Keeping things in proportion: challenges in tool and mould making
As head of manufacturing and an experienced metalworker in tool and mould making, you must have observed the increase in the complexity of construction requirements and component shapes. Customers expect more from you than just precise fits and excellent surface quality. Other elements are equally important – your customers must be sure that they can reproduce perfect results at any time, while maintaining efficiency. Here, you can read key facts regarding the challenges you face in the tool and mould making industry. Get to know the most important materials and technical details, and stay up to date on preparatory work and the significance of the latest machining processes, such as Parabolic Performance Cutting (PPC) and deep hole drilling (TLB).
Several factors at work – getting a handle on every parameter
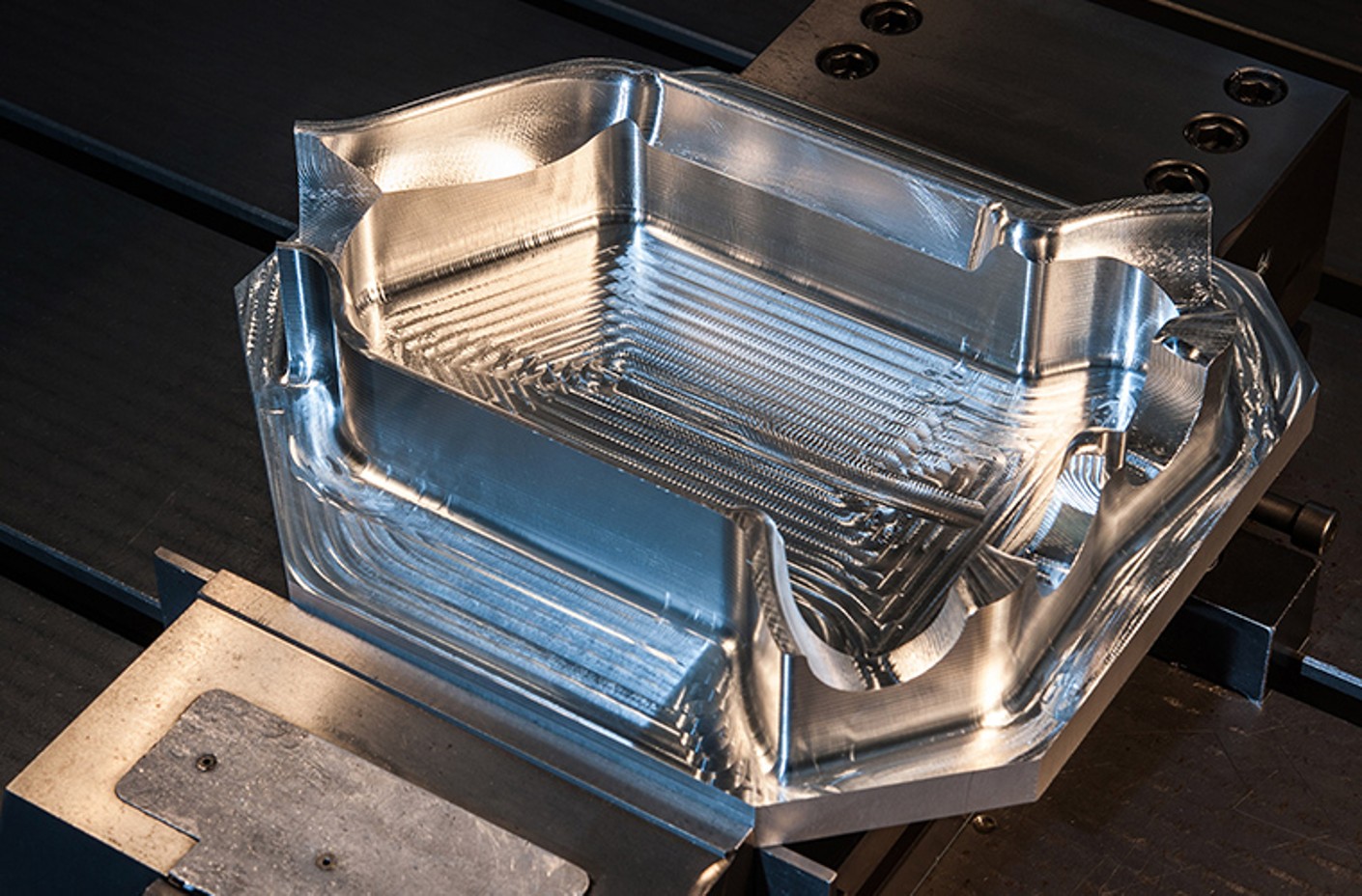
To ensure success at every step, you need two things for each phase. These are: the expertise to know which machining strategy best suits the customer’s needs, and a well-stocked range of high-quality tools with long tool lives. If you have these basic things in place, then your work will proceed with the same level of efficiency, regardless of whether you are working on tools, simple geometries, or highly complex 3D shapes – and irrespective of whether it involves hard or soft machining. Then you’ll be milling, drilling and clamping with confidence, and grinding with precision – right down to the micrometre.
