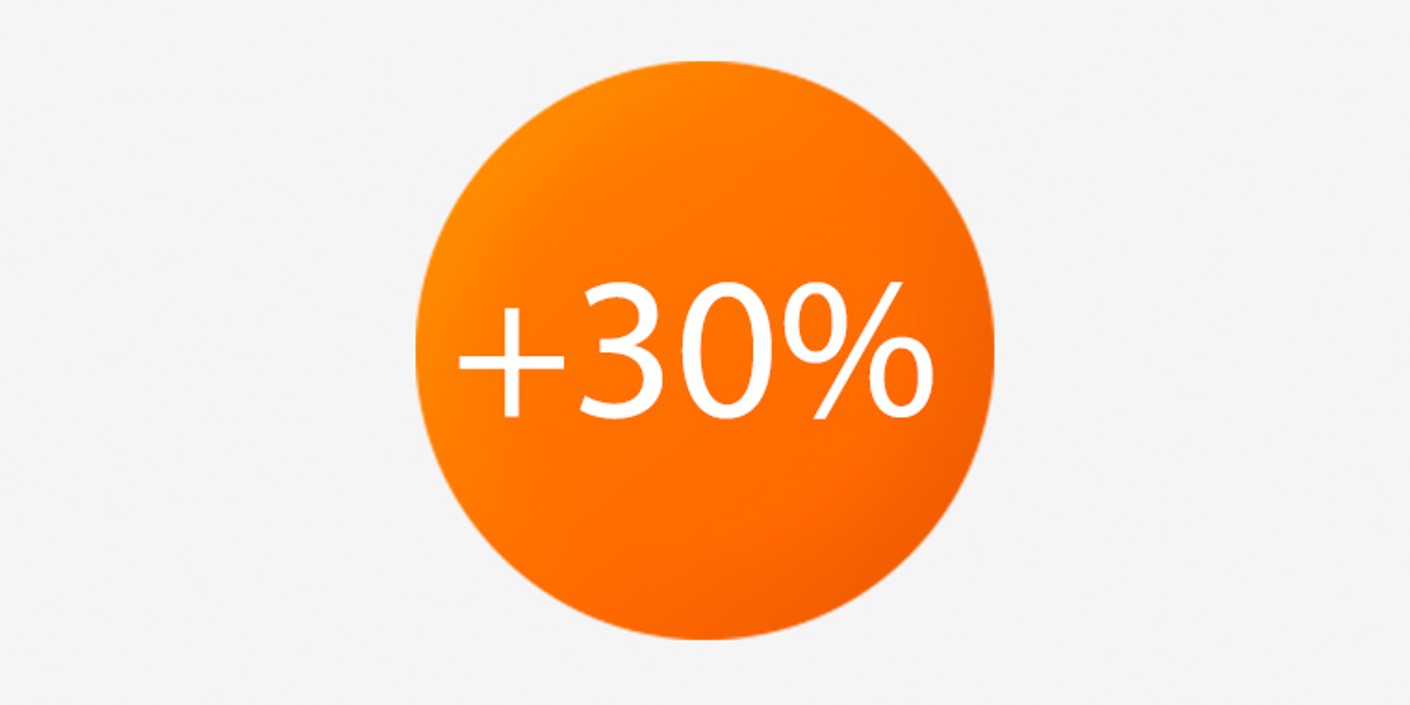
Up to 30% higher metalremoval rate
- Optimised point geometry with stable cutting edges and large flutes.
- Significantly increased cutting data in comparison to the predecessor product and to the competition.
- Extreme tool stability – even at high cutting data, thanks to the greatly strengthened corepaired with innovative shape of the coolant channels.
- High temperature-resistant TiAlN-based multi-layer coating andall-round cooling thanks to guide rings at the drill tip.
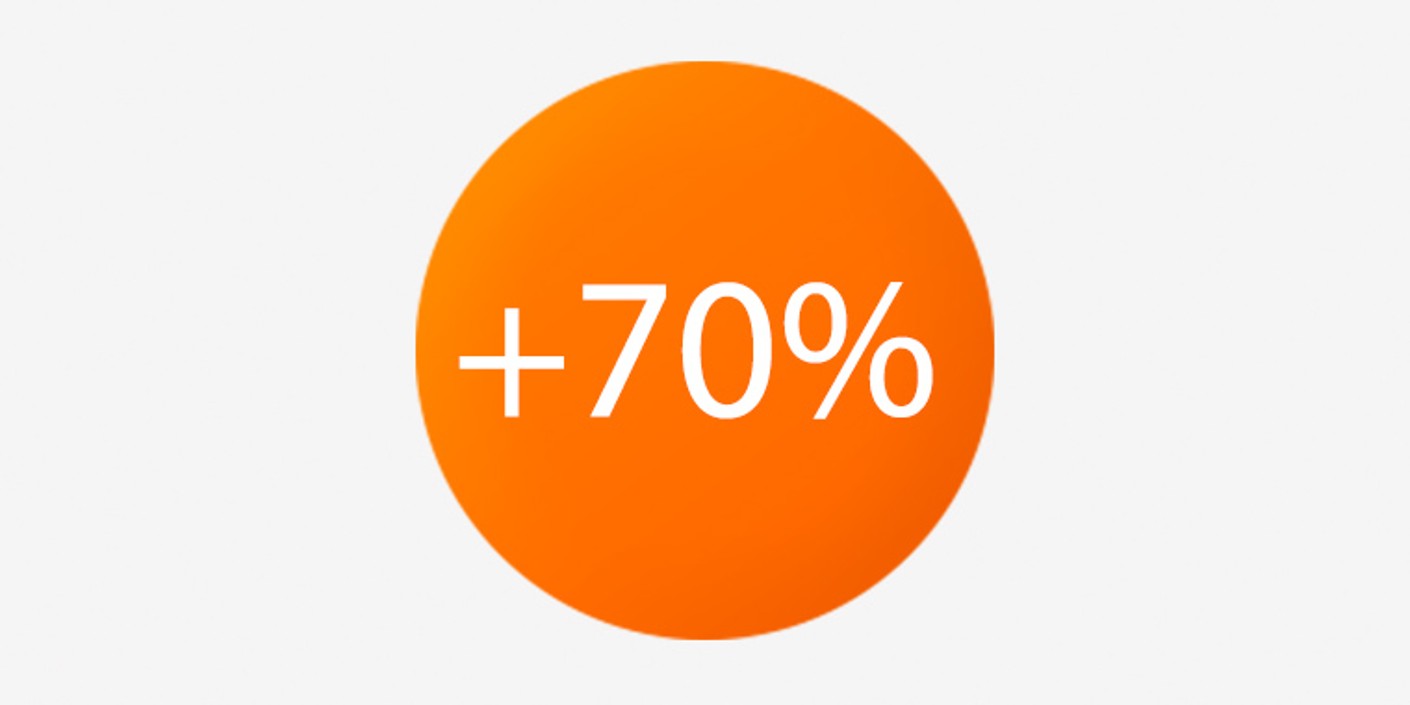
About 70% increased stability
- Improved point geometry to create an optimum chip-breakingbehaviour when using general-purpose materials in steels,stainless steel and also cast iron.
