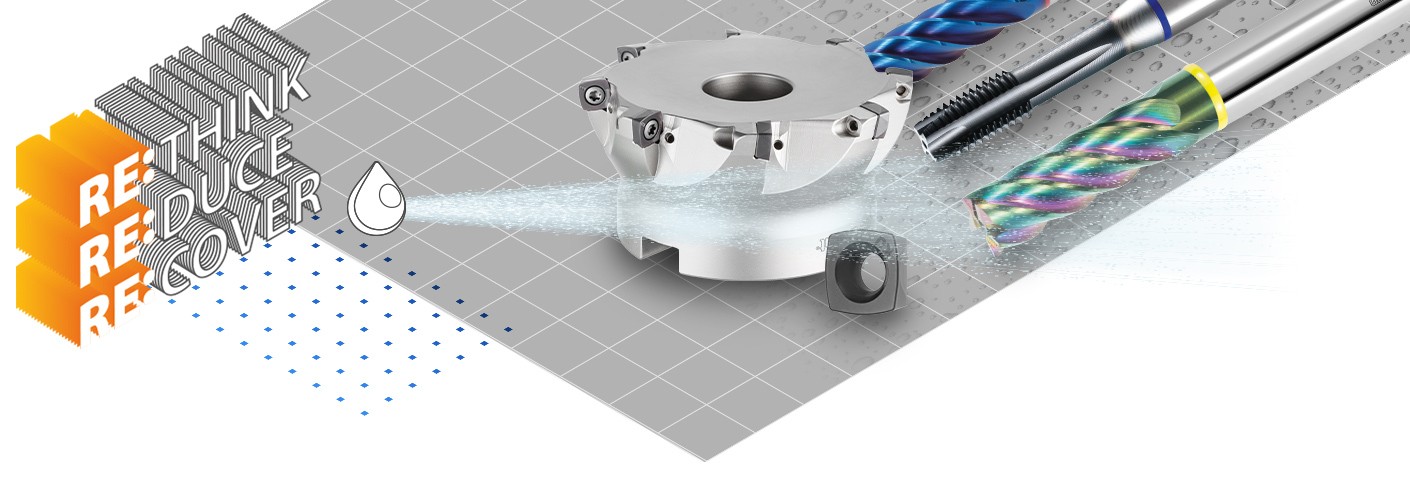
Reducing the use of cooling lubricants – minimum quantity lubrication and dry machining
Wet machining entails high costs
Whether it’s turning, drilling or milling – machining production methods are widespread and often found in the metalworking industry. One of their benefits is that they ensure very tight dimensional and shape tolerances. They enable customers to produce almost any geometric shape, and they are also highly automated, making them ideal for series production environments.
Extremely high temperatures are generated by the machining work in the cutting zone, so air/oil mixtures provide both cooling and lubrication and help to convey the chips away. In conventional wet machining applications, cooling lubricant flows around the tools. This often washes away bedway oils as well, exacerbating wear on the machine guides. Cooling lubricants also require a lot of maintenance, with the checks, disposal and topping up all incurring costs down the line.
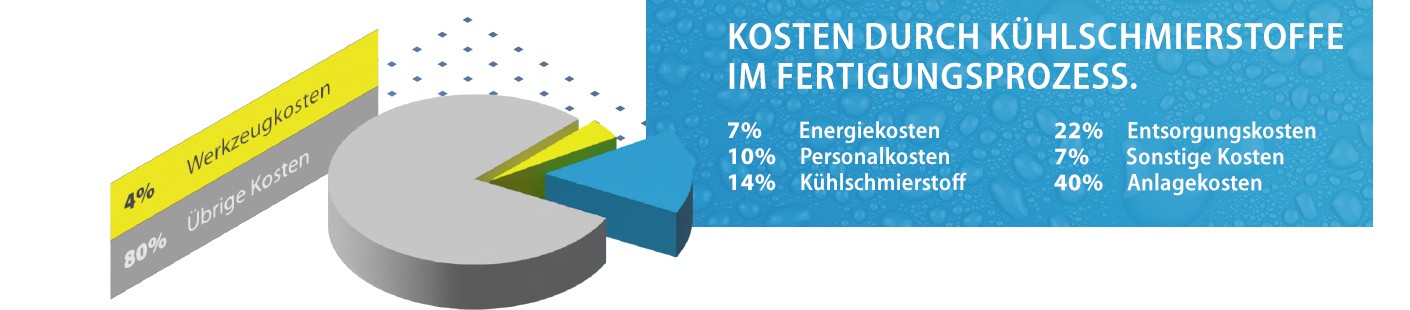
Whilst people have been looking for ways to reduce their use of cooling lubricant for some time now, the current energy crisis has really brought the issue to the fore. After all, the average costs of cooling lubricant in production processes amount to between 8 and 16 per cent! The exact cooling lubricant costs naturally depend heavily on the specific machining method being used and other production-specific factors like the size of the machine tools. Nevertheless, big cost savings can be made here, which shouldn’t be overlooked.
