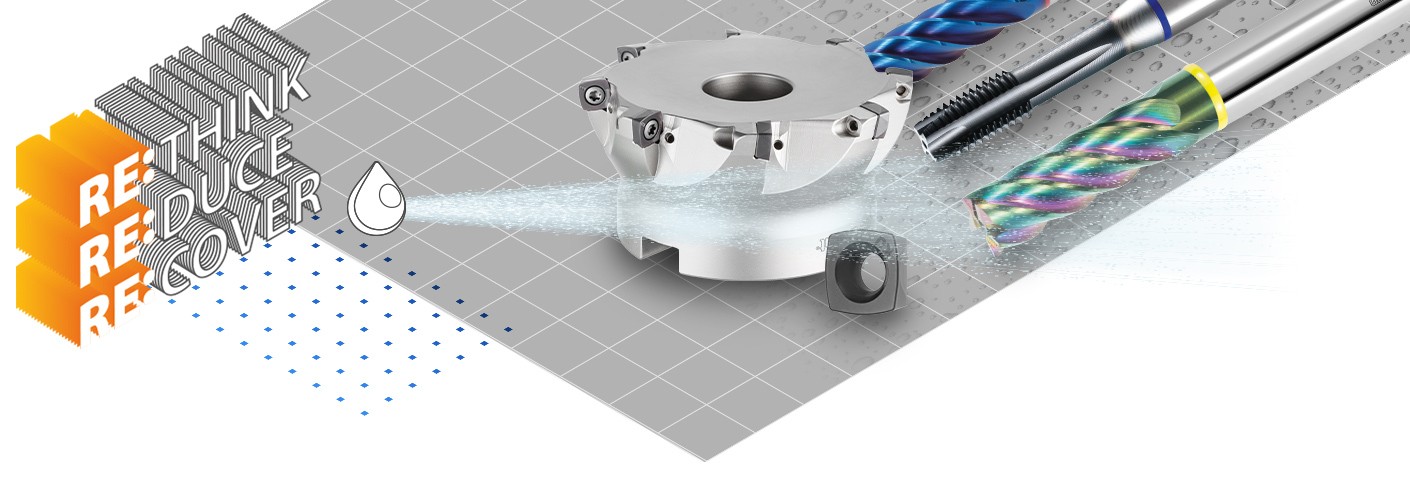
Kühlschmierstoffe einsparen – Minimalmengenschmierung und Trockenbearbeitung
Hohe Kosten bei der Nassbearbeitung
Ob Drehen, Bohren oder Fräsen – spanende Fertigungsverfahren werden vor allem in der metallverarbeitenden Industrie eingesetzt. Für sie spricht das sehr enge Maß- und Formtoleranzen. Fast jede geometrische Form kann gefertigt werden. Durch den hohen Anteil an Automatisierung ist das Spanen außerdem hervorragend für die Serienfertigung geeignet.
Da bei der Zerspanung an der Schnittzone extrem hohe Temperaturen entstehen, sorgen Luft-Öl-Gemische für Kühlung plus Schmierung und helfen beim Abtransport der Späne. Bei der üblichen Nassbearbeitung werden die Werkzeuge mit Kühlschmierstoffen (KSS) umspült. Das führt oft dazu, dass Bettbahnöle mit abgewaschen werden, die den Verschleiß der Maschinenführungen begünstigen können. Zudem ist KSS sehr wartungsintensiv. Prüfung, Entsorgung und Wiederauffüllung bringen auch wieder Folgekosten mit sich.