- Optimum evacuation of chips – even from extreme drillingdepths and at high metal removal rates, due to the unequalhelical pitch of the flutes, thereby drastically accelerating theevacuation of chips from the drill hole.
- Precise guidance by guide rings and additional guide chamferpermits very high drill hole quality.ɾɾ No co-pilot hole necessary – only asimple pilot hole.
- Multiple regrinding capability of the tool to thestandard of a new tool.ɾɾ Coated head and polished chip flutes for anoptimum flow of chips.
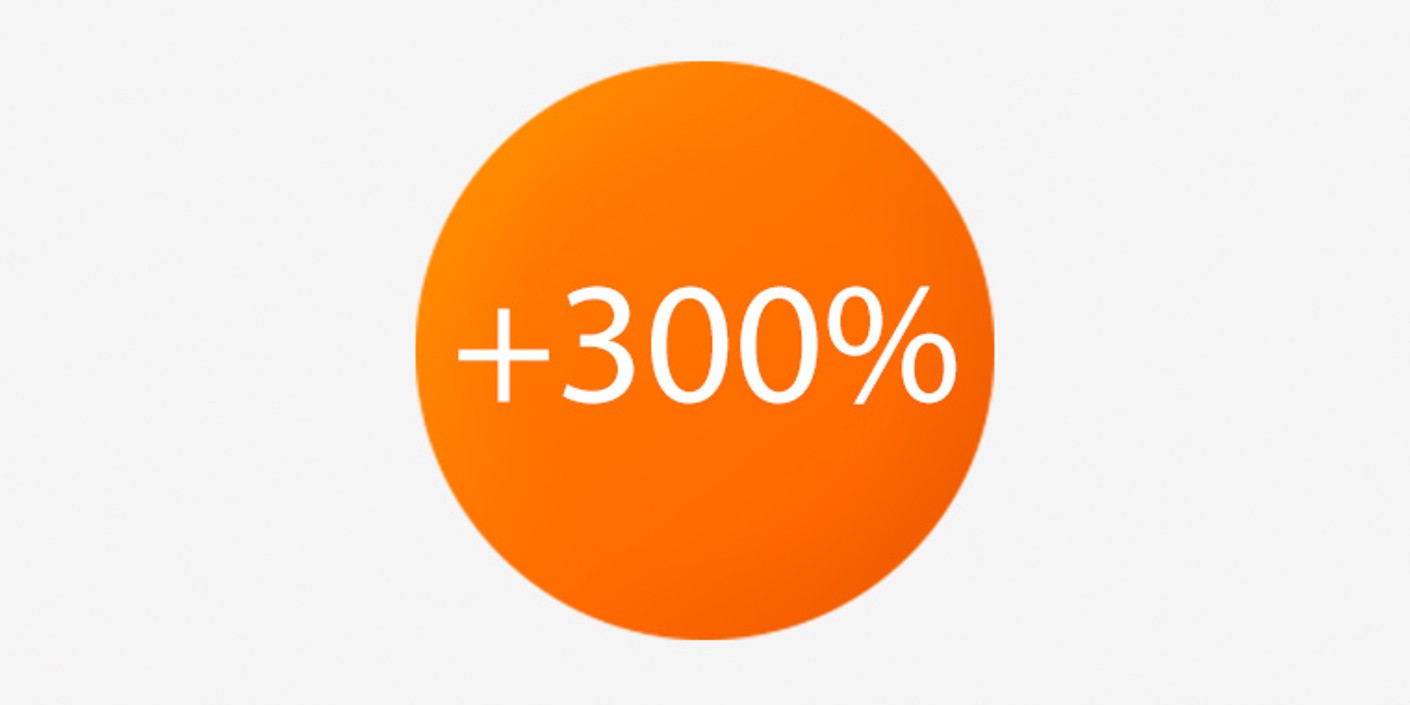
Up to 300% longer tool life
- Outstanding protection against tool breakage thanks tooptimised and innovative coolant channel design.
- Low-vibration running combined with increasedcutting data.
- Extremely wear-resistant and heat-resistantTiAlN-based multi-layer coating.
- Micrograin substrate of the latest generation.
Further Information
Read all about the GARANT deep-hole system for drillings up to 50xD here