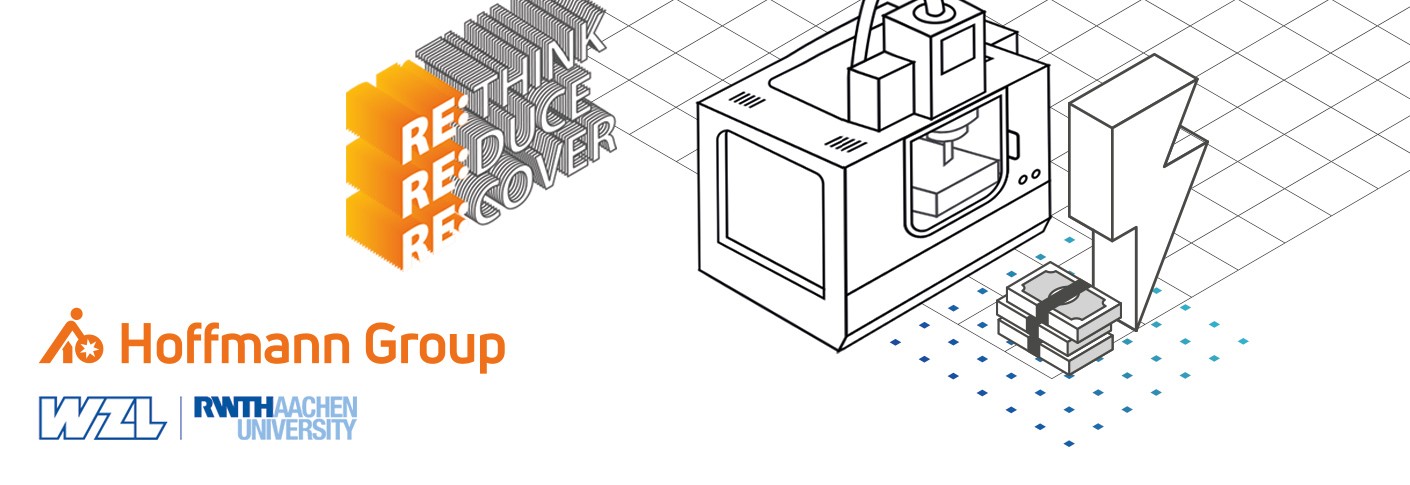
Optimising the production process: how do runtimes play a role?
Energy savings potential for continuous machine operation
On our topics page, we have already taken a deep dive into the different ways of saving energy. Since the start of the energy crisis, the need to optimise production processes in order to reduce costs has been becoming more and more important.
In this article, we take a closer look at what causes unnecessary energy consumption of machines, paying particular attention to their runtimes. To ensure we could work with valid data, the Hoffmann Group tasked RWTH Aachen University to run a series of tests in its tool machine laboratory. We have compiled the most important findings from these tests for you. Click here (PDF) to download the full scientific paper.
The way to identify the leeway a company has for saving costs is to factor out the fixed costs that the company is unable to influence. Some example measurements from a machining centre showed that more than half of the costs for the energy consumed by tool machines are a prerequisite for the machining process to function properly, and are thus fixed costs.
How useful is it to reduce the metal removal rate?
The first question to be considered is whether reducing potential cost drivers can result in the hoped-for lower energy consumption, and whether the savings effect increases even more through further reduction of these cost drivers.
The following example on axis acceleration from the test series makes it clear that this is not necessarily always the case. Analysis of the data with different axis acceleration reduction values showed that the positive effect was limited, and after a certain reduction value the positive effect actually went into reverse.
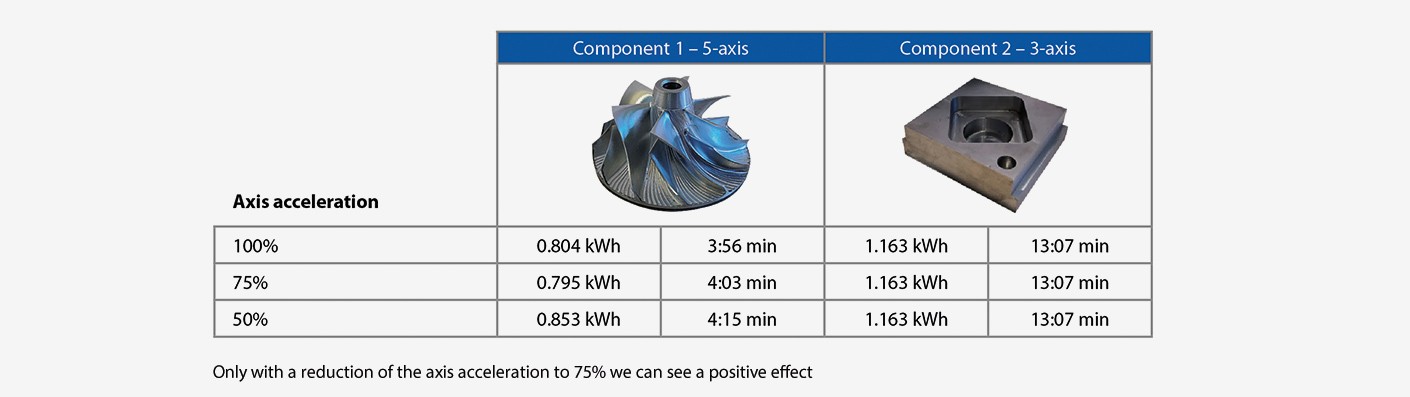
As we can see from the data from the test series, it was only when reducing the axis acceleration down to 75% that the number of kW hours in the energy process fell – although even here only slightly. Reducing the axis acceleration by a further 25% actually increased energy consumption again. This was because the runtime of the auxiliary units increased as a result of the longer manufacturing duration.