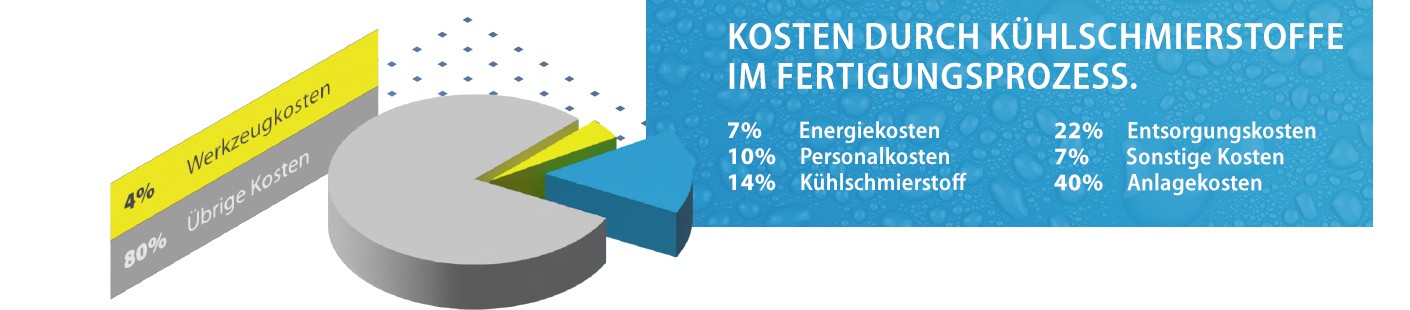
Ein reduzierter Kühlschmierstoff-Einsatz steht schon länger im Zentrum der Aufmerksamkeit, seit der Energiekrise mehr denn je. Tatsächlich betragen die durchschnittlichen Kosten für Kühlschmierstoffe im Fertigungsprozess zwischen 8 und 16 Prozent! Der genaue Anteil der KSS-Kosten ist natürlich stark vom Bearbeitungsverfahren und weiteren produktionsspezifischen Faktoren wie der Größe des Maschinenparks abhängig. Dennoch haben wir hier einen Kostenblock mit großem Einsparpotenzial, der nicht übersehen werden sollte.
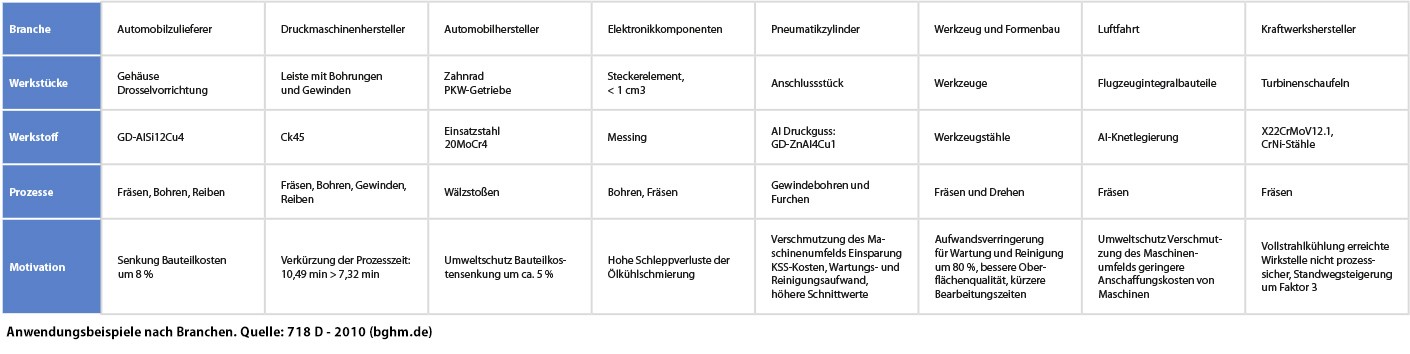
Kühlschmierstoff-sparende Alternativen zur Nassbearbeitung
Trockenzerspanung und Minimalmengenschmierung (MMS) als Alternative zur Nassbearbeitung dürften Ihnen in dem Zusammenhang bekannt sein. Der wesentliche Vorteil der MMS liegt in der Kosteneinsparung bei den Ressourcen Öl, Wasser Energie. Da nicht mehr so häufig entsorgt und aufgefüllt werden muss, wird auch die Produktion seltener unterbrochen.
Hinzu kommt, dass der Wegfall der Vollstrahlkühlung bei der Metallzerspanung meist auch den Wegfall der Thermoschockbelastung der Werkzeugschneide zufolge hat. Damit wird der Einsatz von superharten Schneidstoffen überhaupt erst möglich. Die Folge sind weitaus höhere Schnittwerte und längere Werkzeugstandzeiten.
Jedoch sollte gut abgewogen werden, wann eine Umstellung auf MMS bzw. eine Trockenbearbeitung sinnvoll ist. Nicht immer ist dies ohne Weiteres möglich oder mit hohen Investitionskosten verbunden, die sich erst mal amortisieren müssen. Wenn Sie sich grundlegend über die Möglichkeiten und Grenzen der MMS und Trockenzerspanung informieren möchten, geben wir Ihnen hier einen Überblick. Um den Einzelfall bewerten zu können, empfehlen wir eine Beratung Ihres Lieferanten.