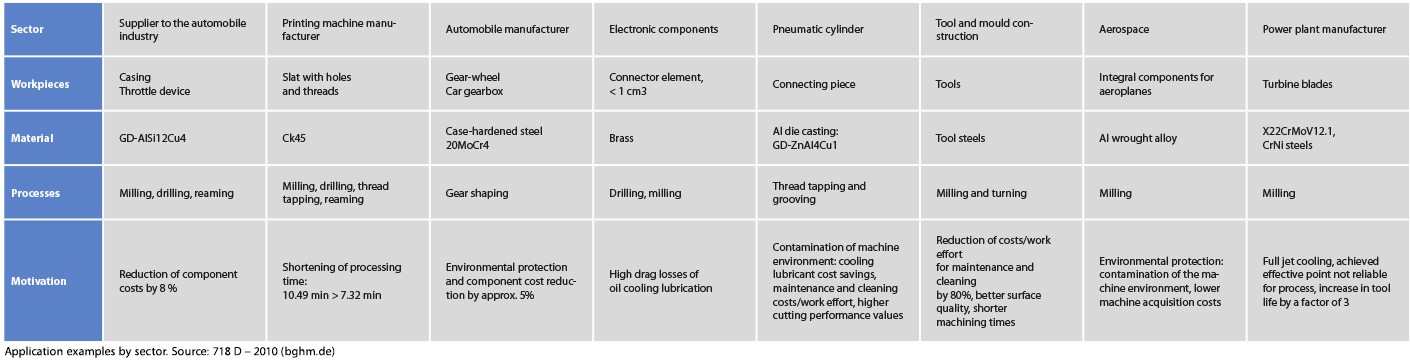
Alternatives to wet machining that use less cooling lubricant
Dry machining and minimum quantity lubrication (MQL) are alternatives to wet machining and we expect that many people will already be familiar with them. The main advantage offered by MQL is the costs saved for resources such as oil, water and energy. If you don’t need to dispose of and top up supplies like these as often, you won’t need to interrupt production as much.
What’s more, eliminating the full-jet cooling when cutting metal usually also eliminates the thermal shock on the tool cutting edge. This, in turn, enables the use of super-hard tool materials, opening the door to much higher cutting data and a longer tool life.
However, you must carefully consider if it would make sense to switch over to MQL or dry machining. It is not always a straightforward process, and could require high investments that will first need to be recouped. This overview is aimed at anyone looking to find out more about the opportunities and limits of MQL and dry machining. We always recommend obtaining advice from your supplier in order to assess your specific circumstances.
What is minimum quantity lubrication?
There is no standardised definition of minimum quantity lubrication. In contrast to flood lubrication, minimum quantity lubrication only uses a few drops of lubricant during machining. A special metering technique ensures that the pressurised medium is brought directly to the active point on the tool cutting edge. Practical experience has shown that, on average, MQL does not use more than 50 ml of lubricant per process hour and tool.