As a result, the relatively low amount of energy that is initially saved is lost again due to the longer production times.
Opportunities presented through a high-performance machining strategy
Our analysis shows that reducing the metal removal rate is not always the best option for saving energy, as from a certain range the runtime of the auxiliary units can start to increase. Furthermore, the maximum energy-saving potential of reducing the metal removal rate is relatively limited. The spotlight therefore moves over to improving the machining strategy in order to reduce manufacturing costs.
Save energy during non-productive times through modern clamping devices
The data from the scientific paper clearly shows that tool machines consume a huge amount of energy not only during machining, but also during non-productive times. And this raises the question of how to save energy by reducing set-up times and thus increasing productivity.
A typical way of doing this would be to invest in modern clamping devices, such as zero-point clamping systems, which allow the component to be centred and aligned very quickly. With these systems, the set-up process can also be performed outside of the machine, so the manufacturing doesn’t have to be interrupted. Another example is 5-axis vices, which allow the component to be finished in just a single clamping.
Energy-saving potential of cooling lubricants
We have already dedicated one chapter on our topics page to the energy-saving potential of cooling lubricants. Here is a quick reminder: in the machining process, cooling lubricant supply and coolant preparation account for around 37.3% of energy consumption. So here we have a major energy consumer that can be directly influenced.
The following example from the whitepaper illustrates how high the yearly energy costs of cooling lubricants are:
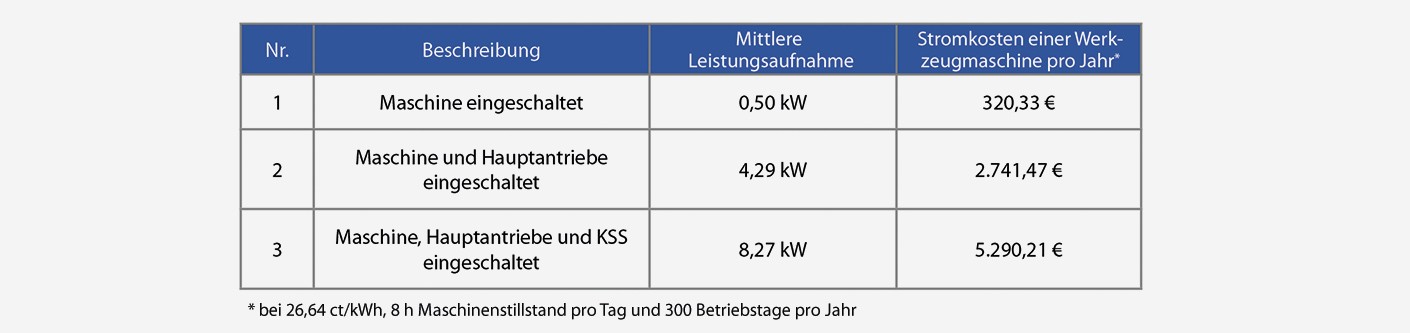
Where possible, dry machining can help to save energy and, depending on the setting, can simultaneously help to improve performance. Around 8 to 16 percent of manufacturing costs can be attributed to the process of supplying coolant to the tool. Even if you only make a partial switch to dry machining, this can already result in considerable energy savings and have a noticeably positive effect on your finances.
The main thing is: continuously supplying coolant lubricants to your machine should be avoided. Expert advice is required if you wish to acquire a bespoke solution. The best approach is to speak to specialist companies in this field. In this context, the Hoffmann Group will advise you solely in terms of the most suitable tools.
Increase your machining capacity instead of switching your machines off
Why not simply switch off the machines during downtimes? Isn’t that the obvious thing to do?
Anyone who makes components that require precision manufacturing will know the answer: this action would result in the machine bed cooling down. This is something that should be avoided on tool machines that have particular accuracy requirements, as otherwise you cannot guarantee quality.
If you are interested in more detailed data, you’ll find corresponding heat curves in the scientific paper. These contrast applications that have particular accuracy requirements with applications where the effects of regularly switching off the machine are within reasonable limits.