Minimalmengenschmierung – Was ist das?
Eine genormte Definition von Minimalmengenschmierung gibt es nicht. Im Gegensatz zu der Überflutungsschmierung (Schwallkühlung) werden bei der Minimalmengenschmierung nur wenige Tropfen an Schmierstoff zur Zerspanung eingesetzt. Durch eine spezielle Dosiertechnik wird das Medium unter Druck direkt an die Wirkstelle der Werkzeugschneide gebracht. In der Praxis durchgesetzt hat sich, dass bei der MMS nicht mehr als durchschnittlich 50 ml Schmierstoff je Prozessstunde und Werkzeug eingesetzt werden.
Trockenbearbeitung oder Minimalmengenschmierung
Die Begriffe Minimalmengenschmierung und Trockenbearbeitung werden nicht immer scharf voneinander abgegrenzt. Oft wird die MMS auch als „Quasi-Trockenbearbeitung“ bezeichnet. Hintergrund ist folgender: Der Begriff Trockenbearbeitung hat sich mehrere Jahre vor der Einführung der Minimalmengenschmierung etabliert. Generell bezieht er sich auf trockene Späne, Werkzeuge und Bauteile während der Fertigung.
Entscheidend ist hier die Definition von „trocken“. Als trocken gilt, wenn der prozentuale Anteil an Kühlschmierstoff auf dem Span weniger als 2 Masse-Prozent ausmacht. In der Praxis bedeutet das: Es können 80 ml pro Stunde an Kühlschmierstoffe eingesetzt werden, um „trockene“ Späne zu erhalten. Damit fällt die MMS eigentlich unter die Trockenbearbeitung.