By choosing the right tool, you can assure the following:
- Receive reliable cutting data
- Improve chip evacuation
- Extend tool life, leading to increased wear mark width
- Make best use of the cutting edge length in milling cutters
- Improve surface quality
- Reduce running times
- Standardise the display of measured values
Fix your workpieces firmly in place – we are always here to help
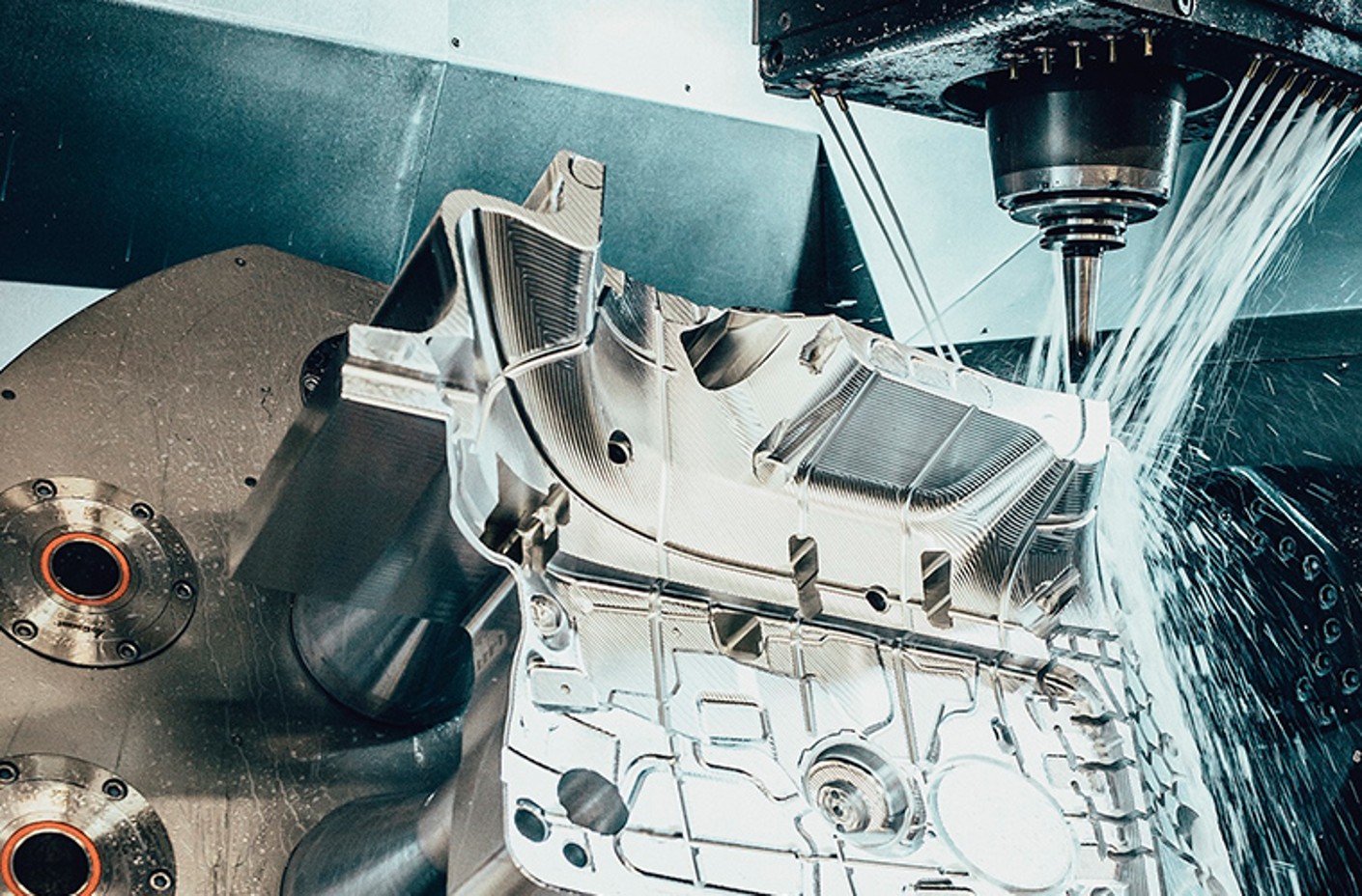
Standard components are great – as long as they meet what is required by the specific tasks in mould construction and tool manufacture. To achieve optimal force transfer, you must fix the blank or material to be worked on and the tool firmly in place. The biggest obstacle to overcome is complex tool geometry. It is often necessary to clamp and release the blank several times to guarantee the dimensional accuracy of the tool’s final shape at the end of the milling and drilling processes.
It does not matter whether you are working on multi-task machines such as milling and turning centres, tool clamping systems with polygon tapers, or hollow shank tapers with flat surface contact. The fewer tolerances your arbor has, the easier it will be to avoid angular errors and height errors.