Dry machining or minimum quantity lubrication
The two terms “minimum quantity lubrication” and “dry machining” are not always clearly differentiated from one another. Indeed, MQL is often also called “quasi-dry machining”. This is because the term “dry machining” established itself several years before minimum quantity lubrication was introduced. Generally speaking it refers to dry chips, tools and components during the production process.
The key factor here is how the term “dry” is defined. A chip is considered to be “dry” if the percentage of cooling lubricant on the chip is less than 2 per cent by mass. In practice this means that 80 ml of cooling lubricant can be used per hour to obtain “dry” chips. As a result, MQL in fact falls under dry machining.
Moreover, “dry machining” also denotes methods that are absolutely dry, i.e. they do not use any cooling lubricant whatsoever. Where “dry machining” is referred to below, we’re referring to an absolutely dry method that does not use any cooling lubricant, otherwise minimum quantity lubrication is meant.
One thing is clear – if you want to ensure efficient dry machining, you need to be familiar with the ins and outs of how the workpiece, material, machining method, tool, machining conditions and machine tool all influence one another. The following table summarises where dry machining and minimum quantity lubrication have established themselves. It is no substitute for an on-site consultation that looks at your specific circumstances.
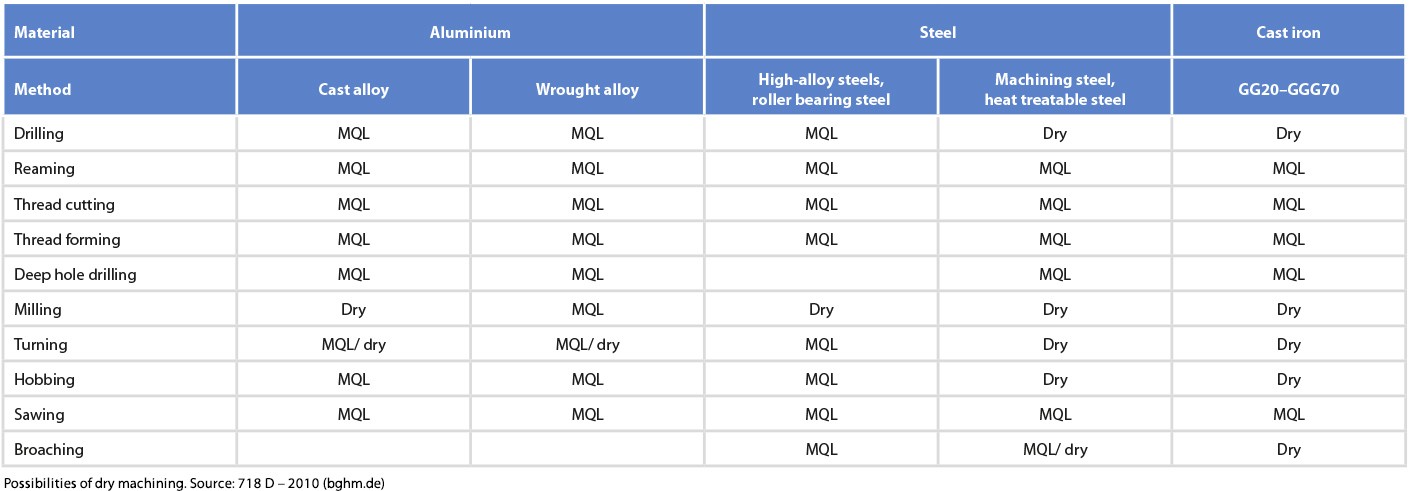
How difficult is it to switch over to minimum quantity lubrication?
Companies will be asking themselves: “How difficult is it to switch over to MQL?” and “When does it makes sense to do so?”. Unfortunately, there is no one-size-fits-all answer here. The changes required to machines and tools in order to use MQL vary greatly depending on the specific production conditions at the company. For example, machine tools such as circular and band saws are very easy to retrofit for use with MQL. However, this is not the case for High Performance Cutting – if you want to optimise these workflows for MQL, you will need specially designed machines and the appropriate tools. The decisive factor is how the lubricant is fed in.