Daneben werden mit Trockenbearbeitung auch Verfahren bezeichnet, die absolut trocken verlaufen, also unter Verzicht von Kühlschmierstoff. Wenn im Folgenden von Trockenbearbeitung die Rede ist, gehen wir von einem absolut trockenen Verfahren ohne Verwendung von KSS aus, andernfalls ist die Minimalmengenschmierung gemeint.
Vorweg: Um effizient trocken zu bearbeiten, sind detaillierte Kenntnisse über das komplexe Zusammenwirken von Werkstück, Werkstoff, Bearbeitungsverfahren, Werkzeug, Bearbeitungsbedingungen und Werkzeugmaschine notwendig. Folgende Tabelle gibt eine Orientierung, wo sich Trockenbearbeitung und wo Minimalmengenschmierung in der Praxis etabliert haben. Sie ersetzt nicht die Beratung vor Ort.
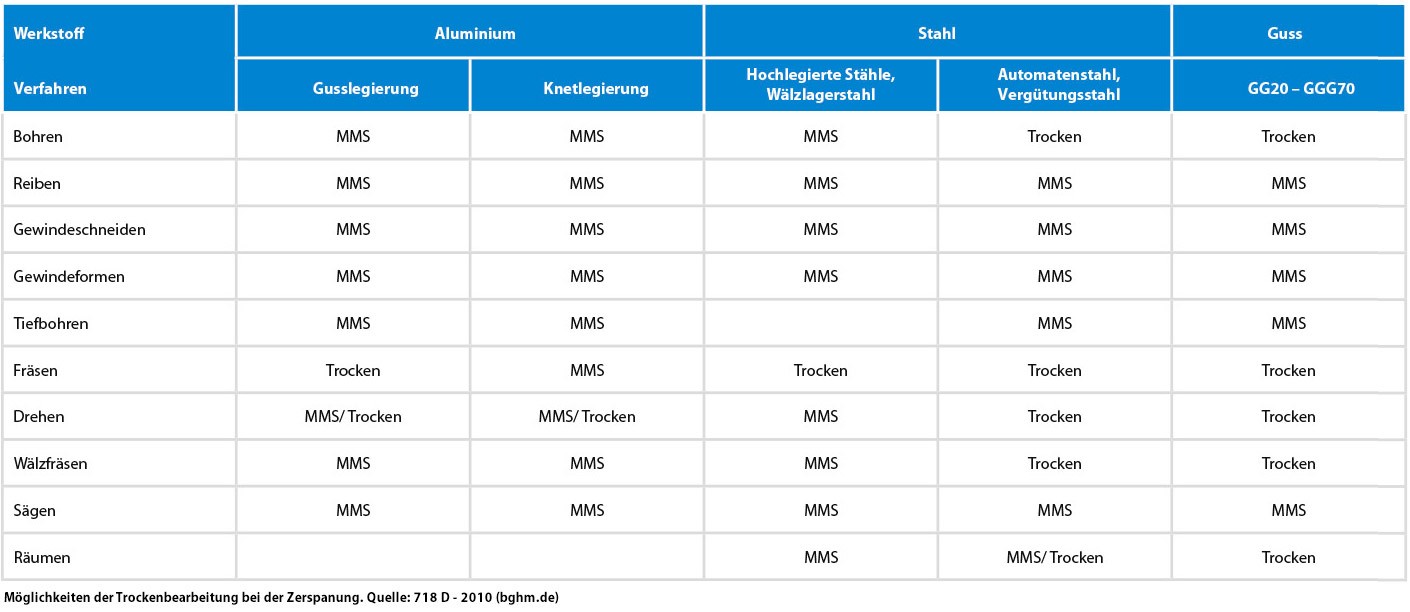
Wie aufwändig ist ein Umstieg auf Minimalmengenschmierung?
Für Unternehmen stellt sich die Frage: Wie aufwendig ist eine Umstellung auf MMS und wann lohnt sie sich? Eine pauschale Antwort gibt es hier nicht. Die MMS erfordert von den Produktionsbedingungen abhängig ein ganz unterschiedliches Maß an Änderungen von Maschinen und Werkzeug. Werkzeugmaschinen wie Kreis- und Bandsägen können zum Beispiel recht einfach zur MMS nachgerüstet werden. Anders sieht es im Bereich des High Performance Cuttings aus. Hier kommt man für die Optimierung auf MMS nicht vorbei an eigens konstruierten Maschinen und darauf ausgerichtetem Werkzeug. Entscheidend ist die Art der Zuführung des Schmiermediums.