The following arbors are available:
- ISO taper arbor
- Hollow shank taper arbor
- ISO taper arbors with flat surface contact/double-contact arbors
- MTM tool systems
- Tool clamping systems with polygon tapers
If you’re so inclined – arbors get the best results
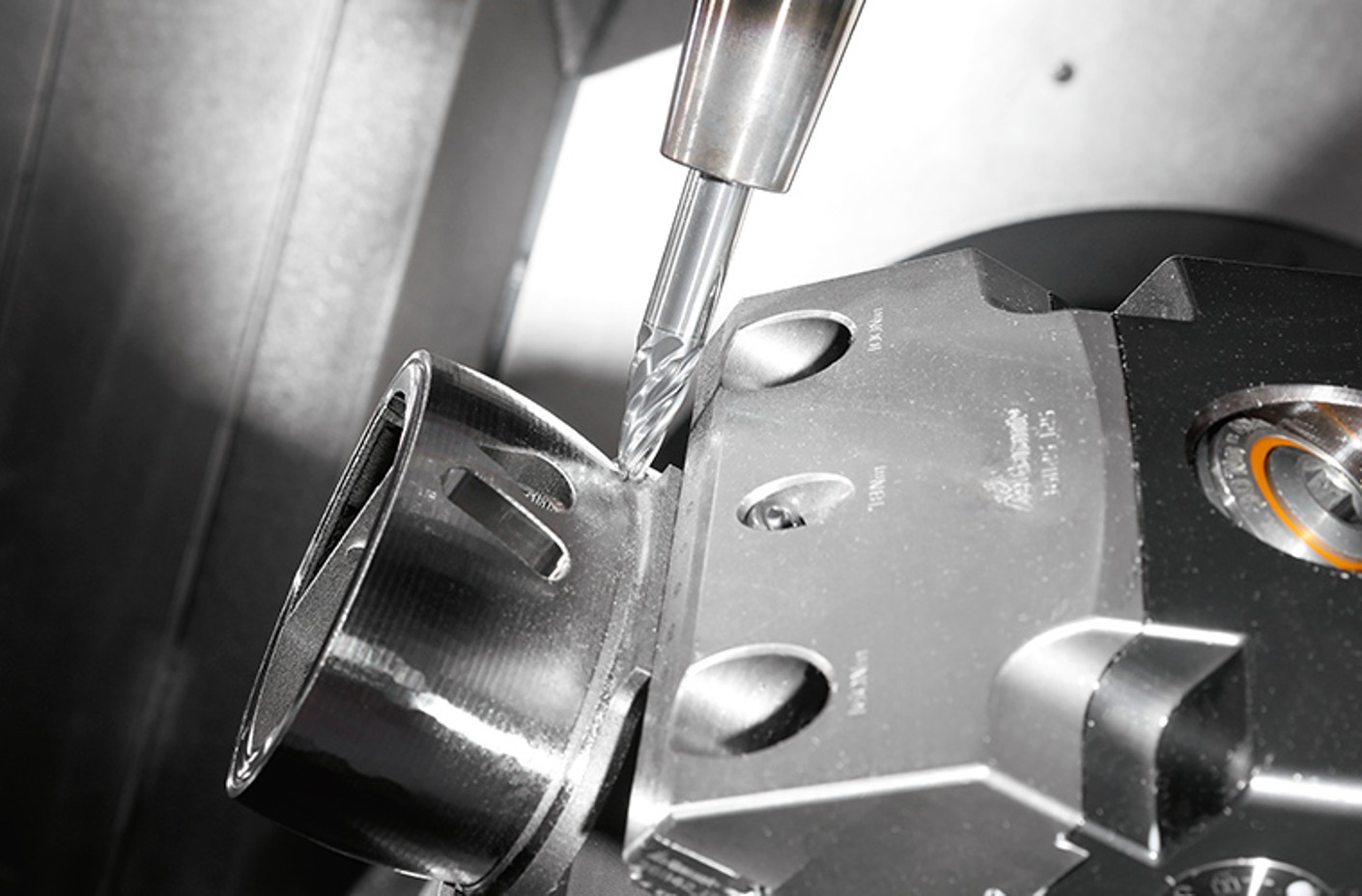
Even when you use side lock arbors, there is a way to improve the quality of your blank, and the time required for the processing. For example, if you are milling (roughing and finishing), then as an alternative to the side lock arbor with side flat (Weldon arbor), you can use a side lock arbor with inclined clamping flat (Whistle-Notch arbor), which will let you drill more precisely. This because in this situation, the loss of length due to the regrinding of the drill front can be corrected through axial length adjustment in the toolholder. If you have to perform difficult machining tasks (TPC milling), the Performance milling chuck is a perfect further development of the side lock arbor due to its pull-out protection and vibration damping, and is especially easy to use.