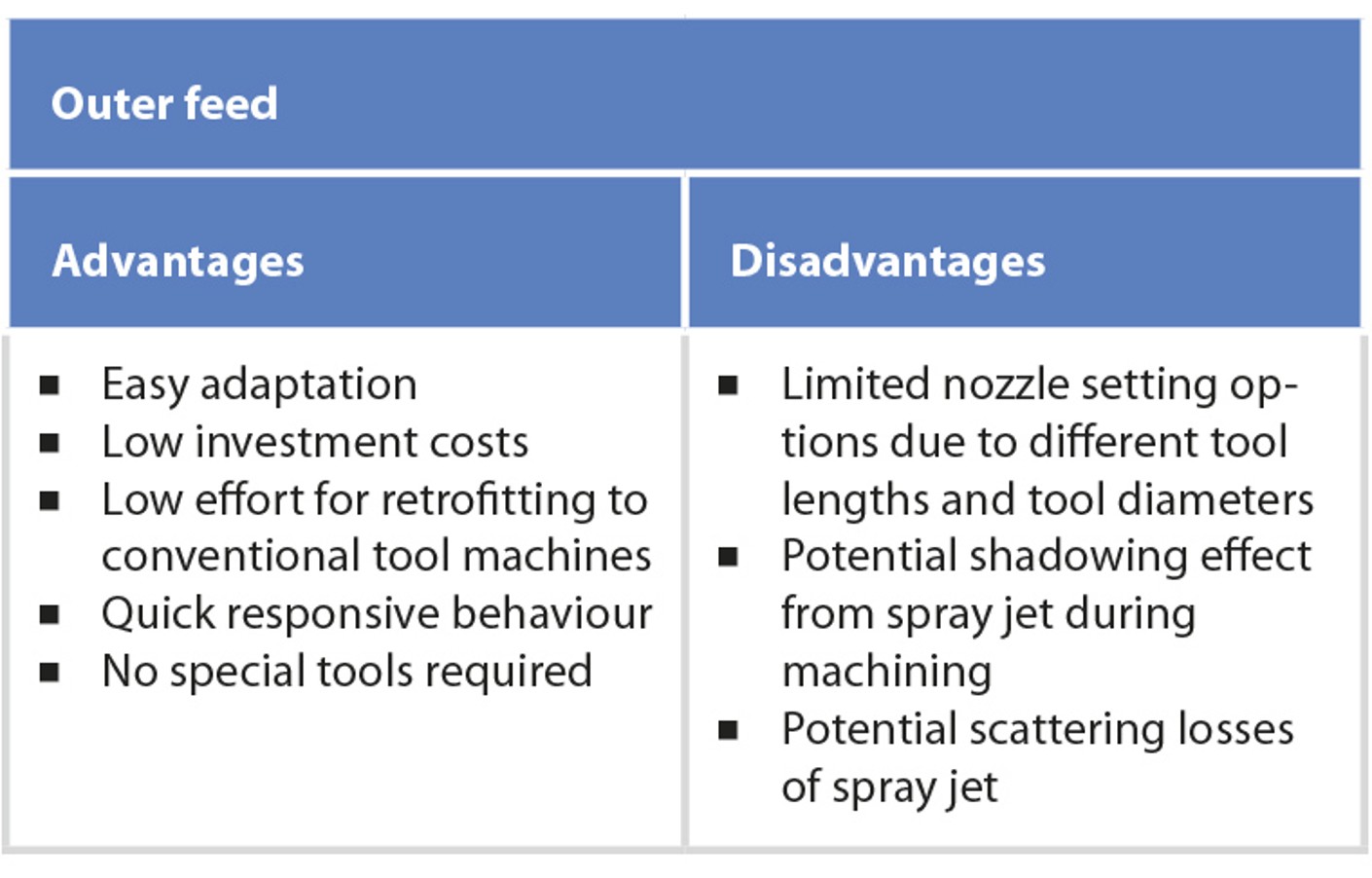
Systems where the minimum quantity lubrication is fed in externally
If an external feed is being used, the minimum quantity of lubricant is fed to the active point on the tool cutting edge by a nozzle installed in the machining space of the machine tool. An external feed is suitable for retrofitting machine tools and for use in standard processes like sawing, drilling, milling and turning. The spray nozzles required for this are very simple to attach to the spindle nose.