Systeme mit äußerer Minimalmengenschmierungs-Zuführung
Bei der äußeren Zuführung wird der Wirkstelle die Minimalmenge durch eine im Bearbeitungsraum der Werkzeugmaschine installierte Düse zugespeist. Die äußere Zufuhr eignet sich zur Nachrüstung von Werkzeugmaschinen und bei Standardprozessen wie Sägen, Bohren, Fräsen und Drehen. Die erforderlichen Sprühdüsen können recht einfach am Spindelkopf angebracht werden.
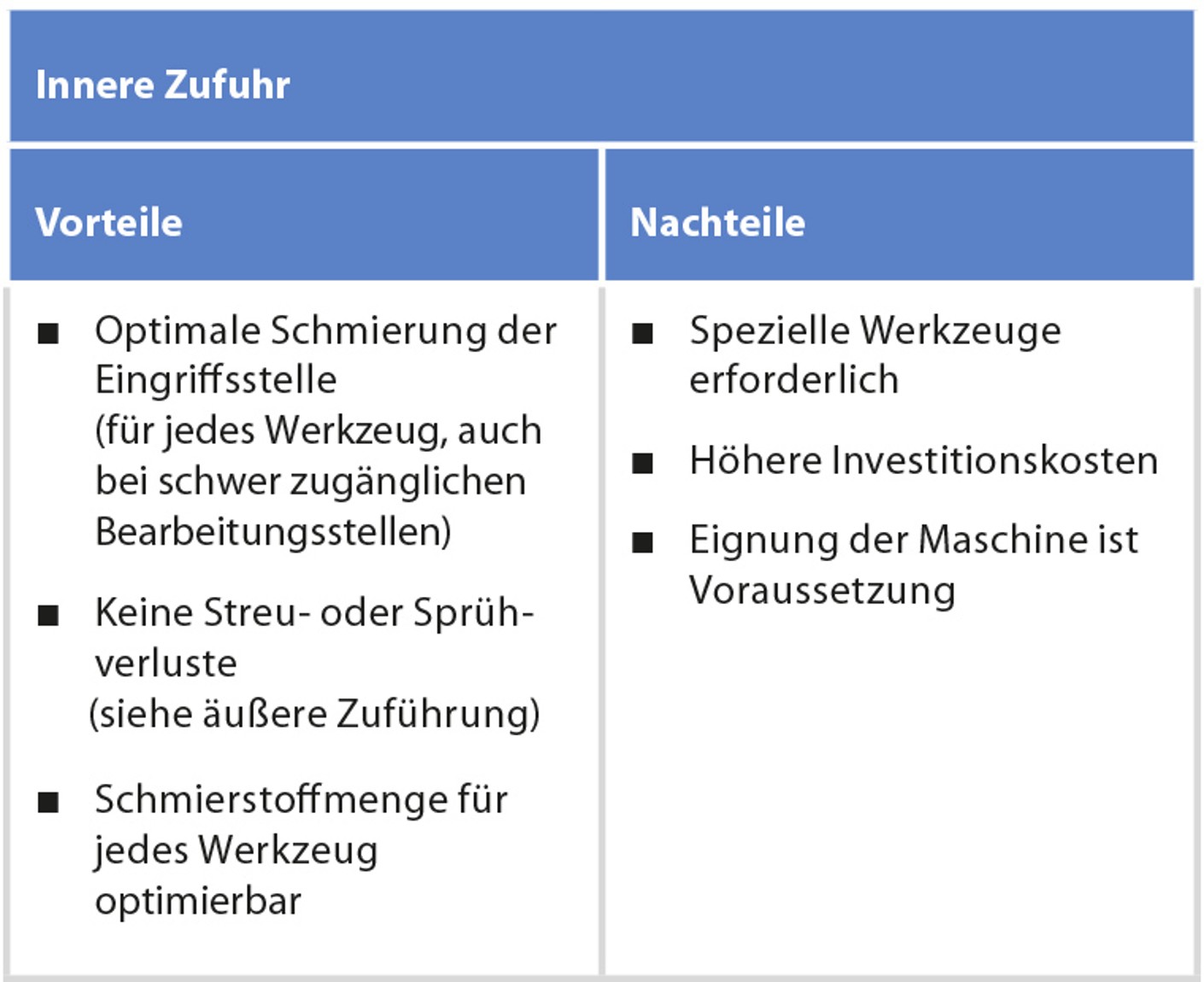
Systeme mit innerer Minimalmengenschmierungs-Zuführung
Die innere Zuführung ist komplexer. Sie erfolgt durch eine Arbeitsspindel direkt bis an die Schneide. Sie wird bei anspruchsvollen Prozessen eingesetzt, da mit ihr eine besonders präzise Zuführung des Aerosols erreicht wird, – nämlich durch das Werkzeug hindurch, direkt an die Wirkstelle. Sie wird während der gesamten Bearbeitung kontinuierlich mit Wirkstoff versorgt. Möglich werden damit sehr große Bohrungstiefen und sehr hohe Schnittgeschwindigkeiten. Jedoch ist eine Umrüstung auf dieses System unter Umständen mit hohen Kosten verbunden. Daher ist eine gute Beratung besonders wichtig.
Wirtschaftliche Vorteile im Überblick
Mit der Reduktion von KSS gehen eine Reihe wirtschaftlicher Vorteile einher. Natürlich sind diese auch stark von den Produktionsparametern abhängig.