Alongside side lock arbors, there are the following further tool chucks:
- Hydraulic chuck
- Precision ER collet chuck Centro P
- Shrink-fit chucks
For work on relatively simple blanks, the following are suitable:
- Magnetic clamping technology
- Vacuum technology
- Zero point clamping
- Using a jig insert
Staying on top of things – clamping the blank
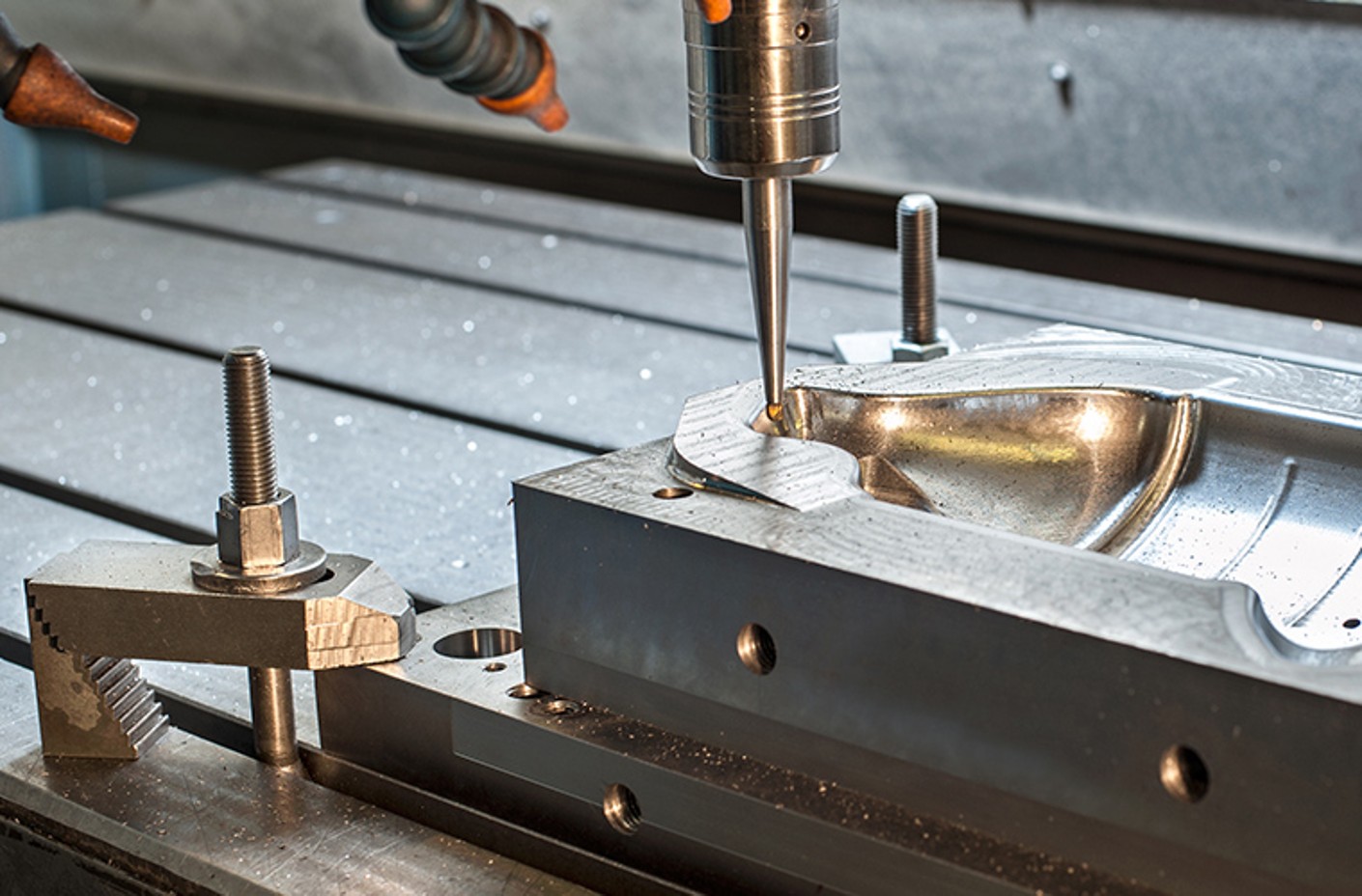
For work that permits direct clamping of the blank on the machine table, lateral toggle clamps or claw clamps are a good choice. If you work mainly on machining centres and milling machines, then high-pressure vices, centring vices and machine vices may be useful to you. When choosing the right technology for your business, always note the programming effort. The only way for you, as a master craftsperson in tool and mould making, to truly benefit is if the process and programming both proceed with equal efficiency.
If you would like to speed up your whole process, whilst taking into account all the clamping processes, our experts will explain all the technical options to you.
