Higher process reliability and shorter set-up time
“The first impressions of GARANT Master Tap showed it to be a high-performance tap which delivers high process reliability in a range of applications.”
Stefan Wagner, tool management at Krones Nittenau
Krones AG is headquartered at Neutraubling, Germany, where it designs, develops and manufactures machines and complete systems for process industries, bottling plants and packaging plants. Around the world, every day millions of bottles, cans and moulded containers are filled using equipment supplied by Krones AG. Whether it’s beer, soft drinks, wine, jam, cough mixture, washing lotion or engine oil – if it’s filled or packed there’s a good chance that Krones equipment is involved. In Germany it’s one bottle in every two, worldwide it’s one bottle in every four. The group includes not only Krones AG but also 90 sales and service subsidiaries at home and abroad.

Internationally competitive
The Nittenau location is the Krones AG centre for production and assembly of filling, labelling, plastic and process technology. This is a classic customised machine building operation. That means each machine is either specially designed to customer order or is manufactured as part of a small series. “Around 90 percent of our products are exported”, says Stefan Wagner, who works in tool management at Krones Nittenau. “Despite this we develop and produce our machines here in Germany. That’s because here in Nittenau we have a globally competitive position which we have gained by rigorous application of technology and automation. Our range of very modern machine tools puts us in the position to deliver on time despite tight delivery deadlines.” In order to maintain its technological edge, Krones AG regularly engages in research and development and invests in trying out new production processes and tools. “The introduction of new tools is a costly business, because it means we have to change the data in all our IT systems, databases and machine control programs”, explains Wagner. “Therefore before we commit to such a change we perform intensive tests on each tool.”
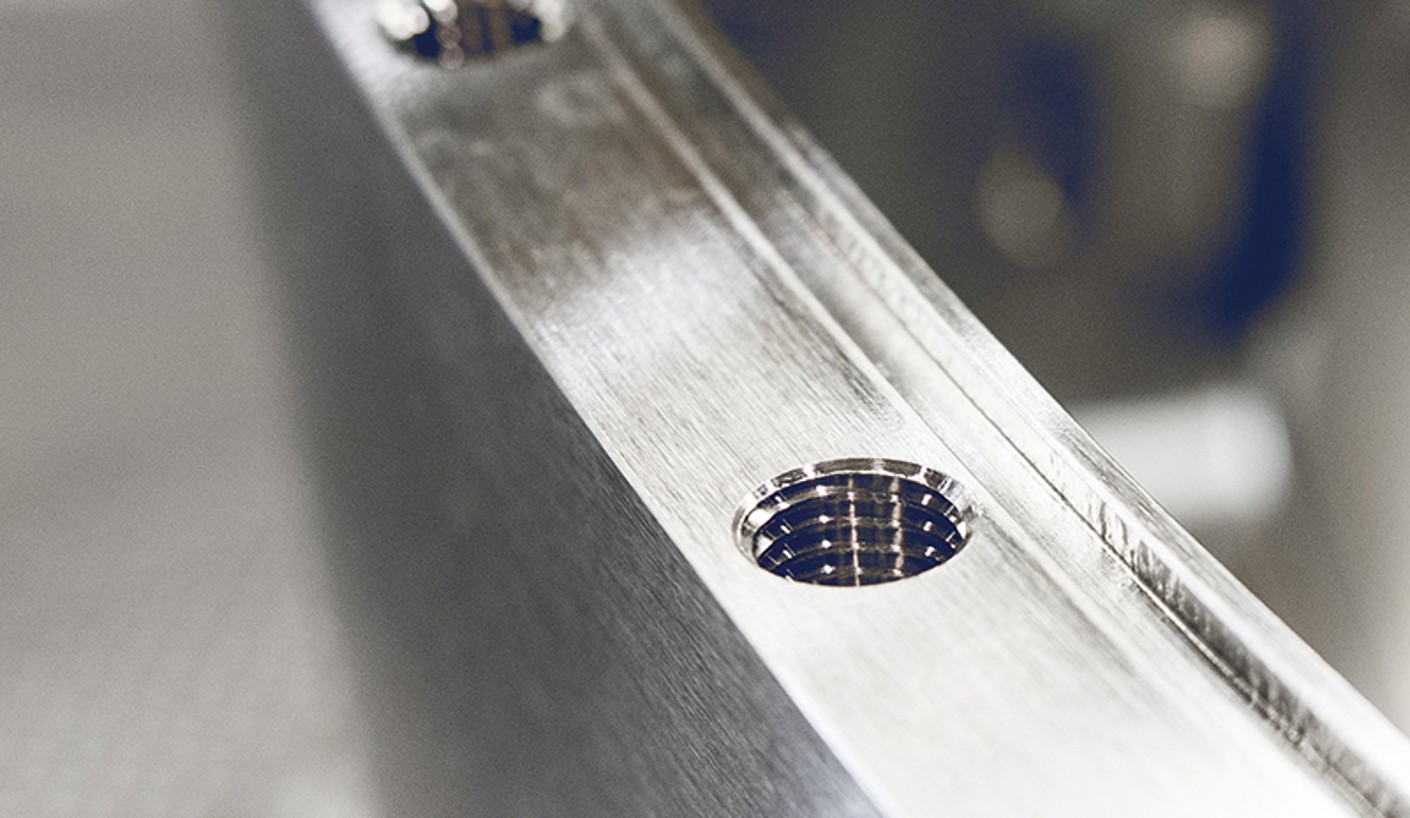
General purpose tap for a wide spectrum of applications
When the Hoffmann Group brought out their new ‘GARANT Master Tap’ general-purpose high-performance tap‚ Krones immediately set up a test program for it. The GARANT Master Tap is designed to perform with high process reliability in a range of different materials such as steel, stainless steel, aluminium, brass and cast iron, thus replacing several other taps on a machine. The tap has new cutting edge geometry, optimised chip flutes and a special configuration of tooth rear face geometry which chops the swarf off at the root and evacuates it with high process reliability. The tap achieves a long working life even when tapping high-tensile steel, because its cutting edges are honed and thereby protected against breakage. Tool material of high-quality HSS-E-PM