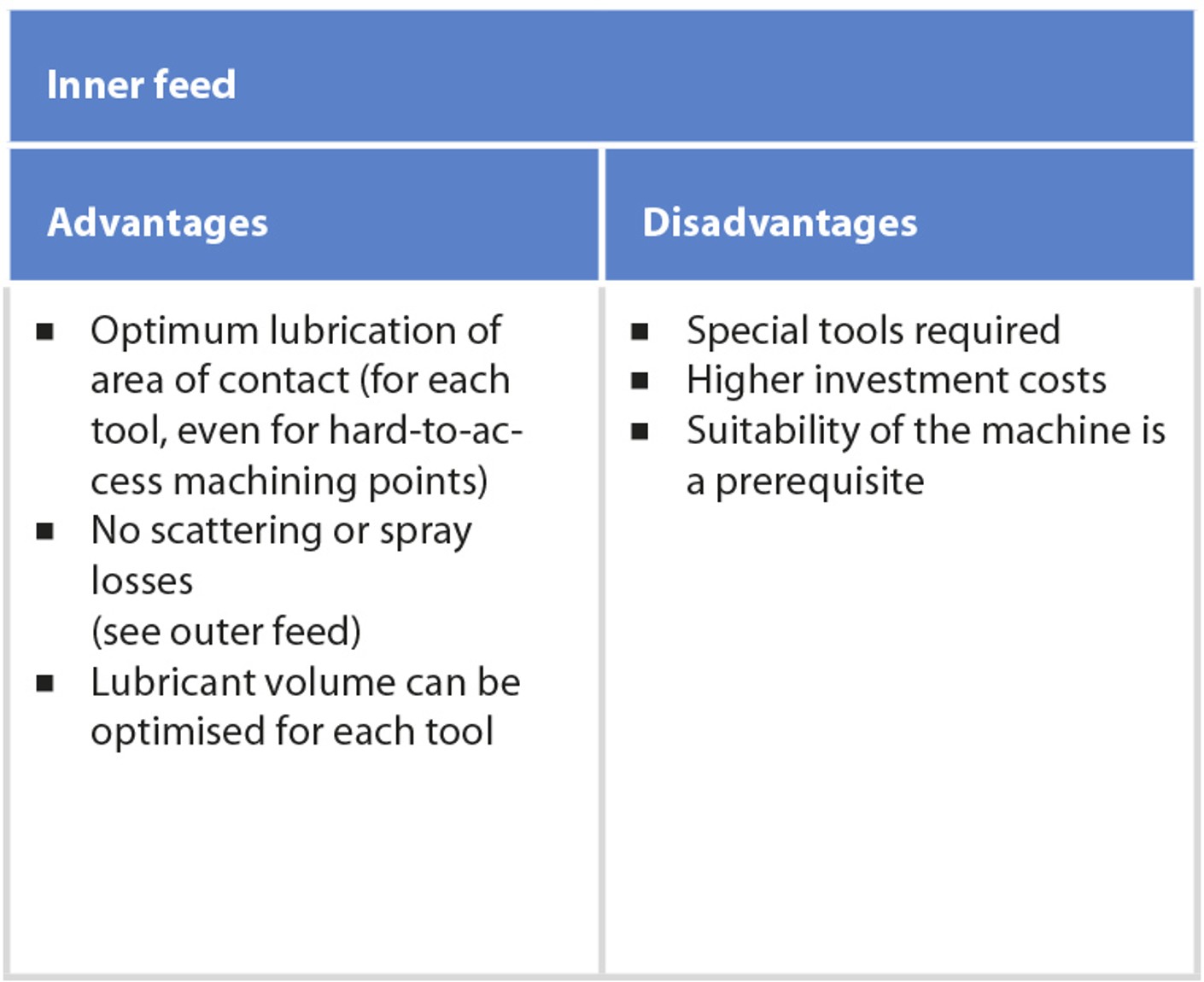
Systems where the minimum quantity lubrication is fed in internally
An internal feed is more complex, as it is conveyed through a working spindle directly to the cutting edge. It is used for more challenging processes as it enables the aerosol to be fed in particularly accurately – through the tool, directly to the active point on the tool cutting edge. Active agent is continuously supplied throughout the machining process, enabling very deep holes and very high cutting speeds. However, converting your machines to this system may entail high costs, so it is essential to obtain expert advice that is tailored to your circumstances.