To receive advice
Not everything has to be hard – advice on your material
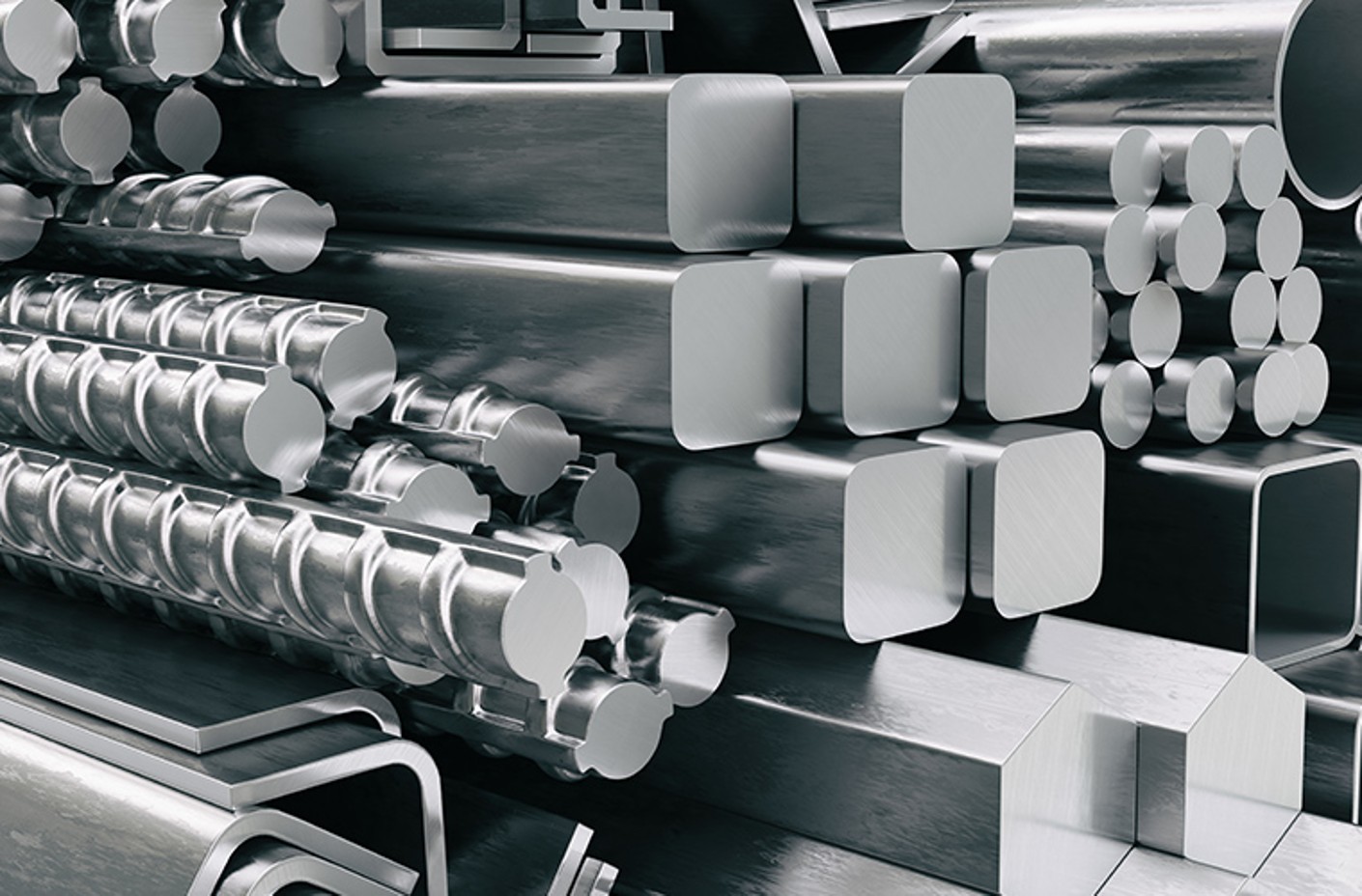
Steel is not just steel – check it closely!
In your work as a master craftsperson or specialist in tool and mould making, the most important things are:
- The alloy element in your steel
- The possibility of heat treatment
What you absolutely must know about steel in tool and mould making:
- Austenitic stainless steels: easy to machine.