- Es sind längere Werkzeugstandzeiten durch optimierte Prozesse zu erwarten
- In Einzelfällen lässt sich bei optimalen Prozessen die Prozessdauer um bis zu 30% reduzieren
- Einsparungen bei Anschaffung, Lagerung und Transport sowie Entsorgung des KSS. Die Späne bleiben trocken und können z.B. als Recycling-Material verkauft werden
- Der Aufwand für Prüfen und Pflegen des KSS fällt weg
- Je nach Anwendung können aufwendige Folgeprozesse wie die Reinigung des Maschinenumfeldes reduziert werden
Ökologische Vorteile im Überblick
- Es fallen keine umweltschädlichen Altemulsionen an
- Havarien durch in großen Mengen auslaufenden KSS sind nicht möglich
- Arbeitssicherheit: Durch ein trockenes Maschinenumfeld wird das Risiko von Arbeitsunfällen gemindert
- Gesundheitsschutz: Mögliche Erkrankungen (z.B. im Bereich der Atemwege oder Hauterkrankungen), die auf Kühlschmierstoffe zurückgeführt werden können, werden vermieden*
- Vorteilhaft ist die Umstellung auf MMS auch bei Maschinen, die längere Stillstandzeiten von Tagen oder Wochen haben. Ein „Umkippen“ der Emulsion kann verhindert werden, die zu Verkeimung, unangenehmem Geruch und zu Gesundheitsgefahren führen kann
Mögliche Nachteile der Minimalmengenschmierung
Nicht immer überwiegen bei der MMS die Vorteile. Auch das ist wiederum sehr vom Einzelfall abhängig und erfordert eine individuelle Beratung. Folgende Nachteile sollten Sie zumindest einmal gehört haben:
- Sollte eine Umrüstung der Maschinen nötig sein, ist mit hohen Investitionskosten zu rechnen
- Durch den Bedarf von Spezialwerkzeuge (siehe folgender Absatz) könnten sich laufende Werkzeugkosten erhöhen
- Bei Einzel- und Kleinserienfertigung lohnt sich eine Umstellung auf Minimalmengenschmierung manchmal nicht. Der Aufwand für die Abstimmung Werkstück, Maschinenparameter, Werkzeug und Schmierung ist oft höher als die Einsparung
- Die Umstellung auf Minimalmengenschmierung kommt nicht für alle Verfahren, Maschinen und Werkstücke infrage
- MMS kühlt nicht. Es schmiert nur und durch die Druckluft werden Späne abtransportiert. Ein Überhitzen von Bauteil und Werkzeug ist möglich
MMS-gerechtes Werkzeug
Da bei der Zerspanung mit Minimalmengenschmierung mit extrem geringen Schmierstoffmengen gearbeitet wird, ist die kontinuierliche Zuführung des MMS an der Wirkstelle besonders wichtig. Mit herkömmlichen Werkzeugen aus der Nassbearbeitung stößt man dabei schnell an die Grenzen ihrer Leistungsfähigkeit. Vor allem mit steigender Schnittgeschwindigkeit ist Sonderwerkzeug und entsprechendes Know-how gefragt.
Anmerkung aus Quelle: 718 D (bghm.de)
*Anmerkung aus Quelle: 718 D (bghm.de): Die Metallbearbeitung mit Minimalmengenschmierung wird in der Praxis als emissionsarmes Verfahren angesehen. Dieser Trend geht auch aus Untersuchungen hervor, welche im Rahmen eines Sondermessprogramms an Arbeitsplätzen mit Minimialmengenschmierung vorgenommen wurden. Hierzu wurden Expositionen (Staub, KSS-Aerosole und Dämpfe) an Werkzeugmaschinen in der Produktion gemessen. Bei diesen Erhebungen kamen jeweils sowohl personengetragene Messungen als auch stationäre Messungen am Bedienpult sowie im Arbeitsinnenraum der Maschine zum Tragen (siehe Bilder 40 und 41) Spalt- und Pyrolyseprodukte, z.B. Formaldehyd, wurden lediglich in Spuren in Einzelfällen nachgewiesen. Auch beim Staub lagen die gemessenen Konzentrationen weit unterhalb der zulässigen Arbeitsplatzgrenzwerte (AGW) für die „Alveolengängige Fraktion“ (AGW: 3 mg/m3 Luft) bzw. für die „Einatembare Fraktion“ (10 mg/m3 Luft). Die Tendenz, dass bei der Minimalmengenschmierung wesentlich weniger Emissionen als bei der Nassbearbeitung freiwerden, konnte mit folgender Vergleichsmessung bestätigt werden. Beim Zerspanen von Werkstoffen mit Minimalmengenschmierung an Werkzeugmaschinen in der Produktion haben sich Kühlschmierstoffdämpfe und -aerosole als expositionsbestimmende Komponenten herauskristallisiert. In allen Messungen konnte eine Einhaltung des ehemals gültigen Luftgrenzwertes für Kühlschmierstoffe (früherer Grenzwert: 10 mg/m3 Luft; Stand der Technik) festgestellt werden. Die gemessenen Konzentrationen in den Arbeitsbereichen waren derart gering, dass mehr als 95 % der ermittelten Messwerte deutlich unterhalb Hälfte des Grenzwertes lagen