It is also important to remember that frequently switching machines on and off can shorten the lifespan of electronic components, such as semiconductor elements or capacitors.
So if a machine is operating continuously, how do you save energy per component? Here you have to start looking at the role of peak loads.
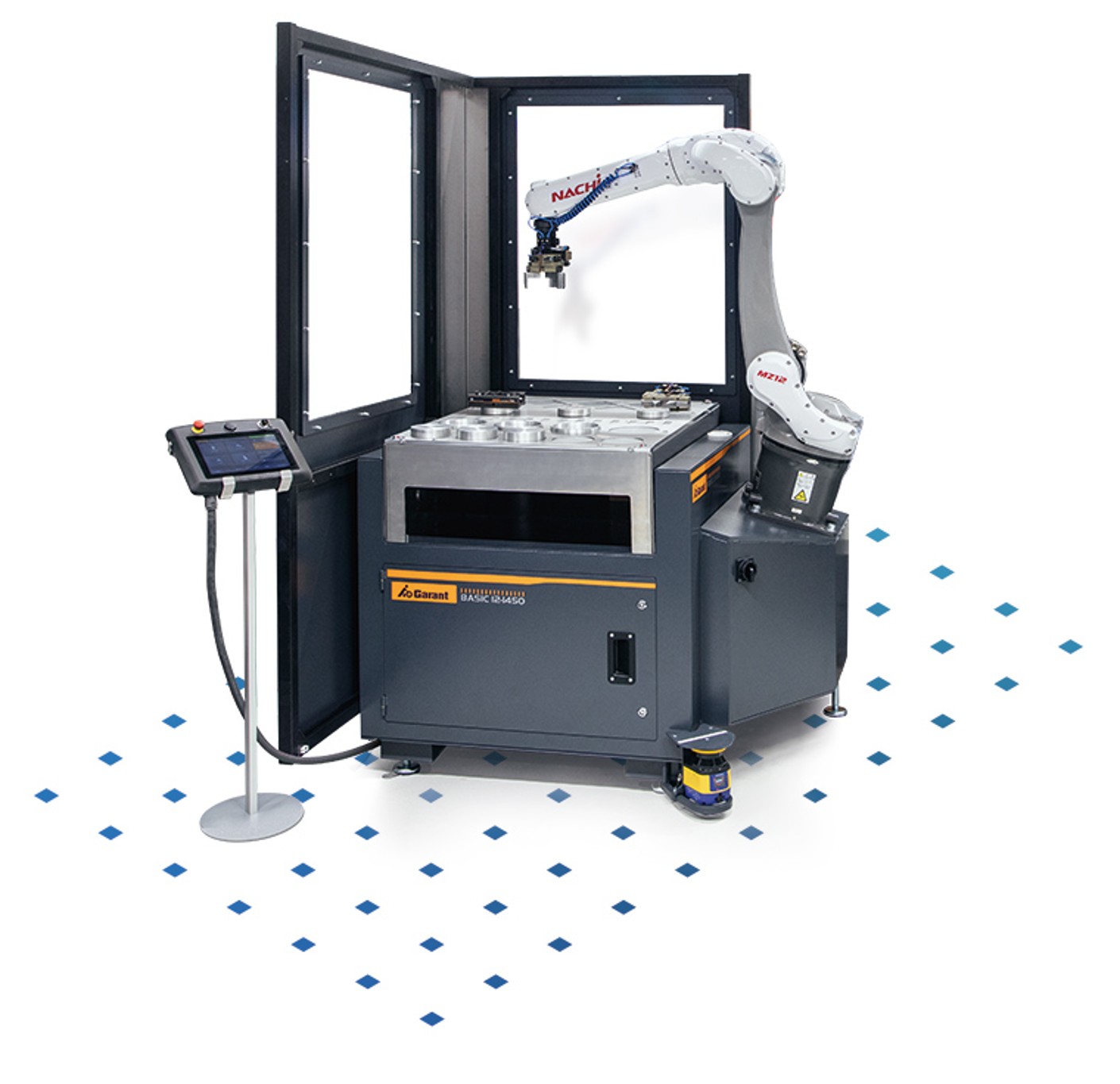
Optimise manufacturing by reducing peak loads
It is a well-known fact that switching on several machines simultaneously (such as at the start of a shift) can result in peak loads, which can significantly affect the electricity tariff. Peak loads often occur when simultaneously starting up several machines that consume a lot of energy after being switched on*.
There are two possible ways of addressing this: one way is to introduce a third automated shift. Read our whitepaper to find out more about this.
The other approach to reducing peak loads is to use digital production solutions. Further information will soon be available on our topics page, which we will inform you about in our newsletter. If you have not yet signed up to our newsletter, you can do so here.
*Source: Peak load management: how to reduce energy costs (mvv.de)
Would you like to know all the background information?
Then why not download the scientific paper from RWTH Aachen University and find out more!