- Super-austenite: extremely difficult to machine
- Ferritic stainless steels: have a tendency to stick, but are mechanically easy to work with
- Martensitic stainless steels: machining can vary depending on the pre-treatment (annealed or tempered)
- Austenitic-ferritic stainless steels (Duplex steel): extremely high tensile strength and heat-resistance, difficult to machine
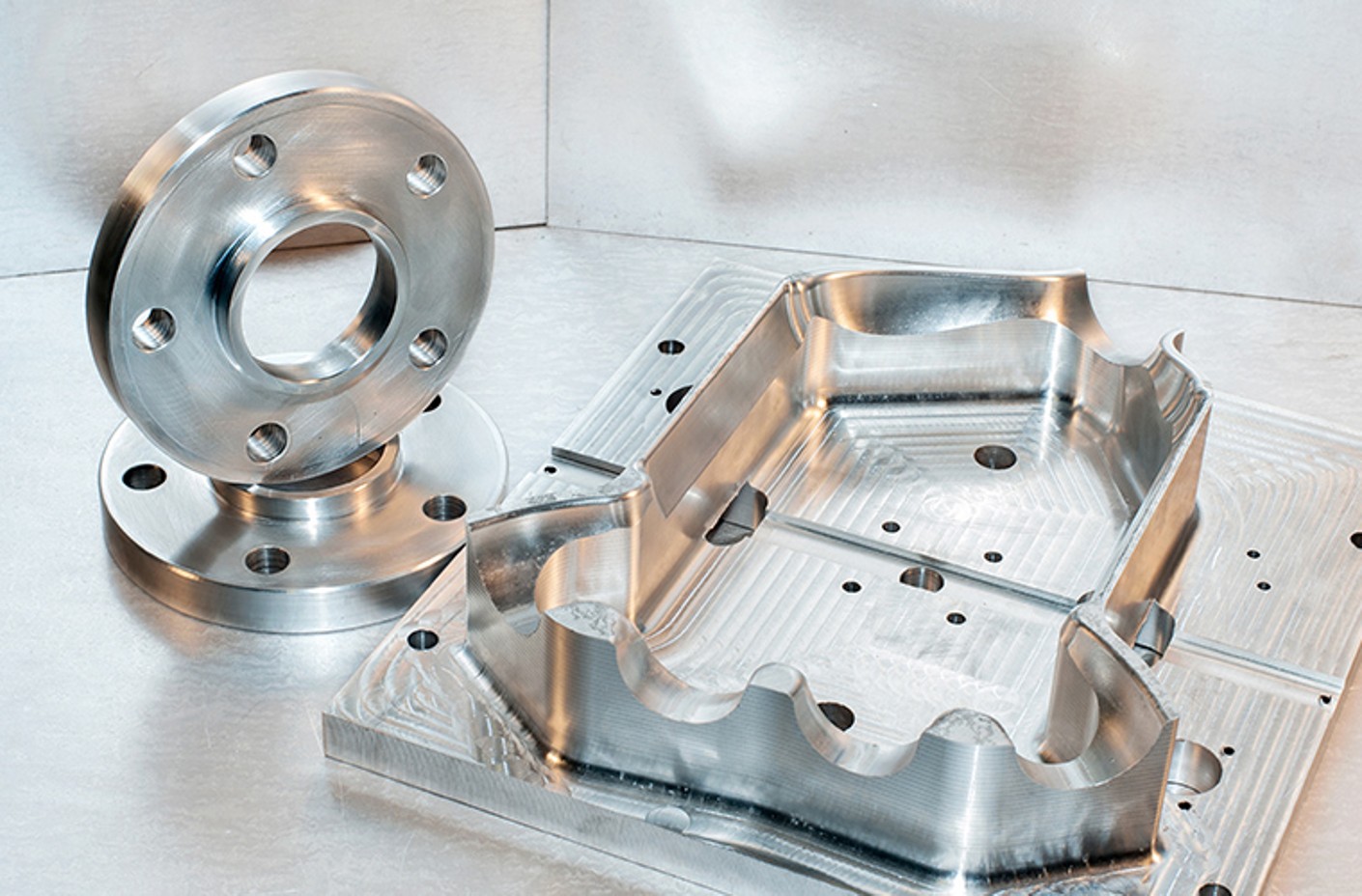
A lighter option – using aluminium or aluminium alloys
If it is an option for you, there is a lot going for aluminium. It is a light material which is generally easy to machine. Compared to steel of the same strength, with aluminium, you can benefit from more favourable cutting forces during your work. As an experienced metalworker, you know that the chip shape is important, due to the relatively large possible chip volume. The chip shape depends both on the material itself and on the cutting conditions and tool geometry. If you value long tool lives in your work process, then tools made of High Speed steels (HSS) and carbide are well-suited to machining wrought aluminium materials.
Important:
- Pure aluminium and hardenable wrought materials in the soft state tend to form spurious chips or built-up edges, particularly at low cutting speeds. This can result in poor surface quality.
- The cutting properties of aluminium cast materials without silicon are approximately the same as those of the corresponding wrought materials.
- Hardenable and hypoeutectic al-si cast alloys are harder to machine. This property increases with a higher silicon content. In this case, carbides are a good option.
- For hypereutectic al-si cast alloys, it is best to use carbides or polycristalline diamond tools. Important: the coarse silicon particles in the relatively hard basic structure significantly reduce the tool life.