and an ultra-smooth AlTiX high-performance coating prevent material adhesions and galling. They permit high cutting speeds, even in wrought aluminium alloys. “When the new ‘super tap’ was announced, our ears pricked up, because during production of steel rings for carousel systems we continually encounter problems with twisted swarf, and during production of small components we constantly have to change taps”, explains Wagner. Stainless steel filler rings up to 7 metres diameter are made at the Nittenau works. Each ring requires hundreds of tapped holes for attaching valves; tapping all these holes can take several hours. Process reliability is particularly important for this operation.

Avoiding machine stoppages and tool changes
Because the machines are for use in the foodstuffs industry, it is mainly stainless steel that is processed in Nittenau. The requirements for surface quality are high, and only a few processes are permissible. “Because there will always be vibration when machining these large rings, the only thread generation process we can accept is tapping“, explains Wagner. “Our designers call for 20 millimetres tapped depth, that’s almost twice the depth usually required. This caused us constant problems with swarf evacuation. The machine would run for twenty holes at most. An employee then had to stop the machine and strip out the swarf. Our business model simply can’t afford such downtime, because of the resulting increased costs.“ A high-performance tool such as the GARANT Master Tap promised to solve precisely this problem. The Master Tap also had the potential to optimise the production of countless smaller components: “As well as the large steel rings we also make smaller components. Most of them are of stainless steel, but some are of aluminium and cast iron. Machining these various materials meant we regularly had to change the tapping tools – this was really time-consuming.” So Krones didn’t just test the GARANT Master Tap on tapping the stainless steel rings, but also on a variety of different materials.
After about 3 weeks both the initial tests on the tools had finally been completed. The results were impressive:
“When tapping stainless steel rings, the GARANT Master Tap chopped the swarf off cleanly at the root, so we no longer had to stop the production process to clear swarf. That saved enormous amounts of time and increased the available time for the machine. For the small components on the other hand we used just a single GARANT Master Tap to tap well over 360 holes – and this working at increased cutting parameters at the same time. With the previous taps, because of the large tapped depth and the resulting swarf evacuation problems, for the same number of tapped holes we needed up to 9 taps to do the same amount of work..”
Stefan Wagner, tool management at Krones Nittenau
So the GARANT Master Tap has passed its acid test. The Master Tap was tested by Krones in the Nittenau works on other machines in sustained use.