Financial advantages at a glance
Reducing the use of cooling lubricant will save you money in various different ways. Naturally, these savings also depend heavily on the specific production parameters being used.
- A longer tool life can be expected thanks to optimised processes
- In individual cases, optimised processes can speed up the workflow by up to 30%
- Savings can be made when purchasing, storing, transporting and disposing of the cooling lubricant. The chips remain dry and can be sold, for example as recycling material
- The time and effort required to check and maintain the cooling lubricant are eliminated
- Depending on the specific application, time-consuming downstream processes can be reduced, such as cleaning the environment around the machinery
Environmental advantages at a glance
- No harmful waste emulsions are created
- There is no damage caused by large cooling lubricant leaks
- Safety at work: as the environment around the machinery is dry, the risk of accidents at the workplace is reduced
- Employees’ health is protected: the risk of illnesses (e.g. relating to the airways or skin diseases) attributable to cooling lubricants is prevented*
- It is also advantageous to switch over to MQL on machines that have relatively long downtimes lasting days or weeks. The “turning” of emulsion can be prevented. This can lead to microbial growth, an unpleasant odour and hazards to health
Possible disadvantages of minimum quantity lubrication
The advantages of MQL do not always outweigh the disadvantages. As previously mentioned, it depends heavily on the specific circumstances at the company, which is why customers must obtain bespoke advice. However, they should be aware of the following disadvantages:
- If the machines need to be converted, this will entail high investment costs
- The need for special tools (see next section) could result in higher ongoing tool costs
- Sometimes it is not worth switching over to minimum quantity lubrication for one-off jobs or small-series production runs. The time and effort required to coordinate the workpiece, machine parameters, tools and lubrication are often higher than the potential savings on offer
- Switching over to minimum quantity lubrication is not recommended for all methods, machines or workpieces
- MQL does not provide any cooling, it merely lubricates. The chips are conveyed away by compressed air. There is a risk of the component and tool overheating
MQL-compliant tool
Since machining processes that use minimum quantity lubrication work with extremely small amounts of lubricant, it is crucial to ensure a continuous supply to the active point on the tool cutting edge. Conventional tools used for wet machining quickly reach the limits of what they can do in this respect. Customised tools and the requisite expertise are needed here, particularly as the cutting speed increases.
Comment from source: 718 D (bghm.de)
*Comment from source: 718 D (bghm.de): in practice, metal cutting methods that use minimum quantity lubrication are considered to be low-emission methods. This trend can also be seen in tests that were conducted on workstations with minimum quantity lubrication as part of a special series of measurements. These tests measured the exposure (to dust, cooling lubricant aerosols and vapours) at machine tools used in Production departments. The data was acquired from meters worn by staff and from stationary measurements taken at the control panel and inside the machine (see images 40 and 41). Decomposition and pyrolysis products such as formaldehyde were only found in trace amounts in individual cases. The dust concentrations measured were also well below the permitted Occupational Exposure Limits (OELs) for “Respirable fraction” (OEL: 3 mg/m3 air) and for “Inhalable fraction” (10 mg/m3 air). The following reference measurement confirmed the tendency for minimum quantity lubrication to release much lower emissions than wet machining. When machining materials using minimum quantity lubrication on machine tools in Production departments, cooling lubricant vapours and aerosols were identified as factors that determine the level of exposure. All measurements identified that the previously valid air limit value for cooling lubricants was complied with (previous limit value: 10 mg/m3 air; state of the art). The concentrations measured in the work areas were so low that more than 95% of the measurement values were well below half the limit value