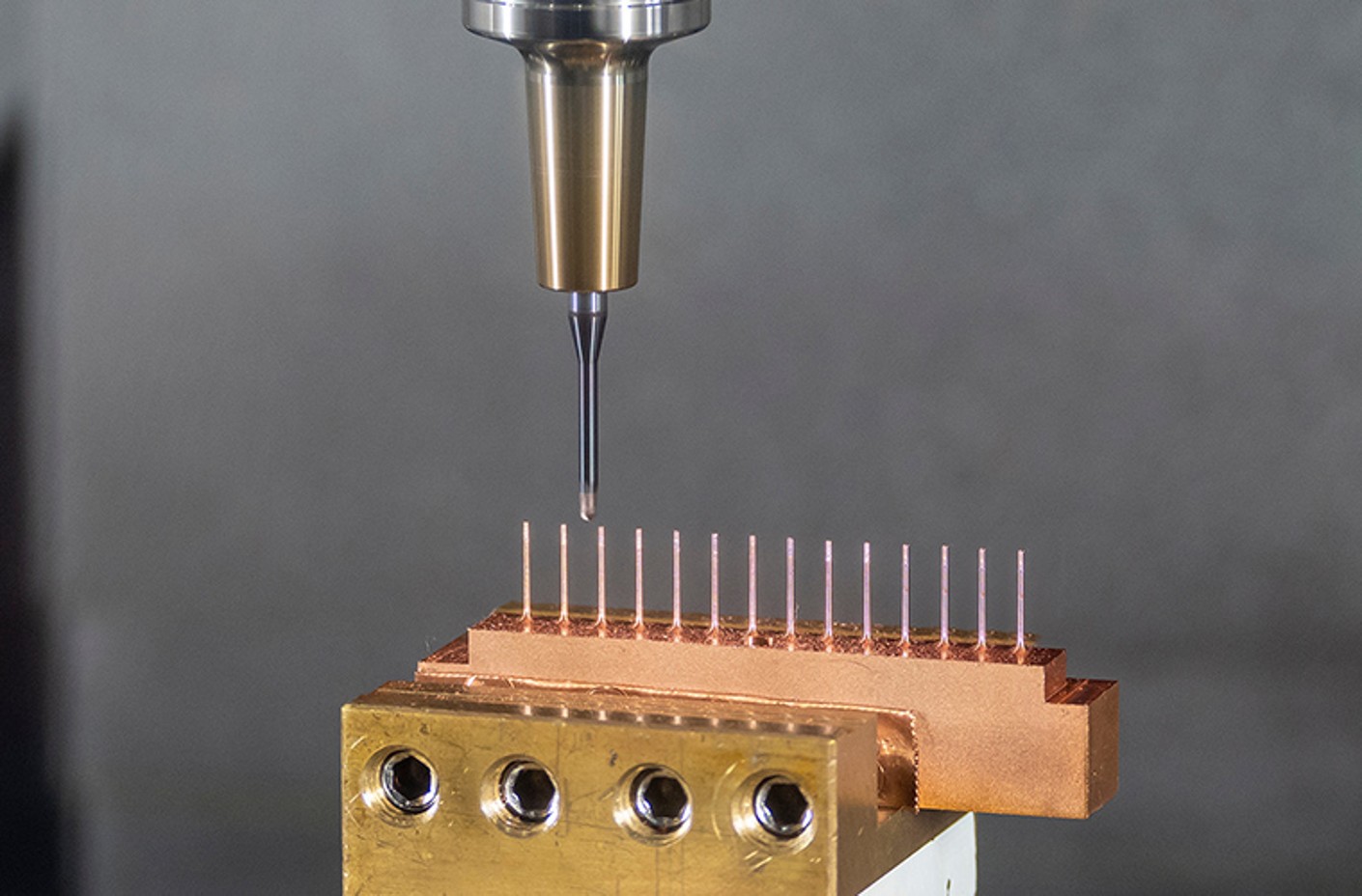
Copper – all that glitters is not gold
When working with copper, alloys that contain Zn, Sn, Al and Si are especially easy to machine. In particular, you will benefit from a favourable chip shape during the machining process.
Important: you can produce even shorter chips by using a copper-zinc alloy that is over 37% zinc. These alloys offer a reduction in toughness with increasing hardness. Copper-zinc alloys are known as “nickel silver”. They are used, for example, to manufacture mathematical drawing instruments and for precision mechanics.
Tip: in industry, copper alloys are mostly classified using the “machinability index”. In Europe, lead-alloyed free-cutting brass CuZn39Pb3 acts as a reference material, with a machinability index of 100.
Definition: the machinability index is an index of the productivity that can be achieved with a material in series production, expressed as a direct comparison with another material.
The German Copper Institute and tool manufacturers provide relevant indices. The following factors affect machinability:
- Tool life
- Chip formation
- Cutting forces
- Surface quality
Where circle-segment milling cutters outperform the ball nose slot drill
Modern mould making is defined by two factors: precision and performance. Everything in tool and mould making depends on how well you, the specialist or master craftsperson, can control these two values when roughing or finishing – especially when performing complex free-form types of milling. Would you like to replace or build on your established ball nose slot drills with new technologies? In that case, newly developed processes such as Parabolic Performance Cutting – PPC milling for short – and deep hole drilling offer new, and above all, more efficient, opportunities. If, alongside precision and performance, you also need to achieve a high metal removal rate, or are faced with the challenge of drilling cross holes or performing stack drilling, then you will be on the safe side with deep hole drilling. Whether drill hole tolerance, shape and positional accuracy, or surface quality – you will have good control of these values, too.
Regrinding carried out quickly
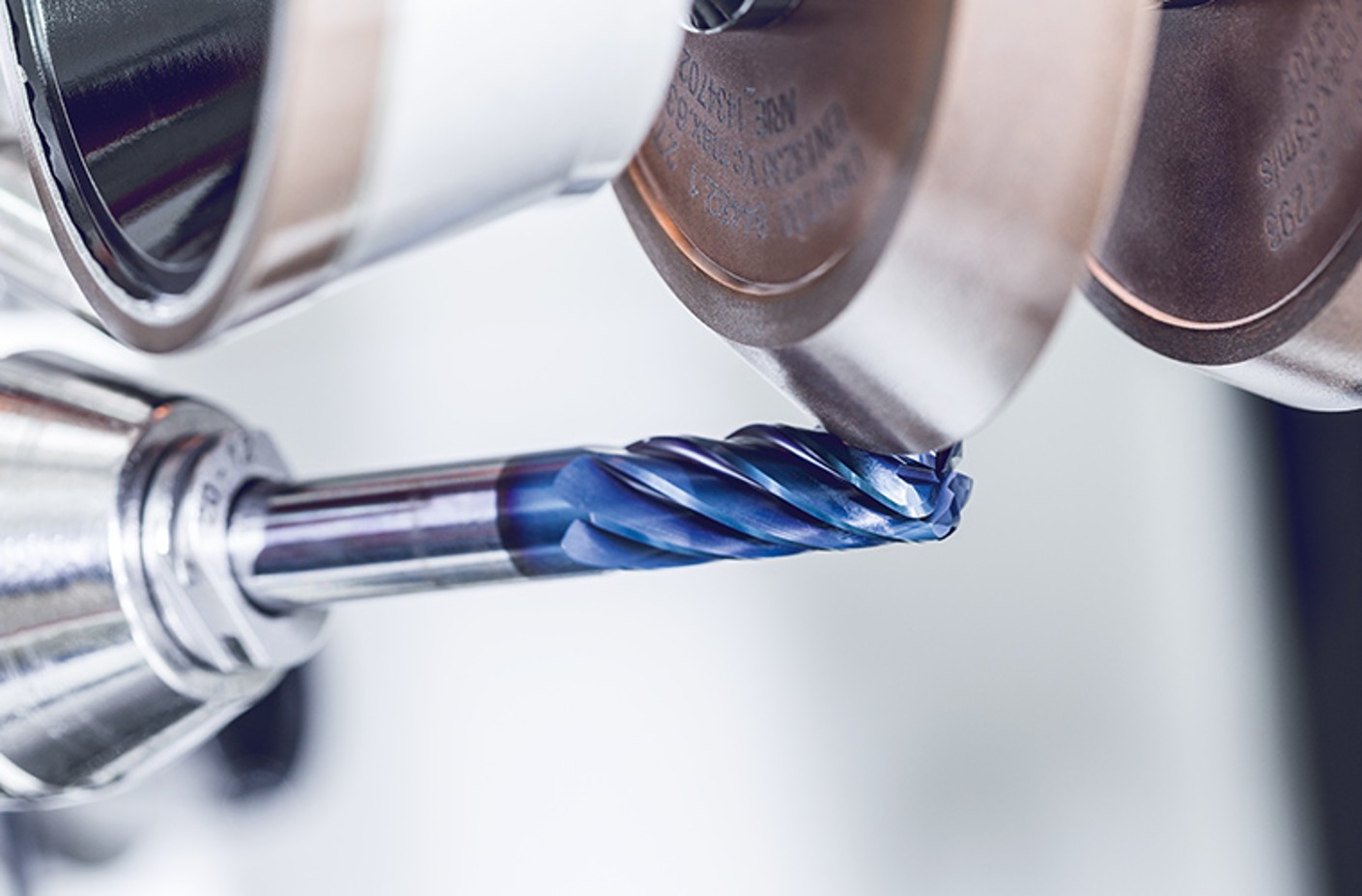
Your choice of machine technology has the largest impact on determining how economically you, as a head of manufacturing in mould making, can perform your tasks, and how cost-efficiently you can manufacture your tools. This must be up to date to meet the increasing demands in terms of dimension accuracy and surface quality and the desire for short machining times. And some things cannot be ignored. Aspects such as thermal robustness or the axis dynamics, as well as static and dynamic disturbance resistance are now important considerations. Finish, geometry and coating are just as important.
If you, the master craftsperson, want to keep using the original manufacturer’s regrind with the original geometry and coating, then our regrinding service is the option for you.